10/01/2015
During the last 20 years, the common understanding that new industrial pumps require some basic checks and adjustments prior to installation and startup has been supplanted by a new notion that pumps arrive from the factory ready to go, a phenomenon known as "plug-and-play."
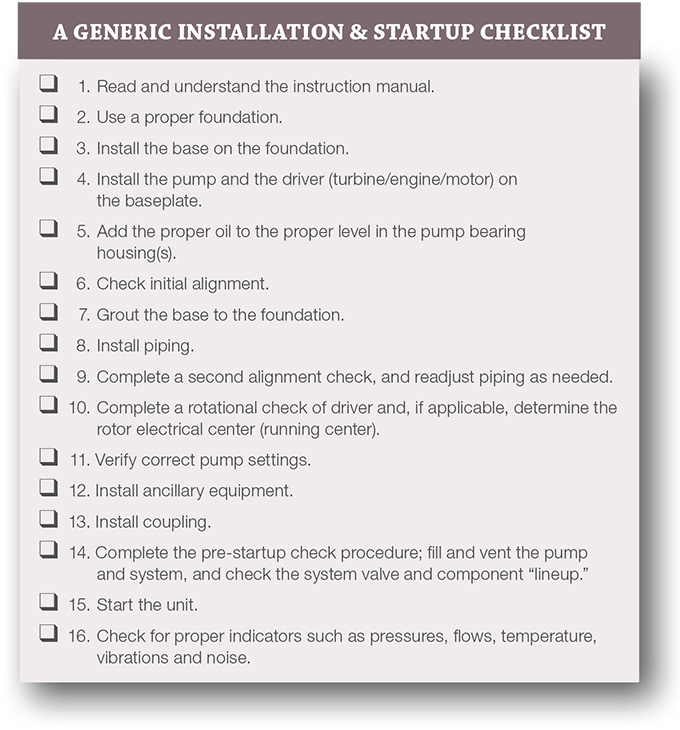
Foundation
Foundations have become a frequent omission on new installations. Unfortunately, ignoring this step can lead to chronic misalignment issues from the driver to the pump and other potential problems. If you want to have a best-in-class operation that increases mean time between failures and repairs (MTBF/R) to more than five years, I highly recommend that you provide a proper foundation. Industry rules of thumb for centrifugal pumps suggest that the foundation size should be three to five times the mass of the pump and driver combined.Base Installation
Install the base on the foundation, and take steps to ensure that the base is flat and level. "Flat" is a condition (state) accomplished by the manufacturer and is difficult to properly measure in the field; however, you can ensure the foundation is flat by using a precision ground flat bar and feeler gauges. Using a level to check flatness is actually an incorrect method. The flatness specification will vary by manufacturer, application and base types. "Level" is a condition that is adjusted and set in the field. It typically means less than 0.002 to 0.005 inches per foot in two directions. It is recommended to set the axial level first. If the unit is not level, the subsequent alignment processes will be laborious and likely incorrect. Many pumps require a specified state of level for the lubrication system to function correctly. Level is also a good practice from a rotor dynamics aspect.Pump & Driver Installation
Install the pump and the driver (turbine/engine/motor) on the baseplate. Best practice usually calls for the pump to be placed directly on the base. Unless specified by the OEM design, it should not be shimmed.Lubrication
Add the proper oil to the correct level in the pump bearing housing(s). (See my two-part article on this subject in the April and June 2015 issues of Pumps & Systems.Initial Alignment Check
This step is often overlooked and can have negative consequences later if not conducted at this point. Once the base is grouted and/or the piping is installed, it may be too late to accomplish some simple machinery placement moves to achieve precision alignment.Grouting the Base
Grouting is another step frequently omitted or performed incorrectly. If the grout is not added or if it does not make full contact with the base and foundation, the forces from pipe strain and machine vibrations cannot be successfully transmitted to the foundation. The top surface of the foundation and the underside of the baseplate must be properly prepared for the required grout/epoxy adhesion and bonding. Recheck the unit alignment after the grout process.Piping Installation
Up to this point in the process, the piping installation should not be completed within 10 feet of the pump. The universal best practice and accepted method is to pipe away from the pump and not to the pump. This strategy will prevent any pipe strain on the pump. Someone once said, "A pump is the most expensive pipe support you can buy."Second Alignment Check
Now that the base is grouted and the piping is completed, the alignment is likely moved off the specification. Recheck the alignment and correct as necessary. This is also a good time to conduct a quick and easy check for the presence of excessive pipe strain. Place your dial indicators or laser units on the pump drive hub in two planes (vertical and horizontal). Then completely loosen the discharge flange bolts. If the pump hub/coupling moves more than 0.002 inches in any direction, the strain is too high. Repeat the process for the suction pipe. Correct the excessive strain before proceeding to the next step.Rotation Direction
Conduct a rotational check of the driver and, if applicable, determine the rotor electrical center (running center). Failure to check the direction of rotation can have serious and expensive consequences. I see this mistake frequently despite instructions to the contrary. Rotors on larger motors with sleeve-type bearings will have both an electrical center and a mechanical center. You will need to determine both and record the results. If your unit has bearings of this type, then this step may be better conducted prior to the second alignment adjustment. Your supplier can provide more details. Set the alignment for the electrical run center distance not the mechanical one. Caution: Don't be surprised when a cloud of jobsite dust emits from the motor on startup.Settings
Check the pump settings, including impeller axial adjustments, clearances, mechanical seal settings, rotor centralization, balance drum settings and bearing lift. Verify the unit rotates freely.Ancillary Equipment
Install ancillary equipment, including seal flush systems, cooling/heating equipment and monitoring devices.Coupling Installation
Follow the manufacturer's guidelines, and pay special attention to the key-to-keyway fits. Note that the pump and driver hubs should be installed sooner than this step.Pre-Startup Check & Startup Procedure
Fill and vent the pump and system. Check the system valve "lineup." Review and verify the preceding steps were accomplished. Remember, you cannot vent a running pump; the fluid will come out, but the air trapped in the center of the machine will remain. The fluid has more mass and will be flung to the outside. Start the unit. Be prepared to stop the unit immediately if anything does not seem right. Check for proper pressures, flows, temperature of oil and bearings, vibrations, and noise. It is good practice to recheck the alignment after the pump has been operating for a short time. If the pumped fluid is very hot (above 200 F), it is also good practice to perform a "hot alignment check."Conclusion
All too often I witness the damaging effects from dismissing or disregarding the information in the IOM and this article. If the intended outcome is to accomplish successful operation for a minimum of five years, measured as zero downtime for repairs or failures, this advice will assist you in that endeavor. When units arrive with the pump and motor already on the baseplate, beware that improper rigging and handling will distort the base. Be sure to record all of the initial measurements and alignment settings to establish a baseline of unit data. Finally, I advise users to check the alignment of the pump to driver four to five times during the process from receiving to startup. References- Heinz Bloch and Allan Budris, "Pump Users Handbook Life Extension."
- Wallace Wilcox, Mike White and Gordon Parks, "Commissioning and Start-Ups of New Units (Pumps)," Proceedings of the 25th International Pump Users Symposium 2009, pages 75 to 83.
- Todd Monroe and Perry Monroe, "Road to Reliable Pumps," Proceedings of the 23rd International Pump Users Symposium 2007, pages 99 to 112.