For the last few centuries, pumping systems and the pump industry have been relatively uncomplicated. Beginning in the 1950s, however, pump manufacturers arose from machining shops, and a stream of acquisitions across the globe created a new and rigorous demand for pumps. Newly engineered pumps designed for an ever-increasing landscape of applications, material variations, sizes and customized solutions created a competitive market focused on creating the most energy efficient pump. Today, the Internet has transformed the realm of energy efficiency, offering remote access and sensing devices—including alarms and video capabilities that visually display and analyze rooms, pump status and other real-time data—to provide critical information at the swipe of a finger. Internet-enabled apps accessed from smartphones, tablets or other handheld devices allow even the pump industry to control diverse devices more efficiently than ever. These apps, if streamlined, could create new value by closing the loop of the entire pump life cycle from research and development (R&D), to application design, to startup and commissioning, to upgrade and retrofit processes. These Internet-enabled apps and devices integrated into value-added services is known as the Internet of Things (IoT). The use of consumer technology is driving the growth of the IoT sphere. In fact, some predictions estimate that by 2020, 26 billion installed IoT units will exist, and IoT suppliers will generate $263 billion in incremental revenues, resulting in a $1.9 trillion global economic value.
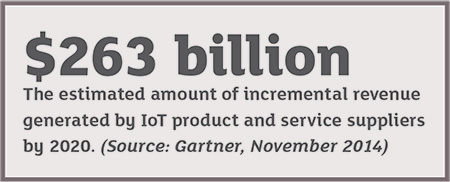
The Internet of Pumps
More than a decade ago, pump engineers and operators experimented with wireless application protocol (WAP)-enabled phones to communicate with pumps. Around that time, the industry used machine-to-machine (M2M) technology based on general packet radio service modems to package equipment data and send it to supervisory control and data acquisition (SCADA) systems and Web-based extranet interfaces to monitor and control pump systems. Today, high-tech tools including variable speed drives (VSDs), SCADA systems, condition monitoring equipment and other automation devices, are widely accepted by the pump industry. However, these systems can be costly, complex, difficult to install and focused only on the individual asset. To solve the challenges of modern pumping technology, many companies and niche industries—utilities, mining and manufacturing in particular—are implementing IoT solutions to reduce operational expenditure, increase their return on investment and improve customer satisfaction. Several levels of IoT sophistication exist within the pump industry. The higher the level, the more plants and facilities are able to tap into this unprecedented opportunity to transform their commodity-driven business into a value-adding, service-based organization (see Figure 1).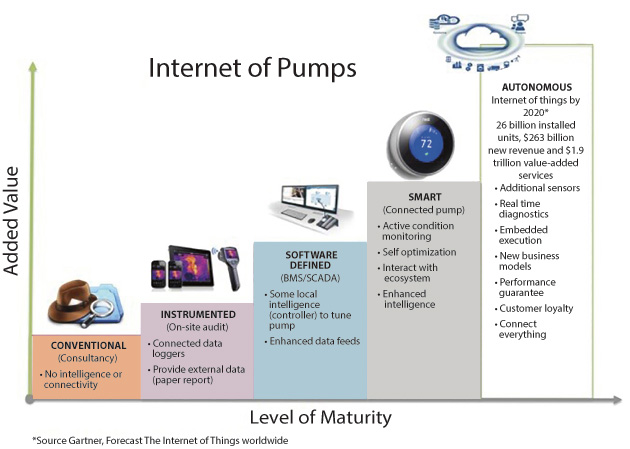
Conventional
The first level of sophistication (see Figure 1), the conventional method of selecting or reviewing pump performance, starts at the basics. Using some basic application data, a consultant or engineer takes the information from the nameplate and chooses equipment using a pump selection program. With that information, he or she can benchmark the existing pump efficiency against that of a newly designed pump and calculated running times. The consultant or engineer can then provide educated estimates about the energy consumption and potential cost savings of installing a new pump.Instrumented
In the instrumented level, actual data loggers could be installed on-site to measure and log critical pump data—including energy consumption, flow, and inlet and outlet pressure—over a period of time. Plotting that data using Excel into the original design curve would give a more accurate view of pump performance over the period the data is logged. The same benchmark used in the conventional approach could be used to estimate potential savings.Software Defined
