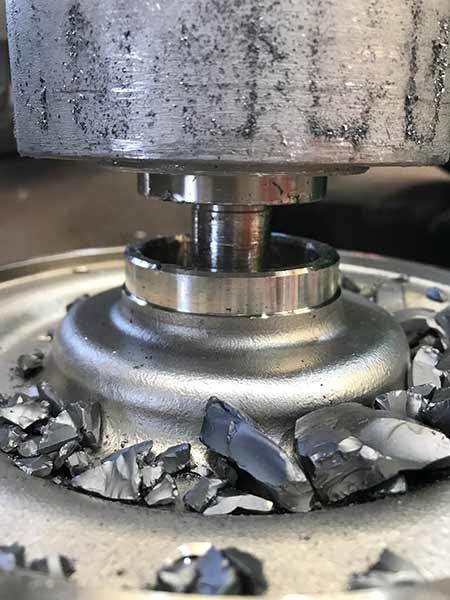
Anyone familiar with industrial magnetic drive (mag drive) pumps has been asked about dry running the pump. After all, a dishwasher and washing machine at home does that all the time. There are bearing materials that allow that, right? Sure, a qualified “yes,” but it is time to take a closer look at dry running.
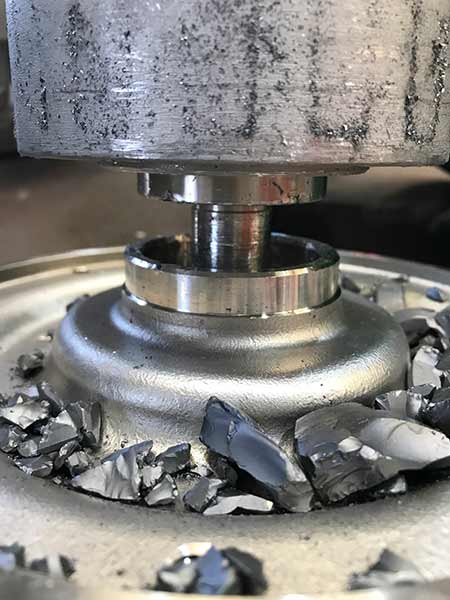
Dry running, except in the literal sense, is a misnomer. Industrial pumps are mechanically sealed or sealless and can suffer from the results of what the industry has dubbed “dry run operation.” This article will focus on the mag drive pump configuration with silicon carbide (SiC) bearing components, which is one of the two sealless types of rotodynamic centrifugal pumps.
Mag drive pumps have product-lubricated bearings that require liquid to be present for proper operation. These hydrodynamic (plain) bearings depend on a fluid barrier separating the bearing components that becomes a wedge when there is relative motion between the two surfaces. When this fluid barrier is disrupted, the two surfaces will touch and can lead to component damage. This effect can be cumulative, resulting in component failure when limits are reached.
If the SiC surfaces touch during operation, the components can break in a short time (depending on several factors). This does not mean the pump stops operating immediately. The broken SiC pieces may still support the shaft well enough to allow rotation of the pump rotor. Broken SiC can be detected by increased vibration and often a power increase. The condition of the pump will only get worse if operation is continued.
When the pump loses suction, it should be shut down immediately. Damage to the SiC components can occur in a matter of seconds. Using a power monitor to detect when the motor load has suddenly changed, such as when the pump loses suction, will protect major pump components. Continued operation without adequate liquid at the suction can quickly lead to severe damage of the SiC components.
For long life, the pump requires only that there be liquid available, operation within the pump flow range of the curve, and within the pump design limits. Please note that it is best to start the pump against a partially closed (about a quarter open) discharge valve. The suction valve should always be open when operating and only closed when the pump must be isolated for maintenance reasons.
