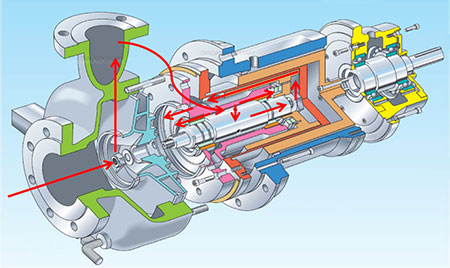
The caustic regeneration loop that ensures the removal of the total sulfur from natural gas liquids (NGL) at a gas plant has two lean caustic circulation sealless pumps. These pumps are responsible for delivering the lean regenerated caustic with natural gas (naphtha) from the disulfides separator to the natural gas wash settler.
Review of the Pump Design
These pumps are 178-horsepower (hp) sealless magnetic drive pumps with a rated flow of 294 gallons per minute (gpm) and total differential head of 638 feet (ft). The process fluid is totally contained inside the pump containment shell and depended on to remove the generated heat through internal lubrication paths.
Therefore, any slight restriction to the lubrication flow paths will jeopardize the condition of the pump’s internal parts, resulting in catastrophic failure. Additionally, the fluid runs between the inner magnet, the containment shell and through the shaft holes to the rear of the pump shaft where it returns to the pump’s suction through the thrust balance hole in the impeller (Image 3). The pump shaft that is connected to the inner magnet is rotated by the action of the magnetic flux circuit between the inner and outer magnet. The outer magnet is coupled to the driver motor through another shaft to transmit the rotation to the inner magnet.
Background Information
Within normal operating conditions, the pump was tripped due to the motor thermal overload fault signal. All process conditions were checked and found within normal parameters. Later, the pump was started again and immediately tripped on the stalled motor fault signal.
The decision was to remove the pump for dismantling and internal inspection. The major findings include:
- There was excessive rubbing between the impeller front cover and the pump casing. Also, there was thinning on the impeller shrouds. This is an indication of high thrust movement as shown in Images 1 and 4.
- Rear thrust pad, thrust washer and sleeve bush were not found in place. The silicon carbide bearings had failed and its traces were found inside the pump casing (Images 2, 5 and 6).
Investigation & Findings
A conclusion was reached based on the above inspection findings, operational trends, caustic lab sample analysis and metallurgical analysis. Material analysis showed that grains of the titanium sleeve bush were colored blue, consistent with the newly introduced process catalyst in 2019. This was considered a sign of a corrosion reaction.
It is suspected that the catalyst has filled the standby pump and when it is not in operation, the pump would have been unable to disperse the liquid. The product would have then attacked the front sleeve bush as this is mounted in the casing volute, whereas the rear sleeve bush is in a less accessible area of the pump.
Occasionally, the process is subjected to high caustic concentration. Material analysis shows that there should be an accelerated rate of corrosion of the titanium sleeve bush carrier in the instances where the pump is exposed to the higher 40% to 50% caustic concentrations.
As shown in Image 6, it is suspected that the corrosion and loss of the titanium sleeve bush circumferential were enough to allow the bolts to lose the grip between the bush carrier and holder. Hence, all the bush carriers became free to move radially and axially, leading to thrust pad and thrust washer silicon carbide to shatter. The failure of the rear thrust pad and thrust washer (active bearing) increased the negative thrusting and axial movement of the whole rotor toward the pump casing. This resulted in heavy wear on the casing, impeller and radial bush failure.
Recommendation
The impact of the intermittent 50% caustic concentration and the new catalyst type corroded the titanium part, resulting in thrust bearing failure.
The user confirmed that the use of titanium is not a common selection but it was requested by the user during the project design. In addition, the other pump components are made of duplex stainless steel and did not experience any corrosion attack. As per the findings, the user’s experience and the corrosion chart, it was recommended to upgrade the bush housing material to duplex stainless steel material.