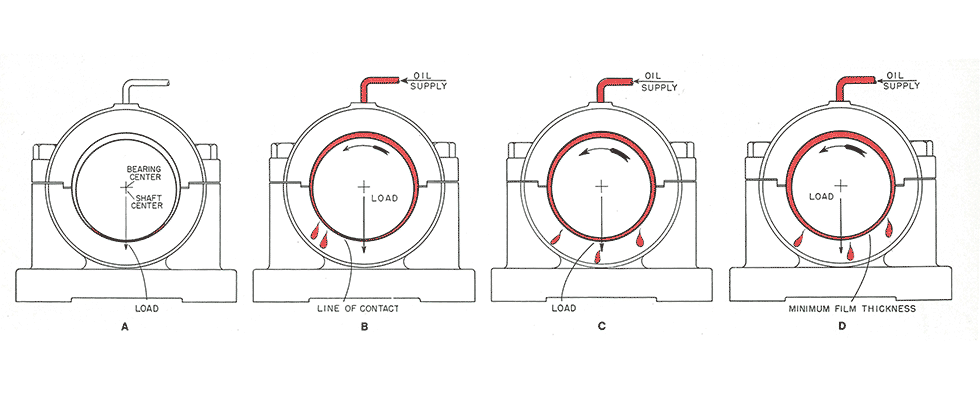
Bearings, by definition, keep the world going around. Without bearings, motion becomes exponentially more difficult. The most common bearings are rolling element bearings that use balls or cylinders to allow rotation to occur within a system.
Oil Viscosity
In the motor and pump industry, most fluid film bearings are a hydrodynamic design that use motion to create the required pressure to force surfaces apart. They are commonly lubricated with a Newtonian fluid, such as oil, that has a flow rate directly proportional to the pressure applied. The viscosity of the oil is what allows for hydrodynamic film and pressure formation. Visualize the oil film made up of many internal layers; each layer is drawn by the layer above at a multiple of the velocity of the moving element. These layers within the oil cause friction. The force required to cause motion in the moving element is directly proportional to the friction between the layer of oil. Viscosity is measured and determined by the force to overcome this internal friction.
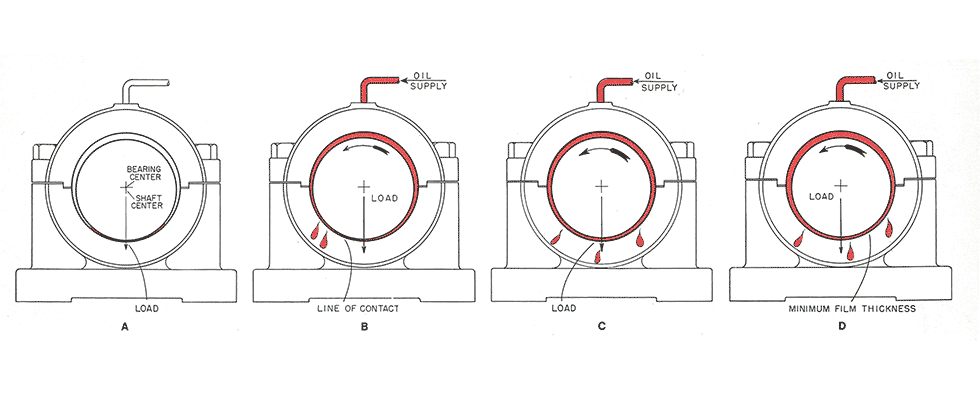
If lubrication failures are found to be a common issue when having equipment inspected, it is recommended to evaluate the viscosity of the oil being used. Temperature, application and load can all play a factor in lubrication efficiency. Contact the OEM with all application details for guidance on the correct oil. Often, equipment is designed for general purposes but can be modified to fit specific applications. If installing a new system is being considered, ensure all details about operating conditions are given to the manufacturer. The correct lubrication can mean the difference between a unit running 10 months and 10 years.
Clearance
With this understanding of viscosity and oil, it can be examined how it is manipulated to create an oil film for lift and separation for equipment rotation. Using a converging and diverging wedge, design pressure is generated and released through the squeezing and releasing of the oil. In a radial bearing, the bore is typically designed to be 0.001 to 0.002 inches larger than the shaft. This equates to 0.005 to 0.010 inches of clearance for a 5-inch shaft.
