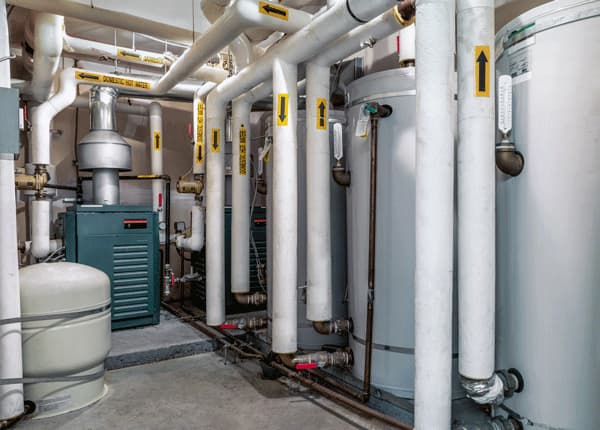
Mechanical seals are critical components typically employed in pumping systems to prevent leakage from the pump casing at the point of shaft entry. Due to the nature of the dynamic interface, it is fair to say that the mechanical seal has the toughest challenge in the pumping system. Subject to the process fluid, temperature and changing pressures, along with rotational speed, mechanical seals are often pointed out as a cause of significant downtime. The actual cause of the downtime is an external factor that creates an operational anomaly that, in turn, causes the seal to exhibit leakage. Fluid film breakdown is the cause of most, if not all, seal failures.
For many years, environmental controls—also known as piping plans—have been employed to provide a lifeline to the mechanical seal. The most common piping plan employed is referred to as Plan 32 and illustrates an external water supply connected directly to the mechanical seal to provide a cool and clean operating environment (Image 1). This then promotes the formation of a clean, stable fluid film.
IMAGE 1: Piping Plan 32 can be costly to operate in high pressure hot water systems.
(Images courtesy of FSA)
Operators must accept that large volumes of water will enter the process stream when using Plan 32 and that the water will not only dilute the process but also affect it thermally as the water used is often unconditioned and enters at ambient temperature. In many applications, the volume of the water can be more troublesome than the temperature; cool, clean operating environments can increase a mechanical seal’s reliability such that the benefit of downtime avoidance outweighs the cost of process dilution and, in some applications, subsequent water extraction.
Hydropad Mechanical Seal Face Technology
Hydropads are mechanical seal face features that work to modify the fluid film directly. A feature of either the rotary or stationary face, hydropads lower face operating temperatures to prevent the effects of flashing. Sometimes the features are placed on the outside diameter of the seal face to provide the benefit of sweeping and self-cleaning themselves of small scale debris often found in boiler and high-pressure hot water systems (Image 2).
IMAGE 2: Hydropads are viewed as ‘scalloped cut outs’ around the outside diameter of the rotary
seal face.
Without hydropads, seal faces would vaporize the process fluid prematurely, causing the seal to operate without a stable fluid film and fail. Hydropads are proven to improve the efficiency and reliability of mechanical seals while eliminating the need for Plan 32 flush or other forms of external cooling such as Piping Plan 21 or cooled discharge recirculation. The resulting benefits and savings for users are often counted in tens of thousands of dollars per pump, per year of operation.
High Pressure Hot Water Applications
In the case of hot processes, the thermal losses resulting from the adoption of Plan 32 to increase mechanical seal life can be counted in tens of thousands of dollars.
By eliminating the need for external cooling, thermal savings along with savings in time spent maintaining the equipment are quickly realized. A secondary improvement is personnel safety, as operators and technicians are no longer required to inspect or adjust environmental controls that are working with or in the proximity of high temperature and high-pressure pumps.
The technology simplifies pump operation and maintenance. In fact, the user is often completely unaware of the fact that the installed seal is operating with a special geometry that requires no external cooling to operate reliably.