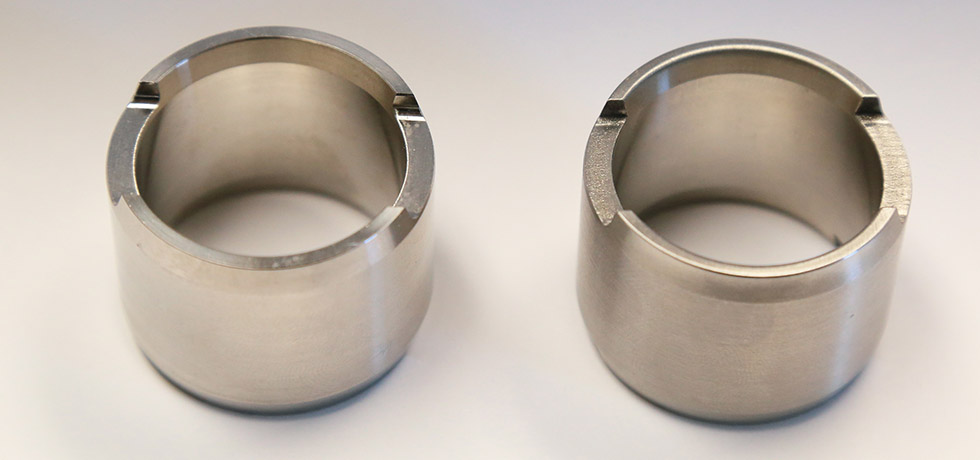
How closely is a part inspected before purchase? Some parts may seem attractive due to a low price, but only looking at the initial cost may leave a user vulnerable to unforeseen costs later.
There are reasons that alternative, “might fit” parts cost less, including the possible use of lower quality materials or by omitting important manufacturing steps, such as polishing or grinding. The part may not last as long, making its return on investment poor.
For some applications, this might not matter if the user does not mind making frequent replacements. But for food or pharmaceutical applications, polishing or grinding are critical to sanitary performance and cleanability. A lower quality finish on a part, therefore, could increase the risk of bacterial growth and contamination of final product—an intolerable result for sanitary pumping.
Well-designed parts are the result of years of research and development. The parts are designed to ensure continued performance and reliability of the machine and are made to the exact same, or higher standards, as the original system. If a piece of equipment is certified to 3-A or European Hygienic Engineering and Design Group (EHEDG) standards, the user should choose a part that will maintain the desired standard for the processing system.
In the United States, the Food & Drug Administration (FDA) Food Safety Modernization ACT (FSMA) was signed into law in 2011, changing the focus from responding to contamination to preventing it. Both the 3-A and EHEDG standards aim to enhance food safety by promoting hygiene in the production and processing of food. Covering the U.S. and Europe, the standards are accepted practices to address public concerns, prevent contamination of food and keep food supplies safe. Developed by a range of industry experts, the standards cover the material specifications, design criteria and fabrication quality of equipment such as pumps, valves and heat exchangers that have any surface contact with the product being treated. The standards are understandably stringent.
The 3-A certification standardsstate: “For processors, conforming to 3-A Sanitary Standards means they are in compliance with applicable sanitary codes for equipment construction. Processors also can be assured that with equipment meeting 3-A Sanitary Standards, they can apply the most modern cleaning and sanitizing methods, materials and systems to in-plant operations.” This remains true if the parts used are certified by the 3-A Sanitary Standards, Inc. Replacement Parts and System Component Qualification Certificate (RPSCQC) program and if these parts are used throughout the equipment’s lifetime. EHEDG guidelines state: “Assurance of quality and safety is an essential need for the continued good reputation of foodstuffs. The correct hygienic design and maintenance of food production systems is considered as a prerequisite to fulfill these requirements.”
The following examples show some of the pitfalls of not using parts that are designed to these strict standards in sanitary applications. These examples are hypothetical but are based on real-life experiences:
Selecting a lower cost blade alternative part for use in a hygienic processing system may mean the part has not been correctly heat treated. If this is the case, it could put the process at risk because the softer blades could shed metal shavings in the product.
Selecting plastic scraper blades in a scraped surface heat exchanger (SSHE) chilling tube, instead of hardened metal blades, can work well in certain applications, but care should be taken to ensure they are suitable for the specific process. In applications where the SSHE is used to freeze products, for example, low tube temperatures could lead to plastic scraper blades breaking and chipping and entering the foodstuff. In such cases, the changes to machine specification may mean hygienic certification. This leaves producers exposed to the risk of having to dispose complete batches of product, as well as having to replace the blades.
These examples show that, with product safety a top priority in food processing and pharmaceutical industries, the potential risk to brand and business could be enormous.
While some spare parts may have a higher price tag, the total cost of ownership could be less than other options.
For sanitary applications, the integrity of the final product is a concern. When selecting the right technology for a process, quality, performance and compliance are all critical considerations to ensure profitable, safe production.