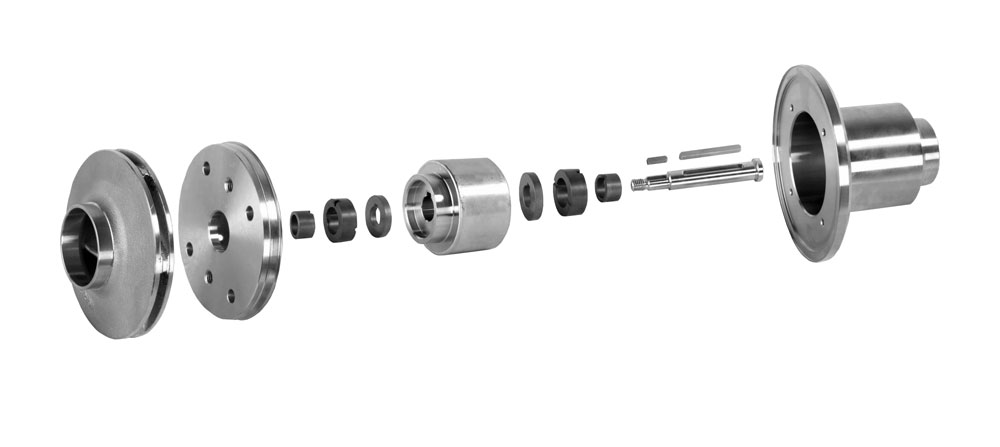
SiC Bearing Components & System Upset Conditions
SiC bearing material does not tolerate mechanical shock, which is what occurs when there is insufficient lubricating liquid between the bearing component surfaces, leading to contact between the components. There are several situations during system operation that can produce such conditions.
The following are considered system upset conditions, during which the bearing lubricating film barrier is compromised:
- operation of the pump with valves closed
- insufficient pressure at the pump suction (inadequate net positive suction head available [NPSHa]) causing cavitation
- extended periods of operation at extremely low flow conditions
- extended periods of operation at high flow conditions with low pressure resistance at discharge—operation “off the curve” or beyond the maximum flow range
- excessive cycling of system flow from one flow rate to another
- excessive temperature that causes pumped liquid (lubricating flow) to vaporize at the bearing component surfaces—or not enough internal system pressure to keep the pumped fluid in liquid state as it passes through the pump
- energizing motor without liquid in the pump, including briefly to check rotation
- plugged impeller vane inlet at suction eye
Specially treated sintered SiC is available from a number of suppliers to provide enhanced dry-running capabilities in the case of a system upset condition. Some manufacturers use coatings that adhere to the substrate SiC, while others use infusion methods that mechanically integrate the coating into the base material. All of these are called diamond-like coatings (DLC) in the industry. These treatments substantially reduce the surface coefficient of friction compared to that of standard sintered SiC. Less friction during system upset and other dry run conditions generate less heat, reducing the potential for bearing component breakage from mechanical contact or thermal shock.
In reference to pumping equipment and product lubricated bearings, no one recommends that the pump be operated without liquid passing through it. There is some residual liquid that remains when the unit loses suction, but that will quickly be pressed out of the sides of the bearing components with continued operation. Vaporization of the liquid can occur quickly, depending on the size of the pump.
Definitive dry run times would require specific testing of the pump size and conditions of service in question. For small pumps under 2 horsepower (hp), testing has shown that the dry run time is minutes and can be stretched to more than an hour for the smallest pumps with the DLC coated bearings. The greater the power input to the pump, the shorter the time period before damage occurs in the bearing system. For larger pumps in the 50-plus-hp range, while DLC coatings will still help, the time before damage occurs remains quite short. Energizing the motor to check rotation of a pump without DLC coated bearings or liquid in the unit will likely result in some bearing damage. Damage from dry running will initially appear as cracked or chipped SiC components. As the liquid vanishes and the rotating ceramic components come in contact with stationary components, the SiC can shatter, breaking into small pieces. Continued operation damages more pump components such as the shaft, rear casing, casing cover and impeller—all of which are costly parts. This type of damage to the pump is preventable.
Again, it is recommended that the pump be protected by a power monitor and that the low power trip point be set at a level representing the first indication that suction has been lost. Setting the low trip point time delay at less than 2 to 3 seconds can prevent tripping of the pump when a large bubble of vapor/air vents through the pump without losing suction. Trying to run longer to empty the suction line of product will result in damage to the pump that is more costly than the small amount of product that may remain in the suction line. A properly set power monitor will save money for the pump owner in several enterprise accounts.
Lined, mag drive pumps use either SiC or nonmetallic bearing materials. Some of the latter may have enhanced lubricity but are still subject to the same axioms of running with compromised lubrication.
Canned motor pumps, the other sealless centrifugal type, typically use softer bearing materials including carbon that are more lubricious, but susceptible to wear. These require a bearing monitor system to avoid component damage.
With mechanically sealed pumps, seal faces operate on a similar hydrodynamic film and require the same type of lubrication. They will not run dry long without damage either.
Most damage to mag drive pumps can be avoided. The best answer to the title question is, do not run the pump dry.