Keeping up with the demand for clean water from this rapidly growing population proved a complex challenge.
Sulzer
05/08/2019
Water resources are placed under increasing strain as populations expand and industry grows within an area. Municipalities and local government are tasked with planning for the future and making sure that the local population has a safe and reliable source of water. For one city in Texas, the planning for a new water treatment plant had been ongoing for years, to the point that the population had increased by 20 percent while plans were made and the finances secured. After deciding to use a new source of water, the question was raised about the best way to move the water over 390 feet vertically from the lake to the new treatment plant.
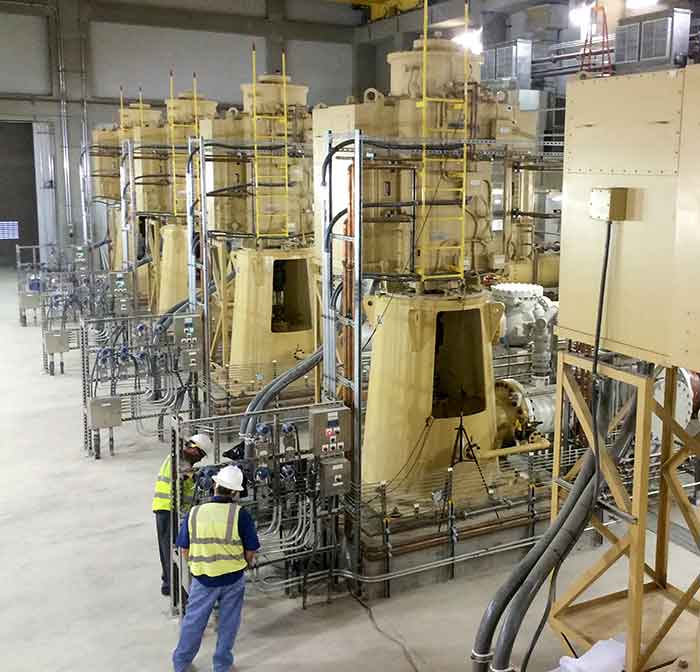