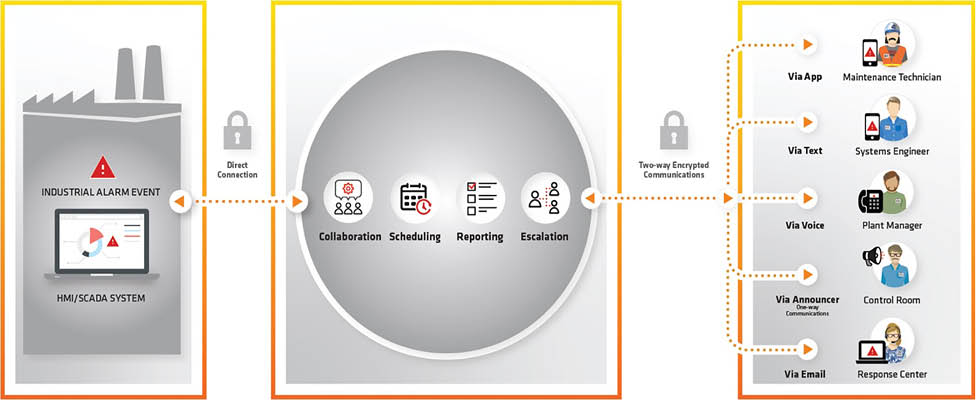
Supervisory control and data acquisition (SCADA) systems are essential for efficient pumping in every industry—water and wastewater, manufacturing, oil and gas, and even agriculture. Like other industrial technology, SCADA systems have undergone several notable changes in recent years driven by the emergence of the industrial Internet of Things (IIoT), the rise of cloud computing, the convergence of information technology (IT) and operational technology (OT) and the shift from desktops to tablets and smartphones.
These forces, along with evolving industrial requirements, are reshaping the capabilities of SCADA and expanding its potential, as evidenced by the increase in market growth expectations from $9.6 billion in 2022 to $16.9 billion by 2030.
SCADA forms the core of modern industrial control systems by unifying communication, data aggregation, information visualization and regulatory control responses. Many SCADA users may think only of the human machine interface (HMI) screen, but HMI is just a component of SCADA. HMI is a highly visible and critical component that has likewise evolved with changing technology.
However, the transformation of SCADA is better understood through the lens of growing plant data. For advanced operations autonomously capturing production data, the days of the clipboard and manual data analysis are gone. With the amount of data being produced in modern industrial facilities, the opportunity for optimization has never been greater.
Integration With IIoT
SCADA systems have increasingly integrated with IIoT devices, which have become more prevalent on plant floors. This integration leverages these technologies’ benefits, creating an environment optimized for both process automation and data analytics, leading to improved decision-making and increased operational efficiency. It also allows for more extensive data collection and remote monitoring capabilities.
The efficient use of large quantities of data to improve pump efficiency is challenging. Newer pump systems designed around IIoT are collecting more data more frequently from more sensors. It is no longer just the pump system flow rate; sensors are collecting data about the pump’s bearings, the mechanical seal system, vibration data from the pump’s foundation and piping structure, as well as a pump’s driver, for example. In many cases they are also synthesizing those measurements into reliability and performance metrics. Such devices are not only generating more data but also providing that data over much-improved protocols, with greater connectivity. SCADA systems have evolved to consume that data, and their footprint across the OT and IT networks has shifted with that change in connectivity.
IIoT devices and other modern field devices and programmable logic controllers (PLCs) are not just generating more data for the sake of consuming more network bandwidth. This information is critical to asset owners because understanding this data allows those servicing the pump to pinpoint the occurrence and duration of conditions like heavy vibration to determine the underlying cause and prevent asset loss and lost production.
More Highly Distributed Architecture
SCADA is increasingly implemented as a network of nodes with site-wide management functions. Cell level nodes are responsible for the alarm conditions and HMI screens relevant to that node while higher level servers allow the configuration and deployment of such nodes. Instead of a single SCADA server with multiple HMI view clients, modern SCADA implementations are increasingly distributed systems deployed across multiple servers. Such SCADA nodes may be deployed across a wide area network (WAN), allowing, for example, individual well sites to process their own data and determine their own alarm conditions while allowing a view client to view process data and alarms from multiple sites. This shift in SCADA deployment was made possible by changes to the communication stacks hosted by SCADA systems. The trend has been a shift away from proprietary methods of data exchange and remote procedure calls to more open protocols based on Internet Protocol (IP).
