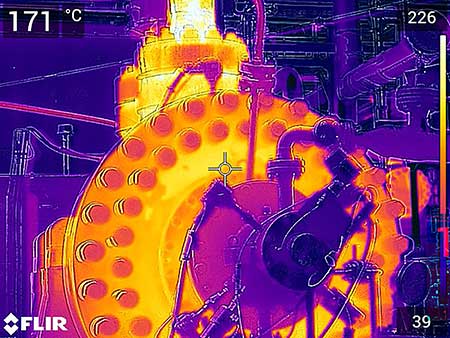
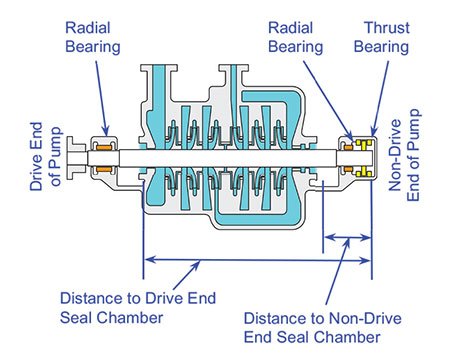
High temperature pumping applications can be found in nearly every industry. Learning how to handle them is critical to ensure reliable operation.
Fluids are pumped at elevated temperatures for a number of reasons:
- The fluid needs to be heated to change it from a solid or semi-solid into a liquid so it can be more easily moved, processed or applied.
- A process where heat is used as a catalyst to initiate or sustain a chemical reaction.
- A heat transfer medium to transfer heat energy from a heat source into a process.
In all of these cases, the pumps are subject to the effects of dimensional changes caused by thermal expansion of the pump components as a result of the hot fluid flowing through the pump.
When sealing the pump shaft of high-temperature pumping applications, the mechanical seal is often subjected to axial displacement as a result of dimensional changes. Pump operating temperature and differences in thermal expansion and heating rates of the pump casing relative to the pump shaft, can result in axial growth of the shaft in the seal chamber.
Compared to the position of the shaft in the seal chamber at ambient temperatures, shaft growth may occur as a result of:
- Differential heating rates of the shaft relative to the pump casing as the pump is preheated in preparation for startup.
- Differences in thermal expansion rates of the pump casing and shaft due to different materials of construction (that produce shaft growth during preheat and while at temperature).
Shaft axial growth is greater the farther away from the thrust bearing the seal is located. Single-stage pump designs have relatively short shafts; thus, these effects are small. However, as the length of the shaft increases with the addition of stages, these effects are magnified. These effects are most pronounced in between-bearing multistage pumps.
Typically for between-bearings pumps, the thrust bearing is located at the nondrive end of the pump. As a result, the drive end seal chamber typically experiences the greatest axial shaft growth.
There are other factors that can impact the shaft thermal growth including the mounting location of the pump on its baseplate (foot-mounted versus centerline-mounted) and piping design causing thermally induced strain at the pump’s suction and discharge flanges.
Mechanical Seal Considerations
Pump manufacturers design pumps to produce as little as possible axial movement resulting from thermal growth. However, it is always present. The challenge for the mechanical seal is the design of the seal arrangement needs to be able to tolerate this displacement without negatively impacting seal performance, and the key to achieving this is knowing the magnitude of the displacement and the direction (into the seal chamber or out). This is typically determined by field measurements or analytically by the pump manufacturer for the specific operating temperature of the pump.
Additionally, many multistage pumps have tilting pad thrust bearings that can have axial clearance up to 0.025 inches (0.65 millimeters [mm]). Increased thrust bearing clearance is frequently required for pumps with specialized spring-loaded thrust compensation devices. The bearing clearance and expected shaft motion during startup should be shared between pump and seal engineers to ensure a full understanding of shaft axial position during operation.
Typically, a high temperature cartridge mechanical seal can accommodate an axial displacement of up to 0.040 inches (1 mm) in either direction from the seal’s installed position at ambient temperature.
Once the displacement is known, it can be compared to the capabilities of the mechanical seal. For situations where the magnitude of the displacement is approaching or exceeding the limits of the seal, one solution is to compensate for the displacement through the design of the mechanical seal cartridge assembly.
This is achieved by offsetting the position of the mechanical seal’s rotating assembly on the shaft at ambient temperatures so that as the pump is heated up to its service temperature, the shaft thermal growth moves the seal into its designed operating position.
Using this method, the mechanical seal typically will be able to accommodate up to 0.080 inches (2.0 mm) axial displacement in one direction.
There are limits to how much axial growth can be accommodated using this method determined by internal clearances within the mechanical seal assembly and, more importantly, the axial travel capability of the seal.
For applications requiring more axial travel than available with standard mechanical seal designs, mechanical seal manufacturers can create special long travel designs as a point solution. These solutions can be tailored to accommodate axial shaft displacements in excess of 0.2 inches (5 mm).
