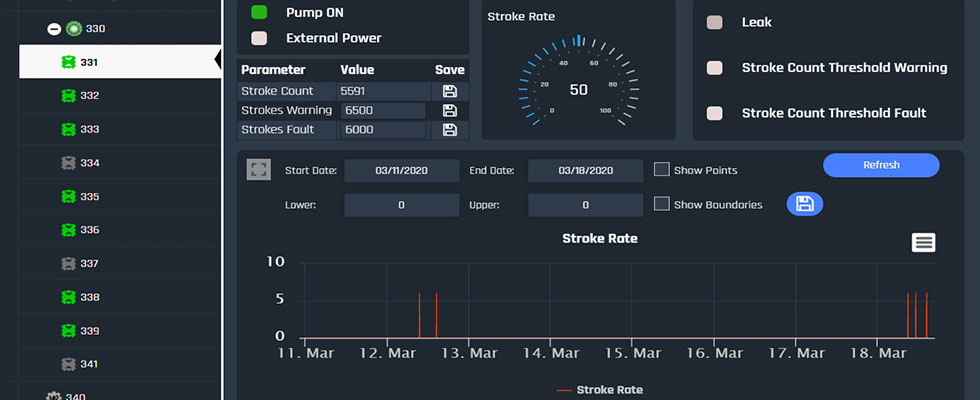
In the old days, “run to failure” was a popular approach that some operations teams at manufacturing and processing facilities took to the operation of their heavy machinery. In other words, they would plug in a machine, such as a pump, turn it on and let it run until it could not run anymore, then replace it with a new model. The pump always seemed to break down at the most inopportune moment, but there was no reliable way to know when a breakdown may be on the horizon.
That mindset began to change when it started becoming more and more harmful to the processing operation to intentionally allow pumps to fail. There were six drivers behind this change in approach:
- Companies began to recognize the true cost of equipment downtime.
- Unreliable or breakdown-prone equipment could pose health and safety risks to employees.
- The cost of employing a large, full-time maintenance team was too high.
- The equipment was getting more expensive to purchase.
- Capital investment budgets were getting tighter.
- Regulatory agencies began to take a much stricter look at the effects that leakage of hazardous and dangerous products could have on site personnel, surrounding communities and the environment.
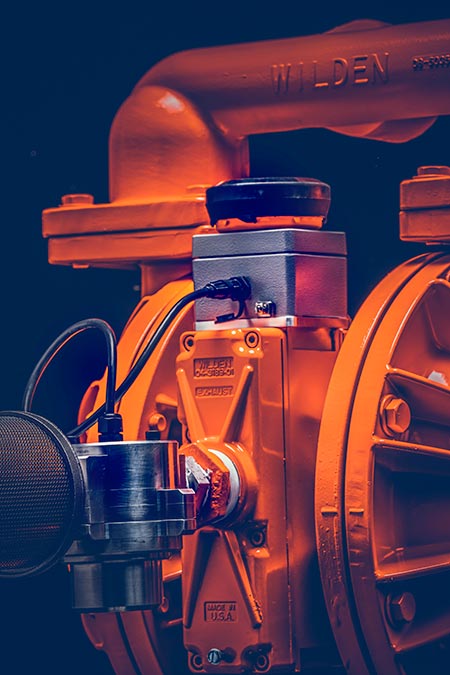
An Ounce of Prevention
The cure to this new world order within the processing plant became what is now known as “preventative maintenance” (or “preventive,” to some). A preventative maintenance routine revolves around the creation of a schedule—typically three, six or 12 months—for periodically inspecting industrial equipment. During these regularly scheduled inspections, the operator is looking for any signs that the overall piece of equipment or any of its components are beginning to wear to a point that they may soon fail and cause a breakdown.
For pumps, a typical preventative maintenance inspection would target any component that was considered a wear component, such as seals, gaskets, bearings and valves, for signs of degradation. Additionally, the rotor would be inspected to make sure it was still operating properly with the casing, and the flow path was checked to see if any performance-altering grooving or galling had taken place. If excessive wear is indicated on any part—or if the pump is no longer operating as expected—the worn parts can be changed out or, in extreme cases, the pump can be taken out of service and replaced with a new model.
The creation and refinement of preventative maintenance routines have been a boon for plant operators as they can get a better view of how their pumps are operating and take steps to thwart unplanned and costly downtime. One type of pump technology—air-operated double diaphragm (AODD)—is typically not the subject of a preventative maintenance plan. In many instances, AODD pumps, in a throwback to the good ol’ days, are allowed to run until failure with the operator hoping nothing bad happens—product leakage that leads to costly cleanup, safety hazards, loss of product and, by extension, revenue—before the pump actually stops operating. Or the plant operator may decide the AODD pump’s wear components (diaphragms, gaskets, balls, ball seats) will be replaced after a certain period of time no matter how they are performing. In this case, the wear components may still have many more months of life in them, so replacing them too soon can result in excessive maintenance costs, downtime, product loss and an oversupply of parts.
Another challenge for the operator is there may not be a good, reliable record of the AODD pump’s operational history. This includes how long the pump has been in operation and when maintenance was last performed. The operator may also not have visibility into how the pump has been operating—for example, whether its performance has been at, above or below expectations.
