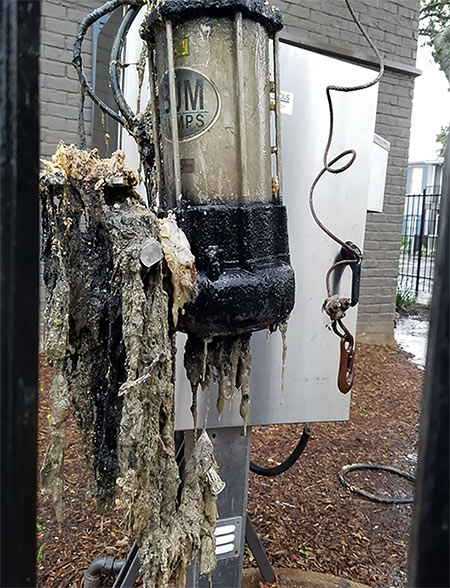
This article explores the role variable frequency drives (VFDs) play in safeguarding pumping systems. It also discusses the mechanisms through which VFDs enhance operational efficiency, prevent mechanical stress and ensure system longevity.
VFDs provide precise control of motors and are also equipped with numerous built-in features that specifically help safeguard pumping systems. These features, and how VFDs effectively manage them to protect pumping systems, are detailed below.
First, VFDs have the ability to utilize multiple ramps to slowly start a pump. Doing so is critical, as it reduces turbidity in drinking water while still starting fast enough to protect the motors, bearings and pumps. Because motors and pumps are typically designed to be at half speed in 1-3 seconds, secondary ramps are utilized to open/close check valves once the pump creates the flow/pressure required to open the valve. One additional reason to ramp the pump up to speed is to reduce or eliminate water hammer, thus reducing leaks, breaks and expensive spills that can risk permits and license compliance, all while extending the life of pipes and pumps.
Another important feature that VFDs employ is built-in motor overload protection. This protects the motor from large or nonpumpable items in the pipes drawing more current, or other overload conditions. By doing so, VFDs help ensure system stability, extending the lifespan of pumps, motors and pipes while reducing downtime and repair costs from pump failures or debris clean-out.
water hammer
VFDs also come equipped with features to initiate pump impeller cleaning. VFDs offer the ability to locally on demand, remotely or automatically clean rags, debris or solids buildup from the impeller by quickly turning it and, when allowed, doing so in a forward/reverse rotation cycle of the impeller to dislodge the buildup (Image 1). By detecting a drop in performance or increase load on the pump, the VFD can be programmed to respond and clean the impeller, reducing the risk of damage to the pump due to lodged debris.
Flow control is an additional feature VFDs have built-in to safeguard pumping systems. Flow control maintains minimum flows to keep solids suspended or pipe flush to clear a pipe of solids. It also can keep flow on the low side to ensure the equipment is not operating outside its minimum speeds for cooling, lubrication and operation for the pump seals. By dynamically changing the pump’s speed to maintain the desired flow, the pump operates more efficiently, reducing mechanical stress and energy usage. It also helps prevent issues such as overpressure and system strain, improving overall system performance.
Cavitation detection is another important built-in VFD feature that protects the pump impeller from the destructive damage created in a cavitation condition. The VFD monitors the motor torque, and when the pump is in cavitation, the torque ripple will alert the VFD to slow down the pump until the ripple stabilizes. Because cavitation can negatively impact pump operation and lifespan, mitigation can increase the pump efficiency and help avoid unplanned maintenance or a costly pump replacement.
Additionally, a VFD’s internal proportional-integral-derivative (PID) controller can maintain most processes with a 4-20 milliAmp (mA) current feedback signal from an external sensor. For example, if the pump is used to maintain pressure, the pressure sensor wires can be connected to the analog input of the VFD.
The VFD can quickly be programmed to operate the pump and maintain the required pressure, reducing the risk of system instability due to fluctuating flow, overpressure or cavitation. This will work for pressure, level, dissolved oxygen, flow and additional parameters.
VFDs also come equipped with the ability to utilize motor moisture protection or motor preheat to maintain a warm winding in the entire motor, reducing damaging water condensation in the motor or in its windings in humid environments or when sitting still with temperature changes. This is done with a standard motor and does not require any special motor components, separate power connection or other hardware, as the VFD already has the power connection to the motor.
Most VFDs also protect the motor from voltage unbalances and fluctuations to the input power. The way a VFD works is by bringing in alternative current (AC) power, then converting it to direct current (DC), cleaning the DC voltage and current up and then inverting it back into a variable frequency and voltage, providing a balanced stable voltage. Across the line, starters and solid state reduced voltage starters (RVSS) cannot protect the motor from these without additional hardware.
Many of these features may already be in the VFDs that are being used today but are not yet “turned on.” Check with the latest VFD programming manual for current VFDs. In some cases, it may be necessary to update the firmware, but sometimes the function may just need to be enabled for these features. And, as always, remember: If the VFD is tripping, it is typically doing its job and protecting the motor.
In addition to the above features, VFDs have enhanced environmental protection for the pump controlling VFD. These include a variety of VFD enclosures and utilization of conformal coating. A variety of VFD enclosures are available that offer higher classes of enclosure for greater VFD protection when installed in outdoor locations (UL Type 3R or UL Type 4X), dirty or dusty indoor locations (UL Type 12) or clean, protected areas (UL Type 1). Another option is an open chassis designed to be mounted inside a protective enclosure.
To extend the life of the printed circuit boards inside the drive, conformal coating—a nonconductive film that covers the full circuit board—is used to protect the boards from corrosion caused by commonly encountered gases, like hydrogen sulfide (H2S), chlorine (Cl), ammonia (NH3) and sulfur dioxide (SO2).
By utilizing a wide array of built-in features and providing precise control of motors, VFDs not only effectively manage but also safeguard pumping systems.
For more on VFDs, visit pumpsandsystems.com/tags/vfd.