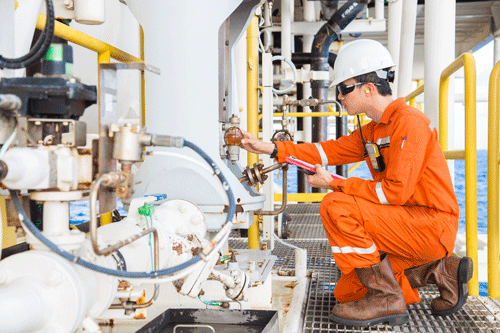
The commissioning and starting up of pumps are special types of work that require specific skills. There are always contractors who are interested in commissioning and startup tasks that will argue that, because they can procure and install pumps, they are able to commission, startup and operate these pumps. This is not correct. Commissioning, startup and operation skills are normally isolated to operators and specialized commissioning companies. Some vendor representatives may have a great deal of knowledge about commissioning and operation of pumps; however, other vendor representatives may not have such knowledge and experience.
Challenges at Startup
For a proper startup, sometimes modification is required for the pump and associated systems. Some well-known examples are:
- incorrectly configured instrumentation and control systems
- piping that must be reconfigured
The lack of spare parts is a well-known problem during startup, which can cause considerable delays. The uniform bolt tensioning and torquing procedure can be an issue for some pump packages. Some flange connections in pumps, particularly piping-pump bolting connections, may require checking and retensioning of bolts. Isolation valves and devices are sometimes not removed for commissioning/startup which can cause serious damage.
Prototype pumps are usually discouraged; however, they are sometimes required when using a new model of pump for the first time. The commissioning schedule for prototype systems should be carefully planned with suitable allowances and margins added. As the main power generator or the main power transmission systems are usually on the critical path of a project, temporary power generation facilities can be a great advantage and offer great flexibility in commissioning/startup.
A realistic and thorough performance test of a pump at a manufacturer’s shop can greatly facilitate the startup. This could save weeks during commissioning and startup. Additionally, the cost of expert hours for on-site repair is more than three-times the cost it would be at a manufacturer’s facility.
Challenges & Difficulties With Lubrication
Pumps of various models, types and sizes are used in any given plant or facility. Some pumps may be grease lubricated, but large, critical pumps usually need a dedicated lubrication-oil system.
Lubrication problems and lubrication-related bearing issues have been frequently reported during commissioning and startup. Regarding lubrication, the following key factors should be rechecked and verified:
- the properties of grease/lubrication-oil (for example, viscosity)
- the quality of grease/lubrication-oil
- the details of the lubrication-oil/grease system
- the operating conditions (pressure, temperature, flow, etc.) of the lubrication-oil system
- cleanliness of the lubrication system
Insufficient lubrication could cause bearing damages. This can progress rapidly, resulting in a failure.
Additionally, insufficient lubrication could lead to discoloration and significant reduction in mechanical strength. Inadequate lubrication and associated heating effects could show themselves in many different forms, such as shiny areas, glassy surfaces and others. These might be detected in a thorough inspection of bearings. It is necessary to ensure any pump receives proper lubrication during startup.
Other Difficulties
There has always been a great deal of attention given to large and critical pumps. Consequently, small and medium-sized pumps have often been looked over. Ball bearings and roller bearings have been used in small and medium pumps, which usually do not reach their life expectancies due to poor installation, improper commissioning, careless startup or poor operation.
Major reasons for early failures of rolling-element bearings have been mechanical damage (for example, due to misalignment), lubrication problems and material defects. Some rolling-element bearings have even failed during startup. High quality bearings, such as ceramic rolling-element bearings, can offer good reliability and long life. One example would be modern ball bearings with special stainless-steel races and silicon nitride ceramic balls. However, only a small percentage of modern pumps are equipped with these advanced bearings.
Installation tolerances of bearings (also looseness or tightness) are usually determined by the pump load and speed. Installation has a great effect on the performance, operation and reliability of pumps. When the bearing is fitted into the pump, forces will be applied to the bearing which can preload the delicate structure of the bearing.
If a bearing fit (of bearing/shaft) is too tight, the bearing can be internally preload. This can generate high loads on rolling-elements, and distorted housing bores can radially pinch the outer ring of the bearing. Some rolling-element bearings can tolerate only limited amounts of misalignment. This is a critical consideration in a proper commissioning/startup.
Shaft seats and housing bores may not be properly sized and may also be tapered or deformed. These defects could lead to a premature bearing failure. For example, the bearing ring could defect under loads and cracks could appear along bearing raceways.
Foreign matters and debris can lead to high rates of wear. Debris and dirt could be introduced to the system by insufficient sealing of bearings, unclean lubrication, improper flushing at precommissioning, etc. The expected life of a bearing can be considerably reduced by these debris and foreign materials. The impact damage during delivery, installation or startup can result in some small defects that can develop into large defects in a short time.