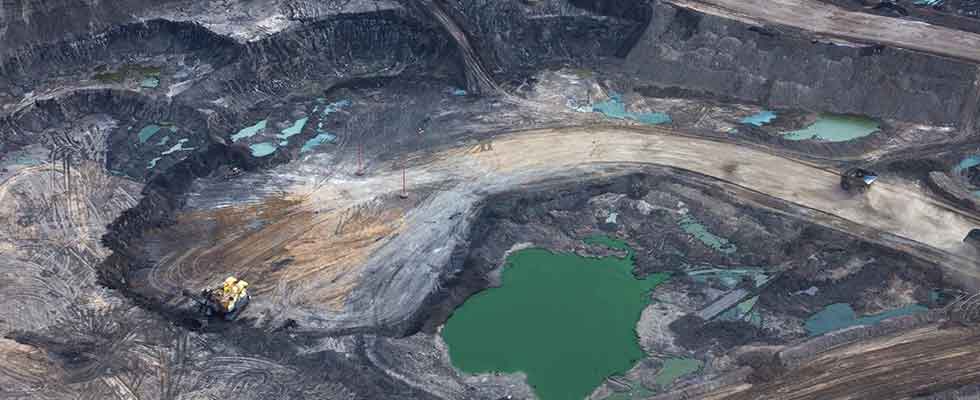
Water management in the mining sector globally is increasingly driven by environmental, social and governance concerns, and the need to adopt responsible practices that ensure water quality and protect the environment. In remote and water stressed regions—where mines are often located—adhering to these requirements presents greater challenges. Miners operating in these environments need solutions to deal with water scarcity, navigate logistical issues and comply with stringent discharge regulations.
Challenges in Arid & Remote Environments
Many of the world’s prominent regions for extractable mineral resources are also the most water stressed. With limited to no direct access to water, operators are forced to be resourceful when it comes to supplying water for mining processes and meeting on-site non-potable demand.
At the same time, miners face complex challenges in managing and treating mining wastewater, including acid mine drainage. Collected and stored in evaporation or retention ponds, these wastewaters typically have high concentrations of salts, heavy metals and sulfuric acid. Treating this wastewater to acceptable levels for discharge requires a well-designed treatment strategy.
In arid locations, storing waste streams on-site in evaporation ponds offers a simple way to help reduce wastewater volume. However, this water is susceptible to water chemistry variations from rainfall or extended dry periods. With conventional treatment processes, these fluctuations can overwhelm or change the pretreatment methodology. Wastewater that is diluted from rainfall can introduce the risk of chemical overfeed and impact the pretreatment functionality. Likewise, prolonged dry spells can lead to greater concentrations of suspended solids that must be removed through pretreatment.
RO Systems With High-Pressure Pumps & Energy Recovery
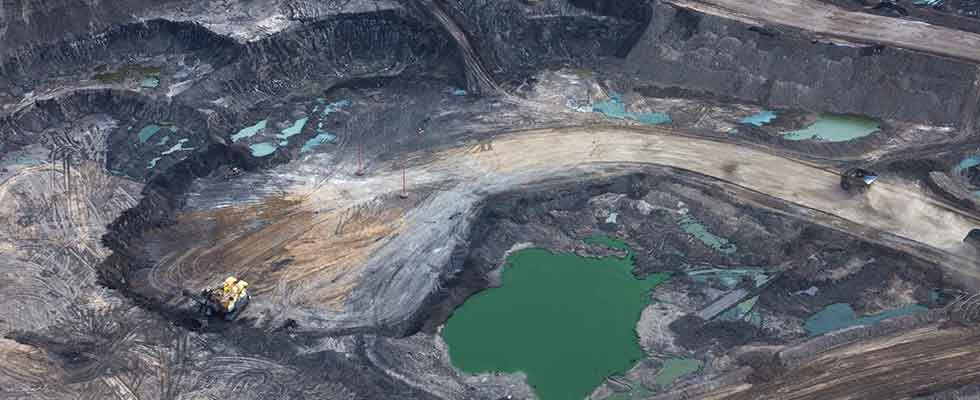
To better deal with tough mining process wastewaters and acid mine drainage, reverse osmosis (RO) offers an alternative to conventional treatment. RO membranes use pressure to force water through a tight polymeric structure that is less permeable to dissolved salts. Salts removed by the membrane are concentrated into a reject stream. In addition to salts, RO offers treatment for removing metals, sulfates and suspended solids that are commonly found in mining waters, producing a consistent, high-quality water that can be reused for several purposes including non-potable applications, helping to reduce the burden of hauling water to the site.
The use of a membrane allows operators to better control the treatment process without the need to worry about varying pretreatment concentrations or chemistries. And, as a nearly chemical-free treatment process, RO will not generate a sludge or a chemical-laden waste product.
Operators who employ RO to treat mining wastewater will be inclined to recover as much water as possible. But in doing so, they run into a critical limitation: the inherent high osmotic pressure of mining wastewaters (a result of high salt and metal concentrations). To overcome this limitation, operators can turn to high-pressure pumps and energy recovery systems that provide the necessary pressure boost to drive water through RO membranes, concentrating salts and metals to the greatest extent possible.
Since RO membrane systems operate at elevated pressure with high salinity applications, the reject stream—although considerably lower in flow volume—is still at a high pressure following the membrane array. Thus, the energy recovery system can be used to transfer that pumping energy from the reject stream back to the high-pressure pump, supplying an additional boost to the feedwater pressure and allowing design engineers to use a smaller high-pressure pump motor.
