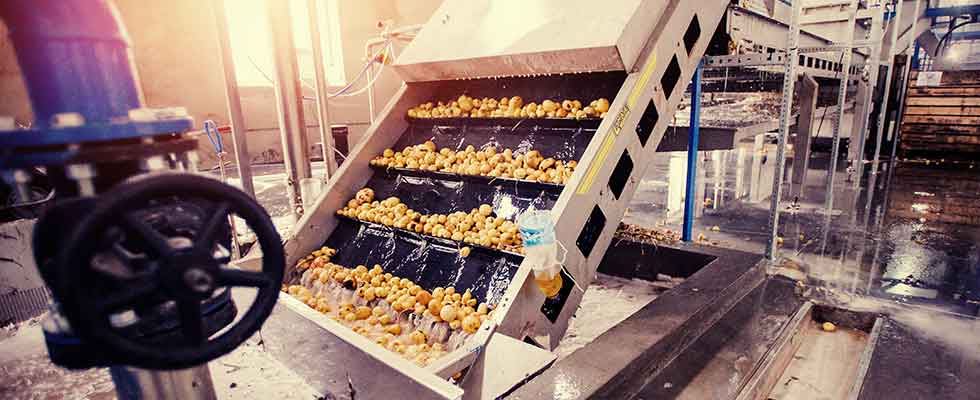
The food and beverage industry has faced its own challenges due to COVID-19. Pumps & Systems spoke with James A. Feltman, vice president of Tacmina USA, which provides pumps and related services to food and beverage manufacturers, and Karen Eng, Ph.D., the president and CEO of engineering firm CSMI, on how the industry has reacted to the coronavirus.
What are some of the biggest changes in the food and beverage industry since COVID-19 hit?
FELTMAN: Two main areas—first, customers are seeking to automate as much as possible. The more a manufacturer can reduce human contact with the process, the better for control and containment of potential issues not only for COVID-19-related issues but to reduce allergens and other potential contaminants. Second, our customers have raised the bar significantly when it comes to justification for a plant visit. Once on-site, there are a lot of safety protocols that must be adhered to in order to be in the manufacturing areas, such as frequent temperature checks, the wearing of masks and, in some cases, face shields, all in addition to the standard face (for those with facial hair) and head coverings, shoe covers and gloves.
ENG: We have experienced new protocols when entering the manufacturing facilities including temperature checks, required personal protection equipment (PPE) as well as the life span of the masks (no more than 12 hours). We have seen polycarbonate dividers between workstations to maintain social distancing. Employees will not have the same access to different areas within a plant and outside contractors have even less access. While the weekly sanitizing crew still comes in, the plant is requiring more frequent sanitation of each area to help lessen the chance of any spread. Any area that an employee or contractor works in must immediately be wiped down and sanitized by that person or group. There have also been many initiatives to automate and increase production throughputs with many Americans buying more grocery items. Lastly, there have been many requests by our clients to optimize their manufacturing lines. For example, the two-second lag per cycle was tolerable prior to COVID-19, but became amplified when demand for product increased. This has led to pivoting our engineering company to include this scope of work.
What new ways of doing jobs in the food and beverage processing industry are we seeing?
FELTMAN: As I mentioned, food and beverage manufacturers are moving more and more toward automating the manufacturing process. And we are seeing a strong interest in process components that can be swapped with items that are sanitized offline and can be easily implemented on a process line. This reduces the amount of human contact with the process and ensures the highest cleanliness standards.
ENG: We have seen huge initiatives on promoting safety and wellness. Safety addresses the physical being, while wellness deals with physical and mental health. Our food and beverage clients see that if the overall health of the worker is improved, it decreases absenteeism, increases productivity and improves capabilities of the workers.
There have been clearer and more effective communication plans. This includes COVID-19-related communications and strategic planning. A majority of our projects are automation and integration specific. With increased production, automating production and packaging lines are more consistent and accurate. Data can be acquired from programmable logic controllers (PLCs) to monitor efficiency and line downtime.
Which aspects of the industry have been the hardest hit? Can they bounce back?
FELTMAN: I would say that those manufacturing models that require a lot of people to make the product, processes that are less prone to automation such as butchering and natural product
processing, and products that are not easily automated because of the unique product mix. These often require a
trained individual to produce the product. For example, you would be hard-pressed
to find a cost-effective robot to process meat or fish.
ENG: I think the overall supply chain management has been most affected. There has been a shift from food service and restaurants toward grocery. I believe this can bounce back as businesses and restaurants are reopening and more people are willing to leave their homes.
There have been shortages of certain packaging items such as cans and bottles based on supply chain modifications. For example, one of our projects includes installing a new bottling line with which the bottles are being utilized for both salad dressing and hand sanitizer. With the increased need for hand sanitizer, there is a backlog of bottles for the salad dressing. I do believe they can bounce back once inventory is built.
We have experienced less business travel on-site as the manufacturing facilities are limiting the quantity of people within their facilities. A lot of corporate staff have been working from home, so that limits in-person meetings. There are also those who are not willing to travel or at high risk of contracting COVID-19. I would anticipate that the manufacturing facilities workforce has had a shift with those uncomfortable with COVID-19 virus remaining at home.
How hard is it to enforce safety and social distancing measures in the industry?
FELTMAN: From what I have seen, people understand the issues that we are facing right now and do a great job of maintaining social distancing and safety protocols. Plus, companies have been doing a good job of putting their own safety measures in place, such as clear dividers to contain contact and almost force social distancing. We have seen a lot of new signage in food manufacturing facilities as passive and active workforce training.
ENG: It is extremely difficult. Most food and beverage facilities simply do not have the spatial requirements needed for social distancing. These facilities are so compact that any procedures a plant may put in place will simply not be enough. Of course, that should not deter anyone from enforcing the procedures. With the constant interaction needed for area coverage, troubleshooting and monitoring among other things, at multiple points within a shift, any social distancing will have to be broken.
Are there pumps/sanitation equipment/mixers that are in more demand these days because of coronavirus?
FELTMAN: Definitely. There is a strong interest in new technology for making it easier to sanitize processes as well as water treatment. Water treatment both pre-process and post-process are nearly half of our discussions these days around plant health and safety improvements.
ENG: We have seen a few of our clients implement new projects to add new mixers due to the increased demand of their products. This would include the addition of pumps and sanitation equipment.
How do you see the future of the industry? Do you think the industry can go back to the way it was before?
FELTMAN: I don’t think the industry will ever be the same, but I also believe that the “new normal” probably accentuates the health and safety of consumers as well as the employees of these manufacturing plants. Truly, the future of food and beverage manufacturing will increasingly rely on automation.
ENG: I think just like the world changes and we adapt, the industry will change and we will have to adapt. I do not believe the industry will ever go back to how it was before. At some point, this pandemic should be better controlled. The biggest lookout will be how to prevent or be better prepared for another pandemic, whether it is a second wave of this or something separate. It is best to be proactive instead of reactive.