When pump systems are not optimized, it impacts a facility’s bottom line with increased maintenance, lost production and higher energy costs. System optimization is a cost-effective way to improve reliability and reduce energy consumption while improving process control to meet the process requirements. However, it is not always apparent what systems need optimization, and the expertise may not be available on staff to determine which systems need to be optimized or how to optimize them. A pump system assessment conducted by a qualified professional is the primary tool used to optimize a pumping system by identifying problematic areas where the greatest opportunities for improvement exist that will provide the greatest return on investment. The pump system assessment process can be divided into four equally important, major tasks: pre-screening; development of the assessment team; detailed measurement, data gathering and analysis; reporting. Two more steps following the assessment are important, which are implementation of optimization recommendation, and measurement and verification.
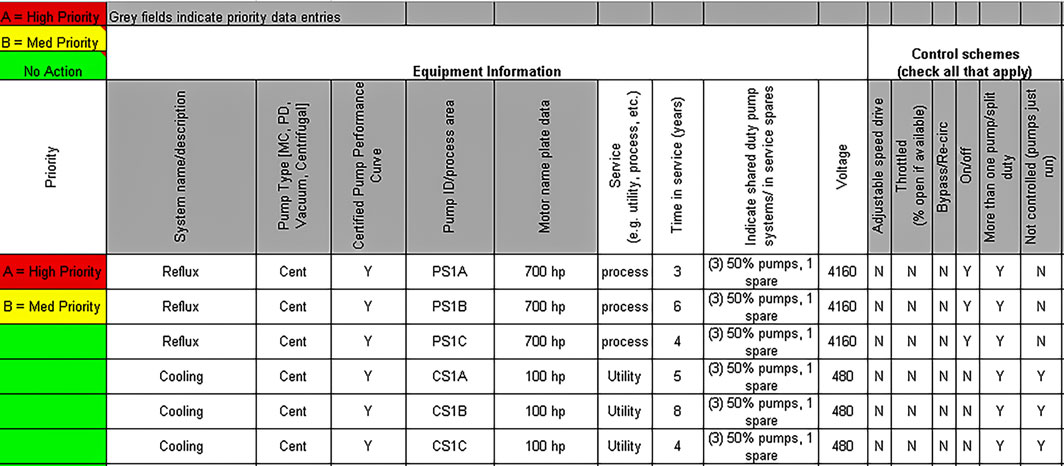
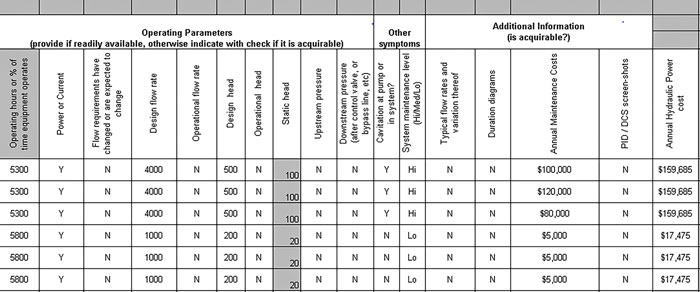
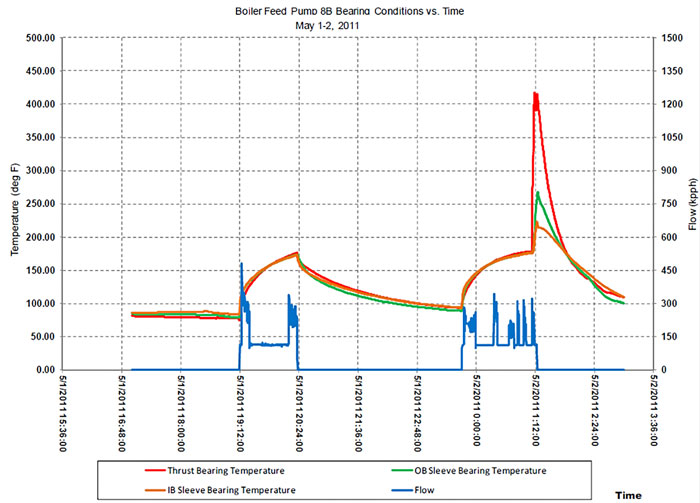