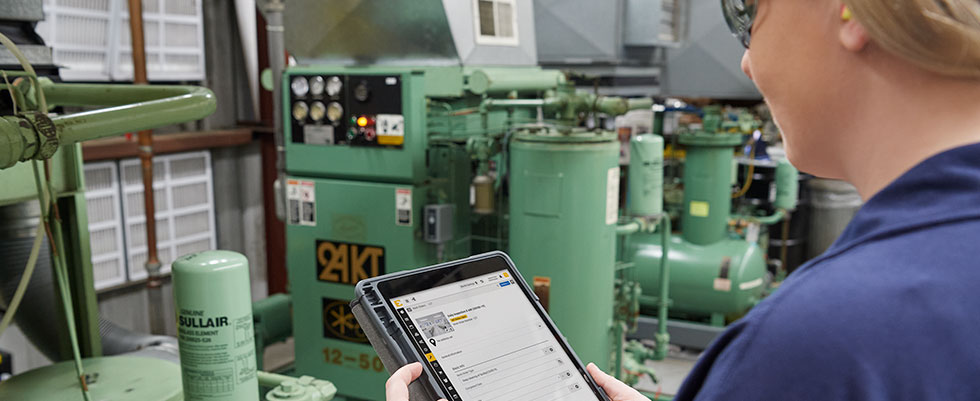
Using ultrasound and thermography to identify problems early can extend the lifespan of pipes and valves, prevent catastrophic leaks and increase productivity throughout a plant. Just as vibration monitoring catches developing faults in rotating machinery, ultrasound and thermographic tools can identify faults in a steam system so they can be resolved before they become a bigger problem.
While ultrasound and thermographic monitoring are not new, they are still not as widely used as other condition monitoring technologies. This article shows how today’s ultrasound and thermography tools work for condition monitoring and predictive maintenance, as well as the advantages they can offer for operations. It also explains how to introduce this technology into a plant.
Ultrasound and thermographic sensors spot early signs of cavitation, friction and turbulence. When used correctly, the sensors can identify faults before they cause issues like major leaks, stuck valves and blockages.
Modern sensors are precise enough to detect leaks as small as half a cup per minute. Detecting leaks while they are still small makes repairs faster, simpler and less expensive. Ultimately, by identifying problems early, ultrasound and thermographic tools act as a frontline defense against catastrophic failure.
Ultrasound technology has been around for decades, but modern tools have made the technology easier and more convenient to implement.
Technicians can use a structure-borne ultrasound sensor (also known as a contact sensor) to check for cavitation or turbulence at a specific valve. Typically, this is done by taking two measurements upstream and two downstream. The sensor listens for any abnormality in the flow of liquids or gas.
In hard-to-reach areas, technicians can use an airborne sensor as they walk around the work site. Airborne ultrasound detectors can sense leaks from a distance or at a location where it is not possible to apply a structure-borne detector. In many plants, it makes sense to use both airborne and structure-borne detectors to check for new and developing leaks.
Ultrasound and thermography give maintenance teams eyes and ears into their pump and valve systems. Ultrasound picks up high-frequency sounds that can indicate a turbulence swell caused by even a small amount of liquid or gas passing through a closed valve. These sounds would normally be drowned out by all the other noise on the plant floor, but ultrasound technology filters out extraneous sounds.
Similarly, thermography allows maintenance crews to see what they cannot otherwise see or feel. Thermal imaging visually identifies differences in temperature, which can indicate issues like valve leaks and blockages, in heating and cooling systems. Thermography tools create a heat map so technicians can visualize the potential problem areas.
Together, ultrasound and thermography allow maintenance teams to quickly identify turbulence, cavitation and friction, all of which are early indicators of abnormalities in the flow of gas or liquids.
Combining ultrasound and thermography creates a more powerful and effective solution compared to using one tool or the other alone. In the past, ultrasound testing required technicians to listen to the ultrasound and then graph it as a waveform. This method could be extremely accurate, but it required a high level of training and expertise.
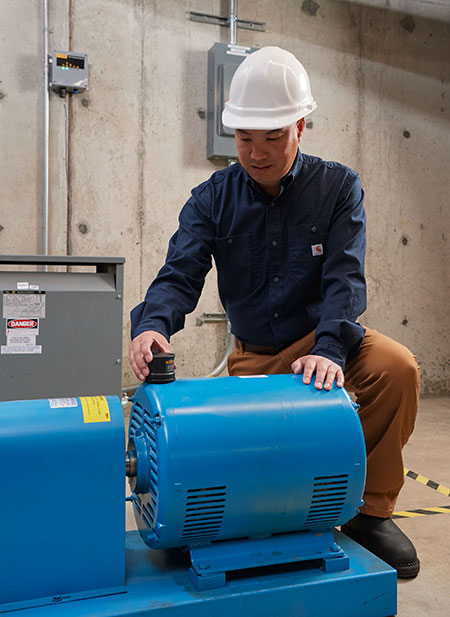
Today, modern ultrasound and thermography tools make it possible to build up a much deeper analysis, even without highly trained staff. Modern tools allow technicians to use more microphones to capture all the available sonic information.
This data can then be integrated with thermal imaging data to create a detailed, color-coded temperature map of piping from the inside out—all without requiring highly trained, specialized staff. Instead of studying a waveform, technicians can simply review the thermal map for indications of leaky valves or other related problems. This creates a couple of clear benefits:
A complete, accurate picture of pipes and valves. Combining ultrasound and thermographic sensing technology provides a more accurate picture of pipes and valves.
A cost-effective, easy-to-implement approach. Using the tools together allows plants to adopt the new technology, even without a deep bench of ultrasound technicians.
While the benefits of ultrasound and thermography are evident, some plants are still hesitant to implement the technology for various reasons. For example, limited resources, lack of skilled technicians and lean budgets are all potential hurdles that plant managers face when considering implementing new technologies.
In many cases, plants are also operating under intense pressure and a tight production schedule. It can be hard to find even a few hours to train employees in using the new tools. It can be even harder to find the time for route measurements.
Fortunately, applying this technology does not need to be an all-or-nothing approach. Instead of trying to introduce sweeping changes, start small. While sudden, large-scale changes are costly, time-consuming and difficult to secure approvals for. A small pilot program can yield fast, cost-effective results, while paving the way to effectively scale.
To start a pilot program, identify approximately 10 assets that have a spotty maintenance record. Train one employee in using ultrasound and thermography tools. Make sure this employee also has a sound understanding of the kinds of valves they will be working with so that they can easily see when conditions deviate from the norm.
Test out the technology on these 10 assets, keeping careful records before and during the pilot to track improvements. At the end of a few months, assess the pilot program. If it has been successful, add another 10 assets to the program. Keep scaling the program from there.
Many plants use ultrasound and thermography as troubleshooting tools when they suspect a leak. This a great application for this technology. However, these tools can also be used for proactive condition monitoring. Doing regular route measurements and checks can ultimately save thousands of dollars in repairs, if not more–not to mention the lost labor and production time from a breakdown.
Using ultrasound to monitor equipment for leaks makes it possible to catch the first signs of a cavitating valve before a pipe starts to erode, and long before there is a rupture and a major leak.
To test out condition monitoring during a pilot program, try performing a routine check every quarter or so. Experiment with doing this more or less frequently to get a sense of what kinds of issues come up and when. This also is a great place to use a computerized maintenance management system (CMMS) software to track maintenance work orders and identify patterns that emerge.
Ultimately, condition monitoring with ultrasound and thermography can prevent major leaks. This results in more uptime, greater productivity and lower maintenance costs.