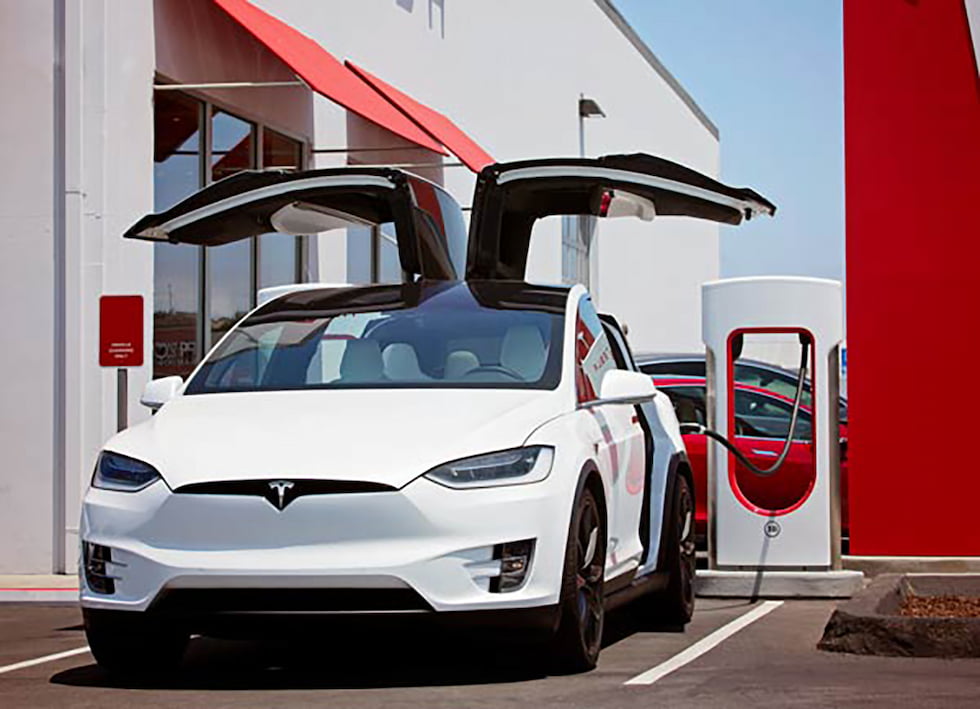
The basic chemistry for lithium batteries was discovered in the early 1900s, and the technology was commercialized in 1991 when Sony introduced the first rechargeable batteries for camcorders. Since then, the popularity of lithium-ion batteries has skyrocketed, via use in mobile phones, laptops and electric vehicles. Rechargeable lithium batteries produce twice the watt-hours (WH) per kilogram of nickel-cadmium (NiMH) batteries, and six times that of lead-acid batteries.
The fastest-growing applications for lithium-ion batteries come from auto manufacturers in the U.S., Europe and in particularly in China, which has more than 60 different brands of electric cars. As electric vehicle (EV) manufacturing increases, so too does the demand for pumps that move the chemicals, polymers and catalysts needed to make the batteries.
The key components in a lithium-ion battery include:
- The cathode, which stores lithium and releases ions when the battery is charging.
- The anode, which stores lithium and releases ions when the battery is discharging.
- A separator, which provides a barrier between the cathode and anode.
- The electrolyte, which is a liquid conduit that enables lithium ions to permeate the separator and move between the cathode and anode.
- Current-collectors (positive and negative), which receive electrons from the external circuits of the battery (during charging and discharging).
The current-collectors on the electrodes have specially designed surface coatings, which are made by pumping a slurry mixture of polyvinylidine fluoride (PVDF) and n-methyl pyrrolidone (NMP). These two polymers bind particles together in a manner that facilitates the electrochemical reactions needed to generate voltage and current.
NMP is extremely harsh in nature, but it plays a critical role in the process. Like a key fitting into a lock, NMP provides the bonds needed to blend and dissolve PVDF in a manner that is optimized for the process. Once the electrodes are coated, the NMP solvent vaporizes completely. The supply chain refers to NMP as an indirect material, because it is needed for the production process, but it is not contained in the final product.
The production of lithium and other hybrid batteries requires large amounts of NMP (which can be sourced from several different chemical manufacturers). In 2020, the global auto industry consumed 360,000 metric tons of NMP, with about 200,000 tons used in China.
