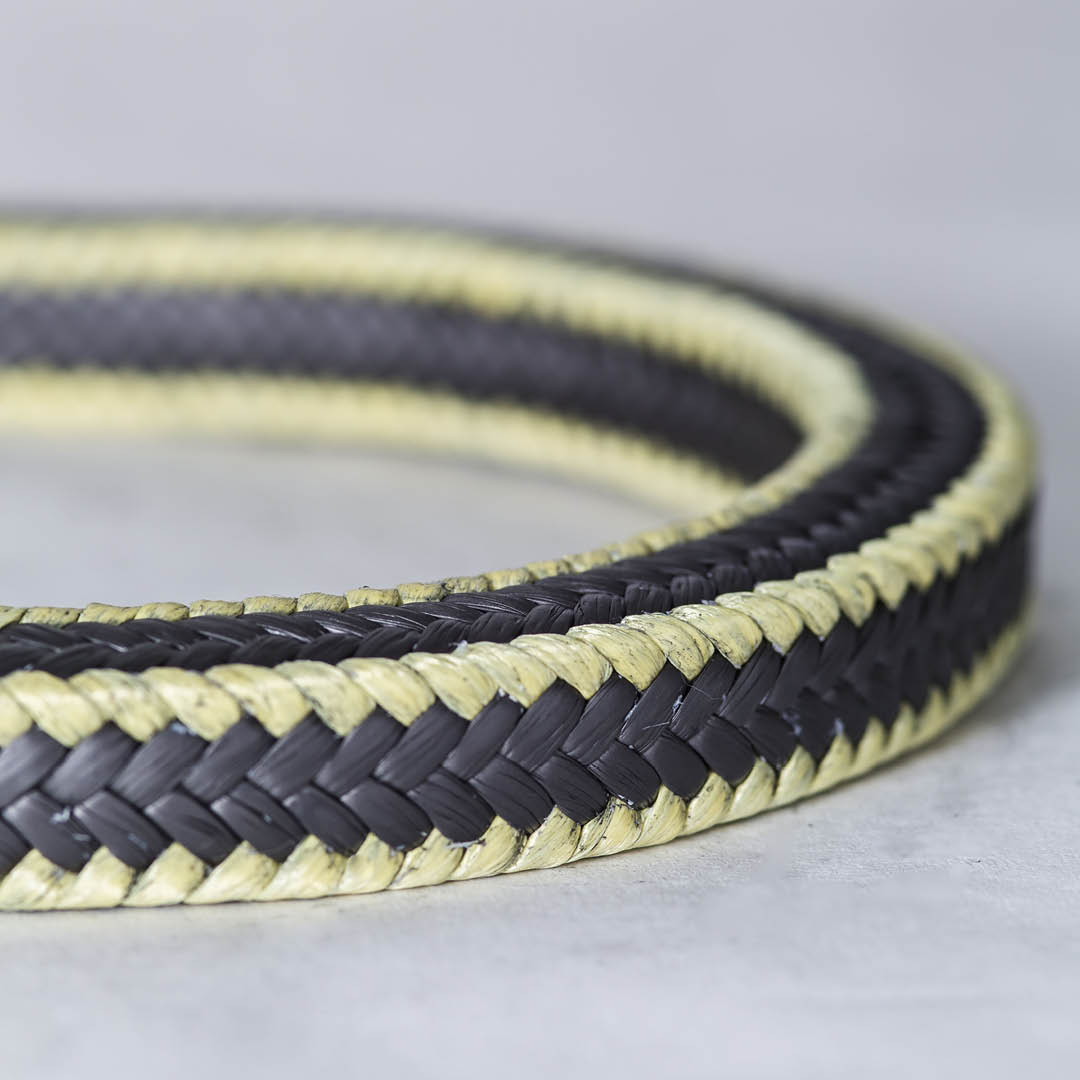
A plant has a process application that needs to be sealed. Which sealing technology should be used? The options to seal the process include:
- braided compression packing (hundreds of fiber types and lubricants/coatings available)
- mechanical seals
- air seals
How do end users and equipment manufacturers determine the ideal seal for their application?
Environmentally Safe Fluids
Clean, environmentally safe fluids can often be sealed with braided compression packing. Hundreds of packing fibers are available, and these can be combined with several different lubricants and coatings for compatibility with the pH, temperature, fluid makeup and shaft speed of the application. Properly specified and installed packing can efficiently and successfully seal these applications.
If the fluid being pumped is cool and clean enough to lubricate and clean the packing, flushing through a lantern ring may not be required. However, the majority of compression packing applications need a flush line into the flush port. This flush can be from the process fluid if it is cool enough or from a separate flush water setup. This ensures that the stuffing box environment is properly cleaned and cool to prevent shaft wear and increase packing life.
However, a stuffing box with packing installed must leak. Even if the fluid is environmentally safe, this leakage may not be allowed in the plant.
