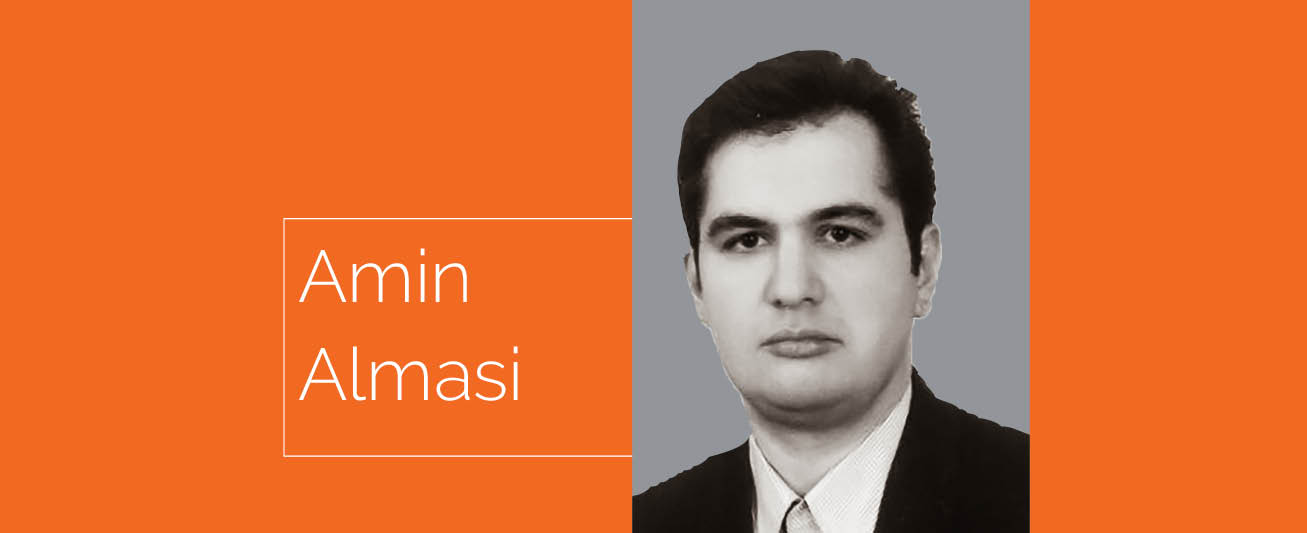
Operation at a flow rate lower or higher than the best efficiency point (BEP) flow rate is not efficient nor desirable. However, this might happen in transients and unexpected cases. The operating point would move on the pump performance curve depending on what happens in downstream and upstream, and if the situation is not managed properly, the operating point might be far from BEP. Running at an operating point far from BEP could be problematic. The goal is to keep the operating points at or around BEP regardless of disturbances in upstream and downstream. Pump control and monitoring should receive attention in this regard. Particular attention is required for operating toward the shutoff point (or at low flow rates). This article discusses practical operational aspects and nitty gritty details of BEP and its relation to the sizing, selection, control and operation of pumps.
BEP & Sizing/Configuration
Pump selection/sizing starts with acquiring detailed knowledge of the downstream and upstream systems. The suction pressure, discharge pressure, required head, flow rate, net positive suction head (NPSH) and other key parameters should be identified or calculated for pump selection.
The first step in the selection and sizing of a pump is to determine the type and number of stages that are needed to meet the given set of operating conditions, usually flow rate range, head, NPSH available (NPSHa) and others. If the pump should meet several such sets of operating conditions, then ideally one set should be chosen as the rated point. This point is to be located as close as possible to the BEP of the pump. All the other operating points should be within acceptable operating range of the selected pump. In other words, they should be sufficiently close to BEP. Making the proper selection may require some iteration. This means the pump with proper performance curve and details should be selected. First, one should make a trial choice, do a preliminary selection/sizing, and then determine the corresponding pump performance curves, operating range, distances to BEP and repeat these steps if necessary.