A large percentage of pumping systems across all industries are operating below their intended efficiency point. Many end users still operate their pumping systems on relay logic panels without any remote visibility, and some operators travel station-to-station daily to manually jot down operating hours on paper spreadsheets. However, utilizing advanced technology and interconnectedness of SCADA, HMIs, remote monitoring and real-time and historian reports, efficiencies and operations can dramatically improve, and critical failures can be prevented.
Integration With Cloud Computing
Operations solutions downstream of SCADA like historians and MES have increasingly integrated with cloud computing platforms. This integration allows for more extensive data analysis, elastic resource utilization and reduced IT costs. Building upon IIoT devices, cloud-based SCADA solutions are also offered. With such cloud-based SCADA, pumps can be monitored and controlled just like with on-premises SCADA with HMI functionality offered typically through a web browser.
More commonly, modern SCADA deployments are increasingly cloud connected while control functions remain on the OT network. Bidirectional proxies are used to bridge communications, allowing data transfer reliably and securely with cloud-based services. Hybrid solutions also exist within the SCADA space. For example, on-premises SCADA servers with cloud-based HMI designer components allow systems integrators to develop HMI off-site and quickly deploy on-premises
for runtime.
Cybersecurity Enhancements
With the rise in cyber threats targeting industrial systems, SCADA security has become a paramount concern. Recent years have seen improvements in SCADA cybersecurity measures, including encryption, authentication protocols, intrusion detection systems and regular security updates to mitigate vulnerabilities.
From companies to federal governments, every business or organization that works with SCADA systems is vulnerable to
SCADA security threats. A cyberattack can access the controller and change the pumps’ pressure, manipulate variable frequency drives or entirely cut down the water supply, depending on where the controller is applied.
Greater Focus on HMI Design
HMIs are used by operators to determine if a particular pump in the facility is currently running, for example. Operations have come a long way from manually activated switches, dials and other controls to start and stop cycles, adjust set points and perform other functions required to fine-tune and interact with a control process. HMI technology eliminates the need for this outdated practice and thereby reduces many costly problems caused by lack of information, faulty indicators or human error.
User interfaces for SCADA systems have evolved to provide more intuitive and user-friendly experiences for machine operators, but the improvements are not limited to that role. Modern HMIs that work alongside a SCADA system have increasingly provided higher level overviews of operations for plant-wide and regional supervisory roles. Such HMIs offer customizable dashboards, advanced visualization tools and support for mobile devices, empowering the entire operations team to monitor and control processes more effectively.
Engineers and forward-thinking operations are exploring ways to implement augmented reality and virtual reality to visualize manufacturing functions.
Remote Alarm Notification Software
Like advanced HMI, SCADA implementations are increasingly incorporating alarm notification, making such alarm notification solutions another means by which users interact with the SCADA system. Alarm conditions can be relayed and acknowledged through such notification via email, SMS, voice calls and mobile apps. Remote monitoring and alarm management enables operators to take on more proactive, hands-on tasks in the field or on the plant floor without hiring additional staff.
Increased connectivity allows for greater process transparency and the added potential for predictive analytics and sentinel alarm conditions. Smart operations facilitate addressing potential issues before they become problems, but only by extending that connectivity to the final hop—to the people who operate and optimize equipment, like pumps. Connecting devices to people and getting the right information—with increased sophistication of modeling—to the right people at the right time is the strength of remote alarm notification software. Such software builds upon the basic email notification built into SCADA systems with advanced escalation logic, scheduling and improved user interaction.
Reporting
Reporting software enables organizations to turn raw process data into actionable information, increasing efficiency and reducing costs. Reports provide a visualization of the history of process information and correlate related process variables, compute metrics on that data and visually graph it for easier pattern and anomaly detection. These reports are created through third-party software that seamlessly integrates with PLCs, SCADA and historian systems. As the data is collected it is summarized as key metrics—flow totals or turbidity threshold analysis.
Such reporting systems also provide the compliance reports required by states, as well as operating and performance reports used by plant personnel. Furthermore, automated reporting solutions streamline regulatory compliance by collecting data from various sources like SCADA, laboratory information management systems (LIMS), manual entry and others. The final output is published into a formatted document accepted by regulatory agencies. Advanced reporting solutions can also pull information from remote alarm notification software, allowing further analysis and optimization of condition response times. This reporting software is scalable so facilities that vary in sizes, data sources and people skills all have a solution.
The Future
SCADA systems have improved the way industries operate by providing a comprehensive solution for monitoring and controlling various industrial processes. With the advancement of technology, the future of SCADA systems holds tremendous potential for transforming industrial operations. Leveraging these advancements enables industries to move from reactive to predictive and preventative, optimizing processes and reducing unplanned downtime.