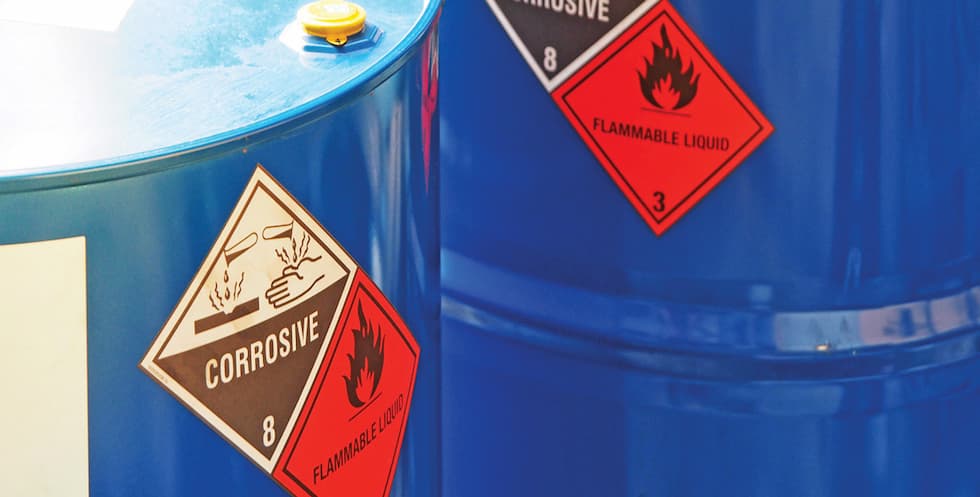
Facilities worldwide receive myriad liquids in drums and totes/intermediate bulk containers (IBCs). Safely and efficiently removing these liquids from these containers is key.
Benefits of Powered Pumps
Powered container transfer pumps offer multiple benefits:
Risk reduction—designed to withstand harsh chemicals and keep them safely contained during transfers, effectively mitigating employee and company risk
Versatility—available in models for high- and low-volume transfer, various levels of specific gravity/viscosity and diverse chemical-handling capabilities, for a full range of pumping solutions
Portability—easily transported for various tasks throughout a facility, with minimal footprint to conserve space or for use in smaller settings
Speed—able to transfer high volumes of fluids quickly and effectively to improve productivity and boost the bottom line
Durability—offering longevity and low maintenance throughout an extended life span, reducing cost and operating smoothly for a prolonged period, even under harsh conditions
Because there are so many options on the market, it is crucial to carefully determine which pumps are best suited to each application. Use the following four steps to determine which powered drum pump is best for the application and select the best model for optimum results.
1. Ask the Right Questions
Start by asking a series of questions about the specific application for which a powered pump is being considered. The answers to these questions will reveal the parameters of your pump needs and guide the selection process.
What is the required head and flow?
Depending on the size of the containers and the pressure capabilities involved, the application may require higher flow or head. If simple transfer is required, transferring fluid into a bucket for example, a pump with lower flow and head capabilities is typically sufficient. If the application involves transfer to a second story or requires an entire drum or tote to be emptied, a pump with higher head or flow capabilities will be required.
What chemicals are being transferred?
Many applications involve harsh chemicals like acids and bases. Will the fluid that the pump will transfer be flammable or combustible? To ensure safe transfer, the appropriate materials must be selected.
What is the temperature of the fluid?
Most powered pumps have temperature limits based on the materials of construction, as well as the length and style. For safe and effective transfers, it is crucial to consider the maximum temperature of the fluids being pumped. Many are being transferred at ambient temperatures but some, like certain plating applications, involve hot fluids.
What is the specific gravity and viscosity of the fluid?
Pumping fluids with high specific gravity may require a more powerful motor or a high viscosity fluid may require a specific pump type. Attempting to use a pump not designed for high specific gravity or viscosity can provide poor results so it is crucial to check these ratings. Refer to the chemical’s safety data sheet (SDS) for specific gravity information. Viscosity typically varies by temperature, so make sure the value being used is correct for the temperature of the fluid being pumped. Users may need to talk to the supplier about viscosity.
What is the container size?