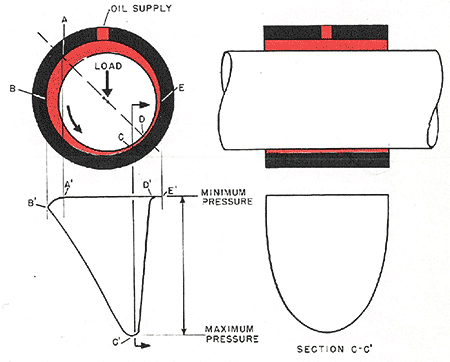
Actual clearance varies by manufacturer and application. This clearance is what allows for the formation of the converging and diverging wedges. As the oil is drawn into the wedge formation by the rotational forces of the shaft, it is compressed into the smaller space. This causes the pressure to increase. It also creates and allows for a lift of the rotating component. As the oil leaves the compressed space, it is drawn into an uncompressed space along a diverging wedge.
Converging Wedge
When a machine is at rest, metal-to-metal contact can exist. Prior to startup, oil should be applied to allow the shaft to ride up and slip into position. Due to the initial friction on startup, the shaft will ride up the side of the bearing slightly as the initial supply of oil is drawn into the converging wedge of the bearing. Pressure will begin to rise as the oil is compressed, which will lead to the separation of metal-to-metal contact. The shaft will then shift into operating position, as the fluid film forms along the journal and bearing. This point is left or right of the load, dependent upon rotation.
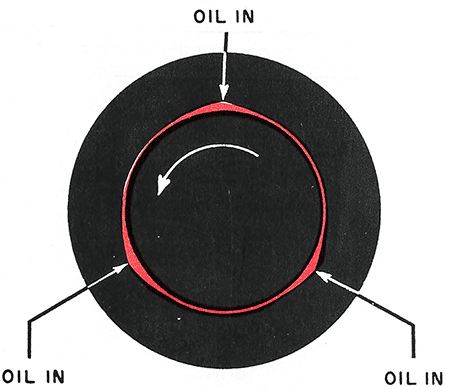
Under consistent conditions, the force developed by the oil film equals the load applied in a slightly eccentric position. The smaller end of the wedge is where the minimum film thickness is. Bearing systems within a motor or pump are designed with this eccentricity in mind. End leakage will play a factor regarding the supply oil. Enough oil must be deposited to allow for the oil film to form, as end leakage occurs along the converging wedge. This is also the point where the diverging wedge begins.
Diverging Wedge
The diverging wedge begins as the maximum pressure/minimum film thickness zone is passed. It allows for pressure to release into the low-pressure clearance zone in the system. This low-pressure zone is created opposite of the bearing load. It is at the exit of the load zone that the diverging wedge begins to draw out oil with negative pressure. Bearing dimensions, speed, load, viscosity and supply pressure determine the extent of negative pressure that can exist prior to positive pressure regenerating. The pressure falloff in the diverging wedge is more rapid as the rotating element is drawing the oil out, while the converging, high-pressure side is pushing it out. End leakage is also a factor that determines the rate at which pressure falloff occurs. This allows the oil to cycle for heat dissipation and re-entry into the converging wedge to begin the process again.
Vibration & Design Changes
The center of the journal on a hydrodynamic fluid film bearing will ordinarily ride in a stable, slightly eccentric position within the bearing. This position and stable condition are dependent upon the load, speed, clearance and oil viscosity (Image 2). Most higher-speed, light load applications closely approach bearing center during its eccentric operation. There is a possibility with simple cylindrical bearings the journal will orbit the stable point of operation. This motion is known as oil whip or oil whirl. This phenomenon is not related to machine critical speed as it is with some vibration issues. It can be corrected through various methods, such as adding lobes, an elliptical bore, linear grooving or tilting pads, to name a few. These added features allow for alternate fluid pathing that will stabilize journal motion by calming the oil discharge area. These changes should be considered if oil whirl is suspected. All application data should be considered prior to any modification of the existing bearing system. It is recommended to have design changes verified with engineers or the machine’s OEM.

A bearing is a component in a system that does a relatively simple job. However, the design consideration and functionality are more complex. If the wrong design, clearance or oil is specified, failure will be imminent. Ensuring the bearings are dimensionally correct is the most essential portion of the design. If improper clearances are given, the journal will not ride in the correct position within the bearing and vibration can occur. It will also not allow the system to build up the correct amount of pressure for proper lubrication and lift. This will cause the journal to ride more eccentric than designed or impact the bearing wall and damage the lining material. Proper design is critical for proper function.
Read part 2 on the history and dynamics of fluid film bearings.