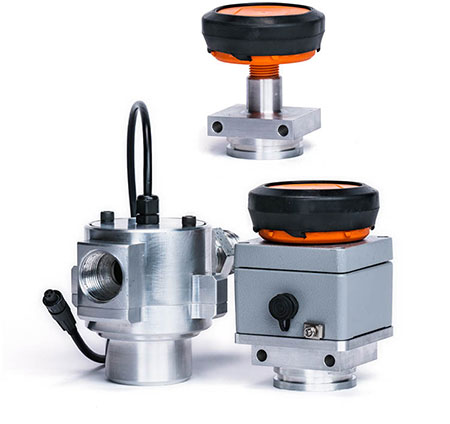
Remote Diagnostics
AODD pumps may be their own worst enemy, mainly because the simple design, few moving parts and method of operation make them a “set it and forget it” piece of machinery that provides the user with a flexible, reliable and resilient solution for use in tough operating environments. These capabilities have often made the AODD pump an afterthought in the development and installation of advanced diagnostics and cloud-based performance monitoring.
Now, however, AODD pumps are just as eligible for remote diagnostic performance monitoring as any other pumping technology. This has led to the creation of new systems that use embedded communication technology to share the AODD pump’s operational intelligence. This technology enables the identification of operational inefficiencies within the pump’s performance sooner and more reliably, creating real-time operational transparency and cost savings for the operator through continuous cloud connectivity.
Specifically, AODD pumps have a number of component and performance parameters that can be measured via remote diagnostic monitoring technology, including:
- wear parts—diaphragms, balls, ball seats, air distribution system (ADS) components—that can break down over time
- diaphragm failures that need to be sensed and reported as soon as possible in order to prevent catastrophic product leaks
- prediction of a diaphragm failure is critical to ensure minimal downtime; quick identification is potentially the difference between total loss of the pump or a less costly repair/replacement operation
- excessive dry-run conditions that will compromise the pump’s performance, overall life span and increased energy usage
- operational impediments such as clogged pipes, air leaks and closed or faulty valves that can adversely affect the pump’s expected performance
This diagnostic pump-monitoring technology also can communicate directly with the operator, while compiling operational information that can be used to predict when a breakdown might occur or preventative maintenance might
be required:
accumulation and storage of performance data, including stroke rate and stroke count, which identify abnormalities in performance and overall pump life, respectively
a reduction in operational performance that can be reported to the operator in real time
historical performance data that gives a clear indication of how long the pump may/can remain in service and when it might require maintenance
Since every AODD pump system and installation is different, building an effective preventative maintenance plan requires that strict attention be paid to a critical set of operational variables, including the age of the pump, along with a history of how long this pump style has typically performed in the specific application; average service time of diaphragms before they fail; and typical costs for spare parts, which can streamline inventory requirements and help lower capital costs.
In terms of hardware, the remote-monitoring system consists of a battery-powered stroke sensor and transmitter that is installed directly on the AODD pump. This sensor collects and analyzes pump-performance data in real time and transmits it to a central gateway for encryption and transmission to the cloud. Once stored on the cloud, real-time and historic operational information can be accessed by the user anywhere through a secure smartphone app or an online portal.
AODD pumps can play a role in a preventative maintenance routine by incorporating remote diagnostic performance-monitoring technology. This digital, cloud-based pump-monitoring system uses diagnostics to give AODD pump users the ability to know exactly how—at anytime and from anywhere—the pumps are operating and if any performance-related issues may be looming on the horizon.
Seeing Is Believing
The use of new cloud-based remote diagnostic performance-monitoring equipment and systems for AODD pumps can pay dividends for users in a number of important industries. Here’s a look at three hypothetical examples:
- A large ceramics manufacturer with more than 100 AODD pumps in operation was incurring exorbitant maintenance costs from replacing diaphragms every six months, no matter their condition. After installing a new remote diagnostic performance monitoring system, it was determined that the diaphragm-replacement cycle could be extended to 12 months. This is expected to save the plant $40,000 annually in parts costs and $8,000 per year in labor costs.
- The diaphragms on a yogurt manufacturer’s AODD pumps were being punctured by foreign objects. In one case, this led to air intrusion that saw the loss of 9,600 gallons of finished product, which was unable to pass a final quality check. Installing a remote monitoring system would have saved the manufacturer $57,600 in lost product and $96,000 in lost revenue.
- A facility that produces 5 million gallons of paint annually uses a fleet of AODD pumps that are located in a remote corner of the production plant. A single pump failure led to the emptying of a 5,000-gallon tank onto the floor. Added together, the costs for lost product ($16,000), cleanup ($4,000), labor ($3,000), equipment replacement ($1,000) and hazmat disposal ($5,000) meant a total loss of nearly $30,000 for one spill accident. Installing a remote monitoring system would have prevented that leak by identifying when potential failures might occur and notifying the operator that a breakdown was looming.
These are just a few examples where a next-generation AODD pump monitoring system can curb component damage and leaks that lead to thousands of dollars in lost product and revenue, along with associated equipment, cleanup, disposal and remediation costs.