The size of the container affects both the selection of the pump model and the length of the pump tube for the application since container height varies by volume. IBCs/totes and tanks require different solutions than smaller containers and drums. The emptying and filling of large containers may require pumps that can transfer significant volumes more quickly or have longer tubes (Image 1).
Are size and portability important?
Some applications require a pump that can be easily transported throughout a facility for various tasks. Others might require pumps with a small footprint to fit in tight spaces. If the pump must meet certain space parameters or provide highly portable use, these are important considerations as a pump is chosen. If the pump is going to be used in multiple applications, it is essential that the pump’s construction is safe and suitable for each application. High viscosity applications frequently require larger pumps with larger and heavier motors, so consider air motor options to reduce weight if portability is important.
Is there a motor preference?
Many powered drum pumps can be operated with various types of motors including air, electric, explosion-proof electric and lithium-ion battery powered. Consider the environment in which the pump will be used to determine if a particular motor is preferred for the application. If the pump is going to be used in a hazardous environment where flammable or combustible vapors are present, an explosion-proof electric or air motor will be required.
2. Select the Best Pump
Based on the answers to the parameters in step 1, choose the best pump for the application.
Materials of construction
Drum pumps are available in a wide range of materials of construction. These include the outer tube, the most visible portion but also the internal components like the drive shaft, impeller and elastomers.
Gather the SDS for each chemical to be pumped. In “Section 3: Composition/Information on Ingredients” of the SDS, a list of the chemicals and percentages can be found. Using chemical resistance guides that are offered by drum pump manufacturers, confirm the materials of construction in a pump under consideration are suitable with the chemicals listed in the SDS. Another source is the chemical manufacturer or supplier.
If the material to be pumped is a flammable or combustible liquid, extra care is required. The pump, motor and accessories all need to be suitable for use with flammable/combustible fluids and use in hazardous locations.
Pump series
Specific series from drum pump manufacturers are designed for or have options for different types of applications. Some are designed for transferring large volumes of fluids in short periods of time while others are better suited to the transfer of small quantities. Others are ideally suited for pumping viscous or flammable/combustible fluids. Using the answers gathered in step 1, review the pump series offered by manufacturers or local distributors. This is also the appropriate time to select the tube length required for the application.
3. Choose the Right Motor
Pump motors are not all interchangeable. Each pump series is compatible with specific motors for optimal functioning. Many come with speed control to allow adjustment for precision flow. In addition, certain motors are better suited for some settings than others. Consider the type of location the motor will be operating in to choose the enclosure type. Choose the preferred power source (corded electric, air or battery powered).
The following are the most common motor options and their key features.
- Splash-proof/open drip proof (IP24): Economical and lighter weight than other electric motors, they are protected in every direction from water splashes.
- Enclosed/totally-enclosed fan-cooled (TEFC) (IP54/55): This type is sealed against water splashes, dust and corrosive fumes. It is the best choice for use with fuming chemicals and dusty environments.
- Explosion-proof (IP54/55): As with TEFC motors, this style is sealed against corrosive fumes, water splashes and dust. They have the added benefit of being appropriate for hazardous areas and are suitable for use with flammable or combustible liquids.
- Air: This motor style is compact and lightweight compared to electric motors. Because this type of motor offers nonelectrical operation, they are generally considered acceptable for use in hazardous areas and for use with flammable or combustible liquids.
- Lithium-ion battery (IP24): The portable, cordless design makes it easy to transfer fluids. It is typically found on pump series with lower flow ranges.
4. Make Sure You Have the Right Accessories
Some of the recommended accessories include:
- Hose: Hoses are available in a variety of lengths and materials of construction. Select a hose that is chemically compatible with the fluid being pumped, temperature and diameter to match the pump connection.
- Nozzles: These allow operators to better control the flow of fluid through the pump hose.
- Flow meters: Flow meters allow technicians to measure the fluid volume dispensed accurately.
- Strainers: Strainers protect the pump from potential damage from foreign objects. Some pump models even feature built-in strainers.
Doing the research and planning before investing in a powered drum pump helps ensure the correct choice is being made for safe operation and long life.