If the pump is equipped with a controller, the pump will operate against defined set points making use of the best possible predefined working conditions. These automated systems could generate some data reports with historical trend lines and even generate set alarms when data thresholds are reached. However, this level of IoT sophistication does not provide any further information about the performance of the pump system. The system only notifies the user when it works outside the programmed conditions. These building management systems (BMS), SCADA or M2M applications have evolved in a context in which applications such as remote monitoring and support for equipment have been tied closely to equipment services contracts. To date, remote services and M2M systems have largely been focused on simple remote diagnostics and simple tracking services, in large part because of technical complexities and business model challenges. Existing technology has proven cumbersome and costly to apply with many conflicting protocols and incomplete component-based solutions. The challenges and costs of developing applications and integrating diverse devices onto networks in an interoperable manner have been significant adoption hurdles. For this reason, many organizations settle at this level.Smart & Autonomous
Moving to smart and autonomous applications (the last levels) involves multiple collaborating systems with significant interactions between assets such as pumps, heat exchangers, control systems and people. The focus is no longer solely on the product supplier's ability to efficiently deliver support for its product. Instead, value is brought to the customer through business process automation and optimization. Consider any of the larger pump systems in more complex industries such as power generation or industrial manufacturing. In such high-value and critical businesses, major electric utility customers have good reason to hate equipment failures. At the least, any downtime creates huge opportunity costs for these customers. It often means they have to pay hefty regulatory compliance fines. To reduce risk, monitoring and diagnostics of critical assets such as large pump systems enable suppliers to send a technician or engineer before a failure occurs (preemptively) as opposed to doing so according to a schedule based upon assumptions (proactively) or, even worse, after the power has gone off (reactively). Most pumps suppliers cannot charge more than $75 to $120 per hour for their technical support because of price and benefit pressures from local competitors. With efficient network-enabled services, however, leading players could charge $250 to $350 per hour for the same technician who has become a skilled subject matter expert.The Future of IoT
These instances, however, are still examples of simple applications largely focused on the product manufacturer's own value chain. They are simple "hub and spoke" remote support. While these models have value, significant untapped opportunities are available to provide new value for users and customers.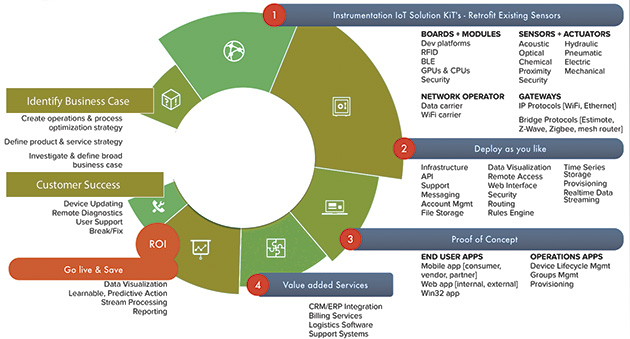
4 Essential Steps to Successful IoT Implementation
-
Define your focus.
When you Google "IoT," you will get more than 25 million results. "IoT technology" will garner about 15 million hits. These search results alone reveal the hype about the newest available technologies and services. The best approach to building an IoT strategy is to begin by spending time and resources to clearly define your customer problem, determine an IoT-based solution and develop a business case for the value-added services these technologies would provide.
-
Choose a platform that fits your needs.
Because most plant management teams are not software developers, consider selecting an IoT platform that provides standard widgets and templates that allow users to drag and drop and copy and paste pre-coded materials that will reduce your time to market by 10 times. Several of these platforms are already available on the market.
-
Keep development simple.
Engineers are used to developing, breaking down and rebuilding again. The development of wireless sensors, however, is different. Selecting the wrong standard is the No. 1 pitfall that wastes time and resources. To avoid these challenges, develop sensors and apps using a basic IoT solution development kit.
-
Build a strong IoT ecosystem.
Entering this new IoT space requires time and teamwork. Building an "Internet of Pumps" solution is impossible without key partners that have strong ecosystems of solutions to serve your plant's particular needs—especially as your IoT network grows.