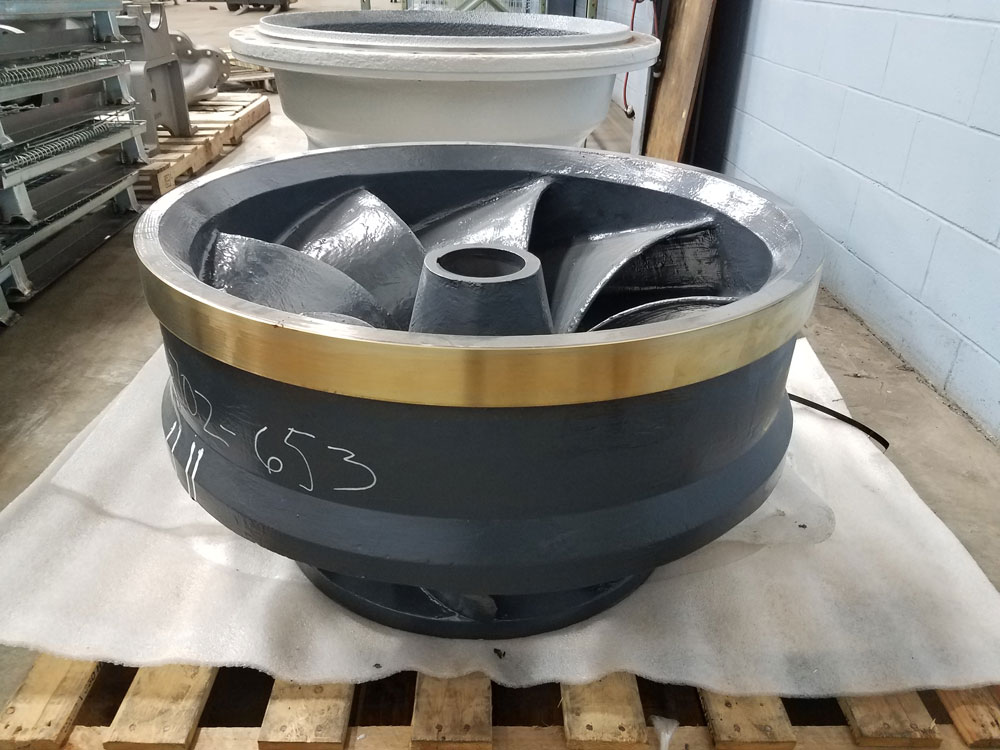
The current trend in the industry is to throw away or replace older, more obsolete pumps that may be at the end of their life with new pumps. Most of those decisions are fueled by the manufacturers of those older pumps having closed down or discontinued the line.
The other factor is the efficiencies of those older pumps are lower than a newer pump, and it might need extensive repair. However, advancements in thermal spray and epoxy coating technology have evolved to the point that it is now possible to restore pumps that would normally be thrown away back to like-new condition. This includes bringing the efficiencies back to the original design.
Why should the restoration process be considered over purchasing a new product? The restoration process saves 70% of the raw material costs and 80% of the energy costs consumed by manufacturing a new product. Restoration is a green process that can help end users lower their carbon footprint. The restoration process, in most cases, can be done for less money than buying a new pump, has a faster turnaround, and the end user does not have to make any changes to their pump base or piping—meaning there is no need to purchase additional equipment.
What Is the Restoration Process?
The restoration process typically uses three types of modern-day technologies to bring the pumps back to like-new condition: twin wire arc spray, plasma spray and epoxy coatings. The main benefit of restoration is it is now possible that an old, obsolete or discontinued pump can be made “better than new” using the twin arc wire, plasma spray and/or epoxy coating method.
Twin Arc Wire Process
The twin arc wire process has been used by the United States military for over 30 years. The twin arc wire process is similar in function to a MIG Welder where the wire is fed to a nozzle, but that is where the similarities end. The process uses direct current (DC) power to energize two conductive wires, one positive and one negative, that are shorted against each other to create a molten metal that is then sprayed against the surface needing repair.
The molten metal is applied until the surface is larger than the original dimensions. It is then machined or ground down to the pump’s originally designed dimensions.
Benefits of the twin arc wire process include:
- The process does not heat the base metal over 300 F.
- There is no melting, distortion or warping of the base metal.
- It allows any metal to be sprayed on any metal, if it can be supplied in a wire form.
- There is no galvanic reaction if the metal combinations are chosen properly.
- The adhesion of the spray to the base metal and to itself has a bond strength exceeding 9,000 pounds per square inch (psi).
- Depending on the metal being used, the surface can be built up to 2 inches thick.
- Once repaired with the twin arc wire process, the part can be repaired indefinitely.
Plasma Spray Process
Plasma spray is a flame spray process where a powder is injected into the plasma flame using an inert gas. The flame melts the material and then sprays it against the surface needing repair.
Benefits of the plasma spray process include:
- The process will not heat the base metal over 400 F.
- There is no melting, distortion or warping of the base metal.
- It allows any metal to be sprayed on any metal, if it can be supplied in a powder form.
- There is no galvanic reaction if the metal combinations are chosen properly.
- It can be used for hard coating and thermal barrier coatings that cannot be made in wire form.
- Once repaired with the plasma spray process, the part can be repaired indefinitely.
Epoxy Coatings
Epoxy coatings have come a long way over the years through advancements in chemistry and various technologies. Advancements in epoxy technology have made it possible to “glue” a locomotive to multiple train cars exceeding 205 tons and pull them without the train breaking free. The same technology is used in hard coat, low friction and chemical resistant epoxy coatings.
Benefits of the epoxy coating process include:
- The process does not use heat.
- There is no melting, distortion or warping of the base metal.
- It allows epoxy material to be applied to any metal.
- There is no galvanic reaction.
- It can be used for chemical and wear resistance.
- Once repaired with the epoxy coating process, the part can be repaired indefinitely.
Apply a hard coat metal finish such as tungsten carbide, Hastelloy or ceramic over the base material with the twin arc wire or plasma method, and then add a finishing topcoat of an appropriate epoxy coating designed for the application. Using this combination, the part is returned to its original design and performance. The other benefit of this process is that when this combination of coatings is used to restore a part, the part can last longer under normal operating conditions than the original manufactured part by multiple times, reducing maintenance and replacement costs.
The process can be used to convert “packing” in older pumps with mechanical seals for additional operating reliability and lowered overall maintenance. It can be used to restore packing glands and packing areas on shafts to resist wear and chemical attack.
Some of the coating processes mentioned above are National Sanitation Foundation 61 (NSF61) and Food and Drug Administration (FDA) compliant and can even be used for drinking water and food contact.
There has been ongoing discussion in the industry relative to repairing or replacing a pump. A new consideration to factor in is the restoration of old, obsolete pumps to be eco-friendly, especially with current supply chain issues. Most people want to do their part in preserving the environment by being aware of their carbon footprint and the impact each of us contributes to pollution. Restoring an existing pump reduces carbon footprint by minimizing mining and pollution caused by manufacturing parts used in new pumps.
Using the restorative processes described here can do just that, as they start with 90% or more of the original product. By adding a minimal amount of additional product, spray coating or epoxy coating, the pump is brought back to its original operating specifications.
With continued focus on preserving the environment, it makes sense to restore/repurpose the existing equipment already available in a plant by utilizing the latest coating technologies.