Hot Pump Preparation & Startup
Successful operation of a high temperature pump can be achieved when the equipment manufacturer’s installation and commissioning procedures are followed. The following summarizes two of the critical steps for preparing a high temperature pump for startup.
It should be noted that this summary does not represent a complete list of all requirements that should be followed.
Alignment checks
Properly aligned shafts will do more to increase bearing, seal and rotor life than any other single thing after lubrication. They provide reduced vibration, reduced bearing loads, decreased power losses and reduced wear. Alignment checks of the drive coupling should always be completed when:
- process temperature changes
- piping changes
- pump or driver has been serviced
Checking the alignment is a two-stage process:
- Initial (cold) alignment check— performed prior to operation when the pump and the driver are at ambient temperature.
- Final (hot) alignment check—performed when the pump and the driver are at operating temperature. This can be completed after preheating or after a short duration of operation.
For further information regarding the recommended practices for pump installation, refer to the American Petroleum Institute (API) document “API RP 686 Recommended Practice for Machinery Installation and Installation Design.”
Pump preheating
Correct preheating of the pump is important to prevent damage to the machine and the mechanical seal. The four areas to monitor for the correct preheating of a pump are:
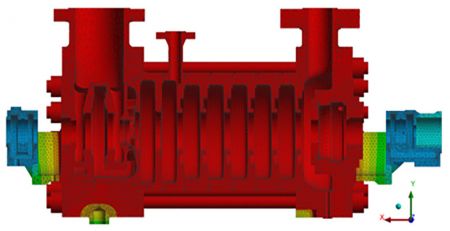
pump at operating temperature (Image courtesy
of Flowserve)
1. Heating Rate
Heating too fast will create temperature gradients that can produce uneven thermal expansion resulting in damage to the pump casing, rotating elements and close clearance wear rings, and the mechanical seal. The manufacturer can recommend heating rates as they are dependent on the type and size of the pump.
In the absence of guidance or specifications from the manufacturer, the recommended maximum heating rate is:
- a maximum heating rate of 100 F (50 C) per hour up to 500 F (260 C)
- a maximum heating rate of 50 F (25 C) per hour above 500 F (260 C)
2. Startup Temperature
A pump is ready once it is within a specified temperature margin relative to the operating temperature. This margin varies with the design as well as the pumped fluid and guidance can be provided by the manufacturer.
Once a pump is at its startup temperature, the metal temperatures within the pump are uniform and the fluid within the pump is approaching its normal operating viscosity. This is important for fluids that solidify at ambient temperatures.
Starting a pump before it has reached its required startup temperature can result in damage to the mechanical seal, pump wear rings and motor as a result of increased torque and friction losses from the increased fluid viscosity.
In the absence of any guidance or specifications from the pump manufacturer, the recommended guideline is: A pump can be started once the casing temperature is within 30 F (16 C) of the pumping temperature and the pump has soaked at that temperature for a minimum of 2 hours.
For multistage pumps that have installed multiple casing temperature probes (to minimize casing distortion due to temperature gradients), permissive starting interlock is based on differential temperature between the probes that is less than 50 F (25 C).
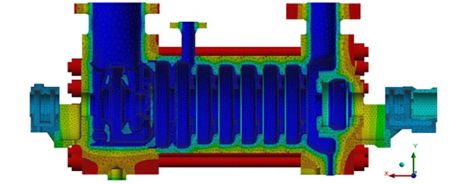
pump experiencing cold shock (Image courtesy
of Flowserve)
3. Thermal Stratification
Thermal stratification of pumps can occur during cooling and when pumps are not properly warmed. Due to density changes as a result of differences in fluid temperature in the pump, a thermo-siphon circuit can be established with hot liquid on top and cooler fluid migrating to the bottom of the pump casing. This causes unequal thermal expansion of the casing and rotor. Operation in this condition can result in galling between rotating and stationary components, vibration and seizure.
4. Thermal Shock
The rapid introduction of hot fluid into a cold pump (or the reverse) can result in thermal shock that may result in permanent damage or failure, and can have detrimental effects on the mechanical seal including seal face fracturing.
There are specific pump designs that are constructed to withstand thermal transients and do not require warming systems. An understanding of the normal transient conditions and pump construction are critical for proper seal selection and design.
Hot pumping applications offer some challenges for mechanical seals. While pump designs in many cases are optimized to reduce the impact of thermal growth on the mechanical seal, understanding its presence, magnitude and direction can be compensated for in the design of a mechanical seal to provide reliable operation of the shaft sealing system.
Additionally, as an operator of a high-temperature pump, following the equipment manufacturer’s guidelines and best practices for preheating pumps can prevent transient thermal growth damage to the mechanical seal.
We invite your suggestions for article topics as well as questions on sealing issues so we can better respond to the needs of the industry. Please direct your suggestions and questions to sealingsensequestions@fluidsealing.com.