The flammable nature of NMP requires that pumps, pump motors and all processing equipment must be explosion-proof. NMP is a highly toxic, Class-3 combustible liquid that exhibits flammable vapors. Even the slightest exposure will irritate eyes, skin, nose and throat. NMP affects the central nervous system and the brain, causing dizziness. Extended exposure can also cause kidney and liver damage. The U.S. Occupational Safety and Health Administration (OSHA) limits worker NMP exposure to 10 parts per million (ppm) in an eight-hour day.
For these reasons, sealless pumps are a preferred choice for handling NMP. Sealless pumps eliminate the seal and associated support systems, providing a reliable and leak-free solution for handling hazardous liquids.
While safety is always a primary consideration when it comes to selecting pumps for chemical processing applications, another factor is durability and the ability to withstand harsh and aggressive chemicals.
Years ago, when one of the world’s most popular electric vehicle manufacturers began ramping up operations, they sourced a variety of metallic American National Standards Institute (ANSI) sealed pumps for use on the battery cells. One after the other, they experienced consistent pump failures due to the NMP corroding the pump’s internals. A local pump distributor reached out to the chemical manufacturer that supplied the NMP to learn more about how they produced the chemical and to identify which pumps they were using during their production process. The NMP manufacturer used magnetic-drive pumps and had not experienced any pump failures. This information was shared with the auto manufacturer. A switch was made, and magnetic-drive pumps were installed in the auto manufacturer’s facility to handle NMP. Since that time, there have been no issues, no leaks and no pump failures.
For these types of pumping applications, durability is just as important as safety. Magnetic-drive pumps are specifically designed to handle corrosive or acidic applications. All of the pump’s wetted parts are molded ethylene tetrafluoroethylene (ETFE) components that can safely handle a wide range of corrosives and solvents (up to 250 F/121 C) without corrosion. A fully encapsulated magnetic drive sealless pump hermetically seals the inner magnets to isolate them from the process fluid and maintain magnet integrity for the life of the unit. Most importantly, a Kevlar-fiber reinforced vinyl ester shell protects the inside of the pump, and a secondary stainless steel layer is also provided for increased durability.
Given the scale of operations in this EV manufacturing facility, it was important to facilitate a fast and straightforward replacement process for installing the new pumps. The sealless pumps installed support all of the ASME/ANSI B73.3 and ISO 2858 standards. The pumps cover a wide range of sizes and standard external dimensions. This flexibility enabled the new pumps to be installed without requiring extensive changes to the piping or baseplates.
Maintenance is an important consideration for pumps handling toxic chemical applications. Sealless pumps have no seals and no seal support systems. They offer longer meantime between maintenance (MTBM) intervals, which reduces the effort required to maintain pumps. Sealless pumps are easy to install, and there is less U.S. Environmental Protection Agency (EPA) monitoring and associated documentation, which further saves time.
Routine maintenance is performed without the need for special tools or training. Pump designs with fewer parts are easier to repair. Sealless magnetic-drive pumps have just 9 wetted parts that can be quickly repaired in the field. A single-piece replaceable impeller is attached to the inner magnet drive via a tongue and groove system. This makes it easy to swap out the impeller as process conditions change, and it also simplifies warehouse parts management.
Energy efficiency is a theme that permeates every aspect of an electric vehicle manufacturer’s brand, so it is no surprise that EV manufacturers seek out energy efficient technology to make their products. Sealless magnetic-drive pumps boast energy efficiency, but some pumps reduce energy costs even further, with features like carbon-filled ETFE lined rear casings, which minimize heat generation through zero hysteresis losses during operation.
Today, more than 7 million electric vehicles travel the world’s roads each day. A third of these vehicles (more than 2.2 million) were produced last year alone, and every EV manufacturer is forecasting exponential growth for the years ahead. This means the world needs a lot more lithium ion battery cells, and all of that production requires thousands (to millions) of tons of chemicals like NMP, which must be carefully handled by pumps specifically designed for the task.
Whether its safety, durability, maintenance, or energy efficiency, there is enough evidence and a proven track record from the world’s leading electric vehicle manufacturers that sealless magnetic drive pumps can effectively handle the harsh chemicals that are needed to manufacture lithium ion batteries.