Using an energy recovery system also lowers the energy requirements for using the RO membrane system (Image 2). Any reduction in energy requirements can be beneficial due to the high cost of electricity often generated on-site.
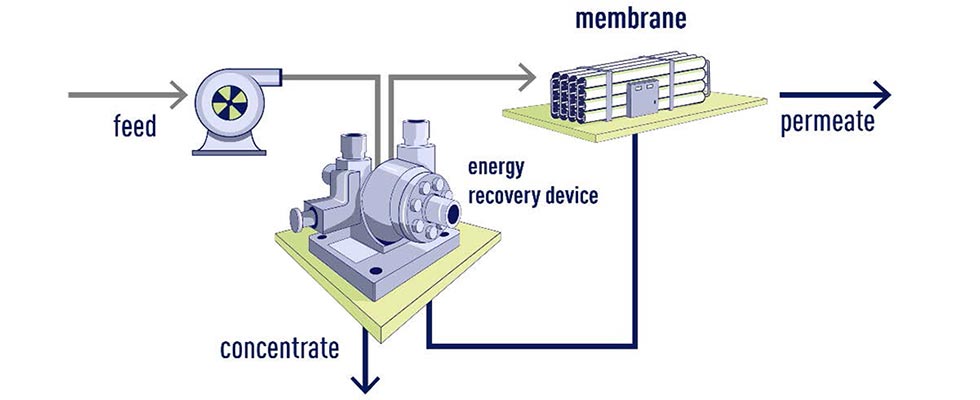
Removing Suspended Solids
With RO system applications, it is critical to focus on the proper pretreatment methodology to protect the membranes.
All RO membrane systems are constructed of membranes and devices that include small flow passages that risk becoming plugged with suspended solids found in the feed stream. Operation at high recovery can increase the concentration of solids and the potential risk of plugging these flow passages. By identifying the size, type and nature of suspended solids in feedwater, the proper pretreatment components can be selected to ensure effective treatment and reduce this risk. Turbidity and silt density index test kits can be used to monitor both incoming water quality and effectiveness of pretreatment operation in reducing the level of solids.
Addressing suspended solids in feedwater is equally important for ensuring that the high-pressure pumps and energy recovery units are also protected. Built with tight tolerances, these systems will often use process water for internal water bearing lubrication and are designed with small flow passages to minimize bypass and achieve high efficiencies.
In the absence of effective particle filtration, suspended solids can act as an abrasive, possibly causing premature wear and tear on the rotating parts, seals and water bearings.
Suspended solids can also plug the flow passages—restricting lubrication and increasing the chance of the pump or energy recovery device prematurely failing. Dissolved salts that tend to precipitate and form suspended solids must also be addressed through scale inhibitor chemicals and periodic flushing to reduce the risk of forming additional particles in the membrane system and associated equipment.
Building an optimal pretreatment strategy requires design engineers to develop an accurate picture of the feedwater chemistry including salt content, heavy metals, pH and temperature range, total suspended solids, and turbidity. This understanding is critical for identifying all parameters that can impact the membrane system, membrane elements, high-pressure pumps and energy recovery units. Once the feedwater quality is adequately characterized, the following technologies can be considered in the pretreatment design.
Sand filters
When combined with chlorine, coagulant and pH adjustment, sand filters offer the benefit of cost-effective suspended solids removal with buffering capacity for widely varying conditions—such as extended dry periods to prolonged raining seasons. Basic sand filter media can be tolerant of tough to treat feed streams and can be easier to recover from process upsets.
Manganese dioxide filters
Pyrolusite, the common name for naturally occurring manganese dioxide, is a natural catalyst for the oxidation of soluble iron and manganese. Mining wastewater can contain these elements, which primarily need to be removed to protect the RO membrane. Heavy applications will require daily backwashing combined with air scouring to fluidize the media and remove precipitated iron and manganese.
Cartridge filtration
Bag and cartridge filters—available in a wide variety of materials—are designed to remove suspended particles to low micron levels. These filters serve as a final protection barrier against any small remaining particles that remain downstream of the media filters. Remote installations are well served to have several stages of bag and cartridge filters in series as a final protection for the membranes, pumps and energy recovery devices.
Hollow fiber ultrafiltration alternative
In some applications, it is necessary to add finer filtration that is often backwashable, such as hollow fiber membranes. The ultrafiltration hollow fiber membrane alternative can be improved with chemicals to achieve a superior level of pretreatment quality.
Minimizing Location-Based Risks
Unexpected component failures resulting from upsets or a shortened life—which tend to be more common with treating difficult mining waters—can be much more problematic in remote regions, leading to longer periods of downtime and potentially impacting profitability.
To mitigate failure risks in difficult-to-access areas, treatment systems should be designed with multiple trains and bypass options. Operators should have adequate spare parts on hand, along with the tools and training to perform simple repairs and rebuilds on-site.
Operators can also adopt remote monitoring and diagnostic tools to improve asset performance management of their water treatment systems. Using data and analytics, these technologies identify flow changes and other problem indicators, allowing operators to resolve critical issues and prevent problems before they occur—increasing asset reliability and life span, and averting unplanned downtime.
In addition to being remote, mines are often located at high elevations. Just as higher altitudes can take a physical toll on people, the same can be true for equipment, including high-pressure pumps.
For this reason, electric pump motors should be oversized when used at high elevation mine sites. This measure will help the equipment adapt to less available dense air for cooling.
Mining operations have many complicated factors that need to be addressed for successful project execution. Fortunately, the advancements in membrane technology and effective pretreatment has provided additional tools to treat wastewater for reuse and/or discharge.