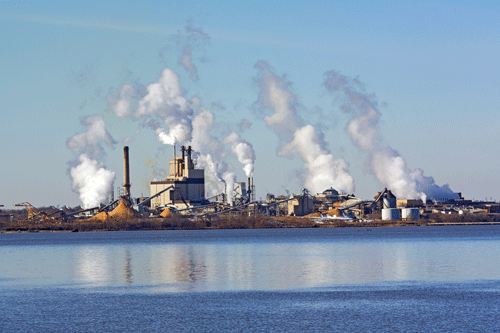
Pulp and paper mills are among the world’s worst polluters and consume a large amount of water. However, efforts are being made to become greener.
Tightening performance standards and increased regulations have seen stakeholders beginning to green their mill operations. Here are three key approaches being taken by the pulp and paper industry.
1. Optimizing Water Use
The pulp and paper industry uses more water to produce a ton of product than any other industry. Examples range from turning wood chips into a pulpy soup to the water-intensive bleaching process. While the average water intake per ton has decreased by 47% since the 1990s, as much as 100 liters (26 gallons) can go into making a kilo of paper.
In fact, it is estimated that 85% of water used for pulp and paper is process water. Growing pressure to reduce water footprints and increase efficiency has seen improved filtration and distillation procedures that allows that contaminated wastewater to be safely discharged or pumped back for alternate uses.
The water footprint of mills is further swelled by the hundreds of gallons of water used to clean the black liquor/red liquor evaporators that burn biomass-based black liquor.
2. Reducing Carbon Dioxide Emissions
A kilo of paper can result in approximately a kilo of carbon dioxide (CO2) being produced during its production, and this can increase to up to 1.2 kilos if the paper is not recycled. As a high emitter of carbon, the pulp and paper industry is in a strong position to make major contributions towards achieving a net-zero economy, and innovations are already being made to accomplish just that.
A 2022 Finnish study concluded that many mills already have the possibility to act as a carbon sink, with a CO2 capture rate lower than 6% enough to make all the studied market kraft pulp mills carbon-negative. It has been shown that biogenic carbon emissions captured from mills combined with hydrogen could be used to create enough synthetic fuel to power an entire country.
3. Improving Energy Performance
Production efficiency is vital to success in the pulp and paper business, both in terms of profitability and environmental impact. Boilers and the drying process are two energy-intensive areas that are being innovated on, along with the implementation of energy-efficient motors and improved efficiency of steam use through heat recovery.
The International Energy Agency notes that the pursuit of other renewable energy sources, alongside bioenergy and alternative fuels, will be an important part of getting the pulp and paper industry to meet its 2050 targets. In addition, the application of combined heat and power (CHP) has the potential to enhance the industry’s energy efficiency. Another key factor that often leads to reduced production efficiency and end-product quality defects is fouling and scaling in equipment and pipes.