Considering impellers, there are close-type impellers, semi-open impellers and open-type impellers. Nearly all pumps in process services and, generally, most pumps in different industries use closed-type impellers. A closed-type impeller is usually more efficient than the other impeller types (semi-open or open-type impellers) because a closed-type impeller properly contains the flow of liquid. Also, this type of impeller is mechanically more robust and reliable. A closed-type impeller is a preferred impeller for many services, particularly critical pump applications.
The ability of a pump to run smoothly with minimal excursions and oscillations of flow rate (capacity) and pressure (head) depends on the shape of the pump’s
head-flow rate performance curve and the characteristics of the system in which it operates. In other words, how do these two curves intact in different situations and operating cases? And how close is the operating point to BEP in all different situations?
BEP & Head Rise
The continuous head rise from BEP to shutoff is important. Another important aspect is the value of the head rise from BEP/rated point to shutoff point. If this head rise is relatively large and the pump curve is sufficiently steep, then a slight rise of the required head would not push the operating point far from BEP. In this way, the required head rise would be produced just by a small adjustment while the operating point is still relatively close to BEP. The head rise from BEP/rated point to shutoff should be at least 8%. Some pumps such as American Petroleum Institute (API) 610 pumps or pumps in parallel operation should have more than 10% of the head rise from rated point/BEP to shutoff.
Toward Shutoff Point
A pump should not be operated for long periods of time at or near shutoff point (low flow, maximum head). Transient operation near shutoff point might happen due to disturbances or mistakes in operation—for example, closing a main valve in the downstream by error, etc. For some pumps, this operation near the shutoff point should be limited to 15 to 40 seconds. In some pumping systems, a dedicated pressure instrument/switch may be set up to shut the pump down when the pressure is high (low or no flow). More sophisticated measures and controls should be used for complex and critical pumps to avoid operation at or around shutoff point.
Most pumps should not be operated at a flow rate less than a certain level. This is usually known as minimum continuous stable flow. As a rough indication, a pump should not be operated at flow rate below 60% of the flow rate at BEP without a recirculation line or similar means. Some factors that determine minimum stable flow include the following:
- Temperature rise of the liquid. The limit on the temperature rise might be assumed as 8 C or 10 C. If a pump operates at very low flow rate, it could overheat.
- Radial hydraulic thrust on impellers. This is a serious matter. Even at flow rates as low as 60% of BEP flow rate, this rise in the force/load might reduce the life of bearing(s). The large forces might lead to excessive shaft deflection, seal failures, impeller rubbing, shaft breakage and others.
- Flow recirculation in the pump. This may lead to noise, vibration, cavitation and mechanical damages.
If a lower flow rate is needed, a recirculation line or another capacity control method such as a variable speed drive (VSD) should be used. This provides overall low flow while the pump is still operating at or near BEP.
Toward High Flow Rate
Operation at a high flow rate, right hand side of BEP near the end of curve, could also be problematic. A pump would be noisy and vibrate excessively near the end of curve. The efficiency is low and the pump would consume lots of power at this region. The operation is unstable and ineffective.
Control & Operation
Many pumps require operation at different flow rates and pressures (heads). A pump will deliver only the flow rate (capacity) that corresponds to the intersection of its performance curve and the system head’s curve. To vary the flow rate, something should be changed—ideally without moving the operating point away from BEP. This can be done through different control methods such as using control valves, variable speed, etc.
The key is to have desired flow rate and head while the pump is still working near its BEP. How to achieve this goal is the art of proper control and operation.
Constant-Speed Pumps
Because many small or medium centrifugal pumps are driven by constant-speed electric motors, throttling using control valves is the practical method of regulating flow rate (capacity) and head. The backpressure produced by a control valve (or throttling valve) imposes a variable amount of loss on the system head curve. Closing the control valve increases control losses and causes the system head curve to slope up more steeply to intersect the pump head/flow rate curve at the desired higher head and lower flow rate. Opening the control valve decreases the control losses and causes the system head curve to slope downward and intersect the pump head-flow rate curve at a higher flow rate and lower head.
VSD Pumps
Many large pumps have been variable speed driven pumps. The variable speed operation can keep the operation around BEP. In other words, it can maintain nearly the same pump efficiency over wide ranges of flow rate and head. In simple terms, it adjusts the speed and other parameters in a way that the pump operates near BEP while producing a different flow.