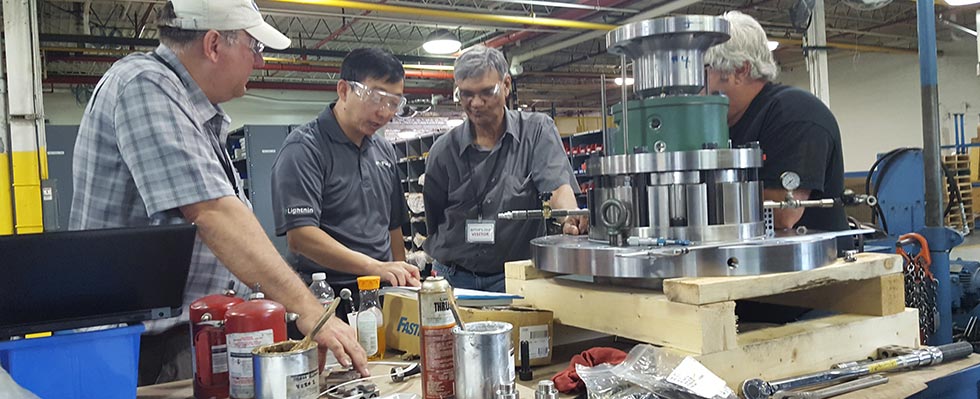
The digital transformation for chemical process industries seems like a difficult endeavor, but with digital twins, tracking assets in the physical world through a digital model is possible and optimal.
Digital twins are created to represent assets in the physical world through a digital model. However, it is not just a data model. There must be some form of relational interaction. In other words, the data that creates the digital twin must always faithfully match the real-world environment. It should look and feel like the real environment. If not, then model simulations cannot provide helpful results. With a faithful digital twin and six essential criteria, users can implement a system that drives improvement across the operations life cycle and the entire organization.
Practical Investment
No matter how large or small the chemical processing plant, a digital twin can be a practical investment. When used correctly, the digital twin simulation can be a flexible and scalable tool not only for the life cycle of projects, but also the entire plant.
For a user to ensure that they are making the best possible investment into digital twin architecture, correct and timely data is crucial. The digital model must reflect the physical world of the plant or operational improvements and control of the plant will never occur. Without proper diligence, a user’s investment will more likely result in loss.
Improved Process & Controls
With a holistic approach to digital twins, a chemical processing plant can improve engineering from the first stages of each project. Advanced simulation technology leverages the existing project with process models that can help to improve speed, reduce waste and even change the process entirely if more efficient models are found to be helpful.
The more accurate the digital twin, the more streamlined each project will be. Users will not need to attempt changes to any project before ensuring they will be successful with digital twin modeling.
Lower Costs With Shorter Processes & Less Waste
There are two ways to build a digital twin model: rigid and flexible, each with their own benefits. However, a rigid approach could result in missing opportunities for improvement, as it would not include results that could be obtained with a larger investment into more equipment and manpower. With some flexibility in the modeling, users could receive suggestions that prompt plant improvement through new purchases and hiring that could save more money over time.
Test Process Updates & Changes
With a more flexible approach, users not only gain insight into the equipment and manpower that could improve efficiency, they also gain the ability to change and update processes for increased control and more predictable results. Instead of doing the same thing repeatedly, users can model new strategies and processes to discover likely outcomes before making changes in their real environment. The modeling allows users to see where potential waste, safety hazards and failures may occur.
Training
In the past, training for new processes in a chemical processing plant took place in real time, with real chemicals. The potential outcomes of each project and process provided real-world training that could take six or seven years to master. With a digital twin approach, tests and experiments can run at any time, allowing plant operators to experience various outcomes on a regular basis, lowering the time it takes to learn how to make good decisions on the plant floor.
Training can now occur for plant transitions, transient operations, startups and abnormal situations—all
in the digital world, with no risk to the real environment. The result is faster training, with employees that enter
real-world scenarios with more experience and confidence.
Usability
The interactions between control data, historical data and design data should all be integrated in an elegant way so that the structure of a digital twin can evolve and change with a user’s specific needs. Whether using flexible or high-fidelity simulations, the need is the same: a simple design that can be easily understood by anyone who uses it. The more it resembles the system used on the plant floor—as in, the more closely it mimics real life experiences—the better off plant managers will be.
A high-tech tool, such as a digital twin, does not have to be impossible to use. In fact, the more usable the program, the better results will be.
When exploring a digital twin architecture for a chemical processing plant, usability should be a top priority.