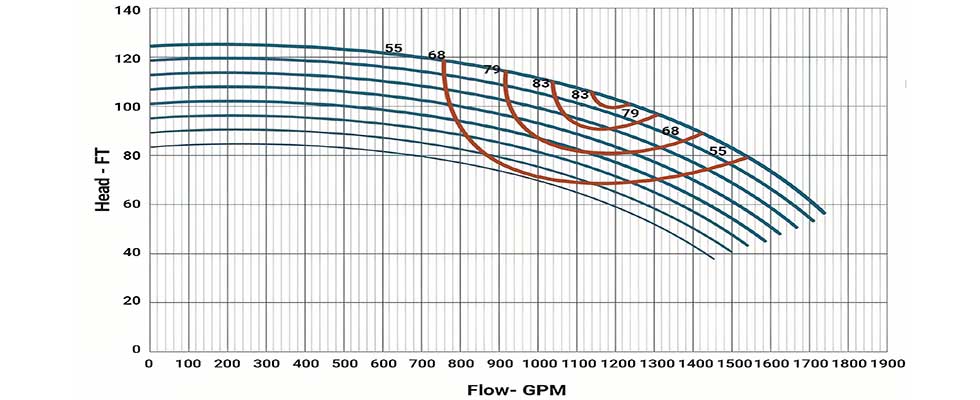
Pump engineers are familiar with the performance curve of a centrifugal pump. For a fixed speed, the head varies with flow and the performance envelope can be clearly defined, although this envelope is often ignored to the detriment of reliability (Image 1).
Engineers intuitively use the mental image of the pump performance curve to evaluate the operating position and the interaction with the system. This has been widely discussed and has become second nature to many. However, reciprocating machines have different characteristics compared to centrifugal pumps.
There is no HQ curve for this type of machine as there is with centrifugal pumps. If we were to draw a capacity curve, it would simply be a straight line from zero capacity and speed to maximum capacity and speed (Image 2). For a fixed rotations per minute (rpm) value, the flow is consistent.
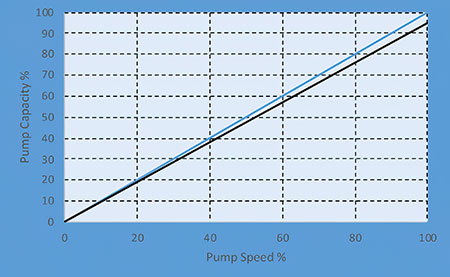
Hydraulic Design of Reciprocating Machines
While centrifugal pump hydraulic engineers spend time and effort understanding impeller blade design and the transfer of energy between rotating and stationary components, the reciprocating pump principles are more straightforward.
Reciprocating pumps function by displacing liquid through a volume—the size of the volume and the number of times per minute the volume is swept. Plus, the number of available volumes means that the reciprocating machine is, in principle, a constant flow machine.
The reciprocating pump engineer has in his or her armory several tools that can get the flow required by the process:
Plunger diameter: One pump can accommodate a range of plunger sizes. Changing the size changes the swept volume. The stroke length is fixed, but the diameter can be tuned to the process need.
Pump speed: Belt and chain drive systems are not uncommon to set the speed to the correct level, and variable frequency drives (VFDs) are also popular. The volume displaced varies directly with the number of revolutions, i.e., increase the number of sweeps of the fixed volume. Image 2 depicts 100% volumetric efficiency, and the other line depicts the pump at the actual application volumetric efficiency. Volumetric efficiency measures how much of the swept liquid passes through to the discharge based on the valve effectiveness. The analogy that can be applied from centrifugal pumps is the volumetric efficiency considered when evaluating the effectiveness of the wear ring landings.
Number of plungers: Plungers can be arranged in parallel in one machine so one complete revolution sweeps all the plungers. Three to five plungers are commonly used.
As can be seen from the variable available, there is not one answer to getting the correct flow. Small plungers at higher speeds will have the same flow as large plungers at slower speeds. Mechanical limitations dictate which is most appropriate and possible.
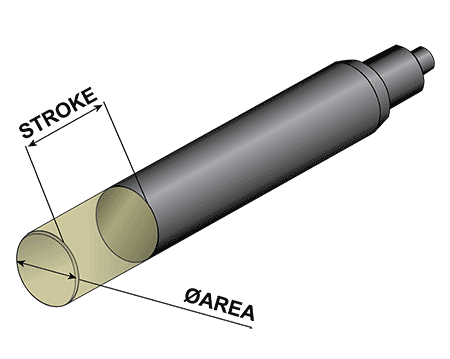
Key Tips for Using Reciprocating Pumps
Reciprocating pumps are well suited to lower flow rates. Certain combinations of flow rate and pressure can make centrifugal pumps inherently less efficient. A reciprocating pump in a high-head, low-flow application could have a high efficiency (90%) compared to the single-digit efficiency of an equivalent centrifugal machine.
Positive displacement reciprocating pump net positive suction head required (NPSHr) varies as a function of flow that is determined by speed. The lower the positive displacement reciprocating pump speed, the lower the NPSHr. The engineer often can run the pump slower to improve the NPSH margin. This is true in centrifugal machines, but there are often compromises on operating condition that can limit reliability.
The operating range constraints of a centrifugal pump do not apply to a reciprocating machine. Using the plunger/speed/number of plungers, the pump can run efficiently and reliably where centrifugal machines struggle.
Because of the fixed volume of fluid displacement, a more precise capacity can be achieved. A positive displacement reciprocating pump has a constant flow regardless of pressure.
Using a reciprocating pump, a different capacity can be achieved by changing the pump speed.
A positive displacement reciprocating pump can be used if the application has variable pressure conditions. A centrifugal pump will be forced up and down the performance curve varying the flow. A positive displacement reciprocating pump can give near-constant flow, making it possible to match the flow rate to the process requirements. A reciprocating pump’s variable capacity can be achieved by changing the pump speed.
A Word of Caution
Misapplication is one of the main causes of poor reliability in reciprocating pumps.Reciprocating pumps should run slowly. Standards from the American Petroleum Institute (API) and Hydraulic Institute (HI) limit the maximum speed of applications. Many are tempted to choose smaller, faster-running pumps that approach or surpass these limits as a less expensive alternative. This causes wear and reliability issues.
Due to the nature of the reciprocating motion of the plungers, the system experiences pressure pulsations on the suction and discharge side. System interactions are stronger. Poor system design drives down reliability, and the system designer must deal with the potential problems caused by pulsations.