Some reasons for this are:
- housekeeping issues that prevent the small amount of leakage from the stuffing box
- the possibility of slip and fall safety issues around the equipment
- the product is too costly to allow for leakage
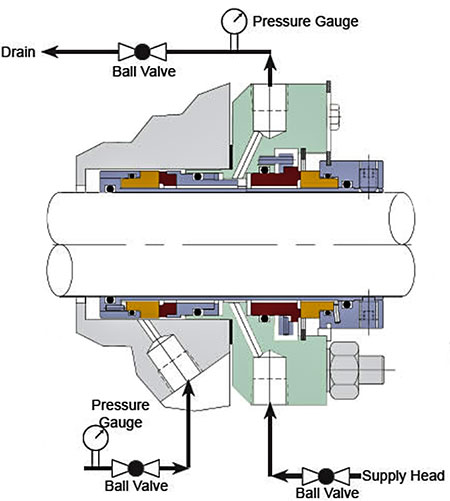
In instances where leakage from the stuffing box is prohibited or not ideal, a mechanical seal may be used instead. Relatively clean process fluids with adequate lubricating properties can be contained with a single-seal arrangement. These seals are typically less expensive to install and simpler for teams to operate and maintain.
A separate lubrication system is required if the process fluid inadequately lubricates the seal faces. In these cases, a double seal arrangement must be installed. A double arrangement (Image 2) helps ensure mechanical seal reliability and prevents the flush or barrier fluid from entering or diluting the process fluid.
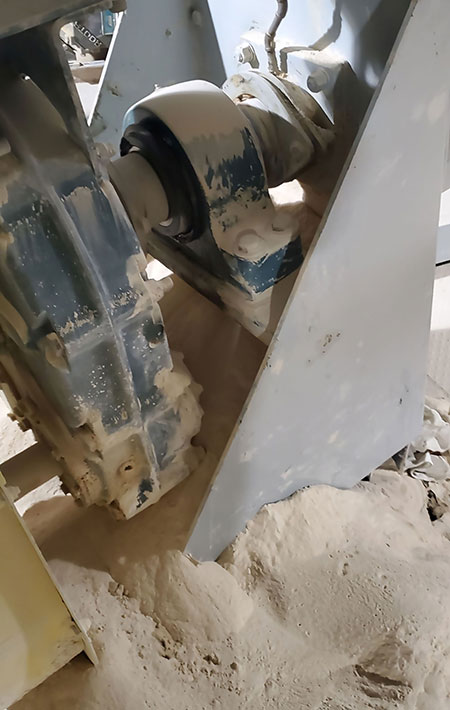
Environmentally Hazardous Fluids
Because compression packing must leak and single seals allow vapor to escape, they cannot be used to seal hazardous fluids. Hazardous or corrosive fluids must be sealed with a double seal configuration and be lubricated with an exterior barrier fluid, such as water, synthetic lubricant or glycol. Another option is magnetically sealing these applications.
Slurries
When handling process fluids with heavy solids content, such as municipal wastewater, food processes (syrup or ketchup), black liquor in pulp and paper, and mine tailings—robust seals are required. Seal technology that eliminates or reduces shaft wear is critical. In these processes, compression packing may not be the first choice. Particulates may embed in the packing and be difficult to flush away. They will cause excess wear and friction making packing less than ideal for slurry applications.
The first solution for these types of applications is a single mechanical seal with an external flush system. The next solution is a double-arrangement mechanical seal. Another option is an air seal system (Image 5). The system is made up of a noncontact tandem seal that uses air to seal and water to clean and cool the stuffing box—minimizing or eliminating particulate damage to the seal components. The system includes:
- two shaft-supporting bushings (to minimize shaft deflection)
- air seal
- lantern ring (for flush water)
Because the air seal is noncontact and floats above the shaft, the system uses little energy. It is also resistant to system conditions that damage or destroy traditional seals and pumps, such as:
- pipe strain
- misalignment
- off-best-efficiency-point (BEP) operation
- cavitation
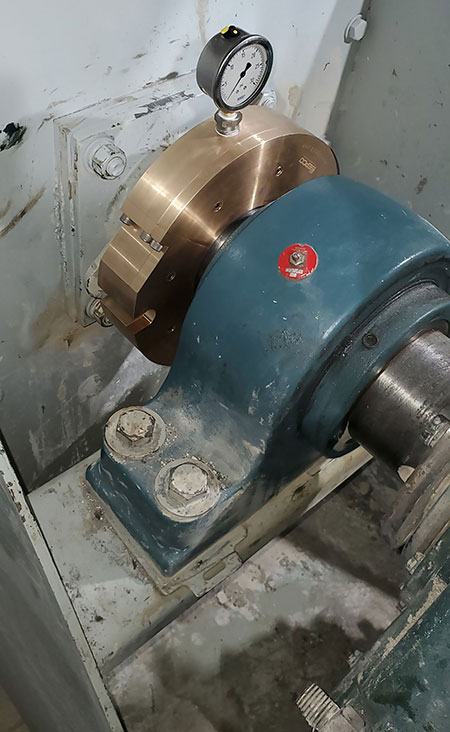
Dry Powders or Heavy Mixtures
Mixers, blenders, agitators and screw conveyors are some equipment types that move or mix powders or heavy slurries. These assets experience many issues if not sealed properly (Image 3), including:
- seal or equipment failure
- downtime and lost production
- replacement equipment or parts costs (this may require a crane or other service to remove the equipment or access the location to replace the parts)
- product waste
- other equipment contamination
- housekeeping issues
- personnel safety
- labor costs (operations, maintenance and housekeeping)
For these applications, a recommended solution is the noncontact air seal (Image 4). This seal uses a knife of air to seal the process, eliminating particle ingress into the seal. The floating throttle of these seals does not contact the shaft, so they cause little to no shaft or sleeve wear. They can also withstand ±0.125 inch of parallel movement, meaning they can handle the deflection that often occurs in these processes.