The Department of Energy’s pump and motor efficiency rules have directly affected new motors and pumps being manufactured and sold in the U.S. But what about the efficient operation of existing, installed equipment—assets that must function efficiently and reliably as designed for the system? Equipment that is not maintained (not properly lubricated, runs above recommended temperature ranges, or is misaligned or loose) will not operate efficiently. How can maintenance teams ensure that they maintain assets and keep them functioning properly? One solution is the Industrial Internet of Things (IIoT). The term IIoT is everywhere, but—until recently—this technology has not been used to enhance and improve maintenance activities. The IIoT has typically been discussed as a solution for industrial processes and operations rather than for maintenance and reliability.
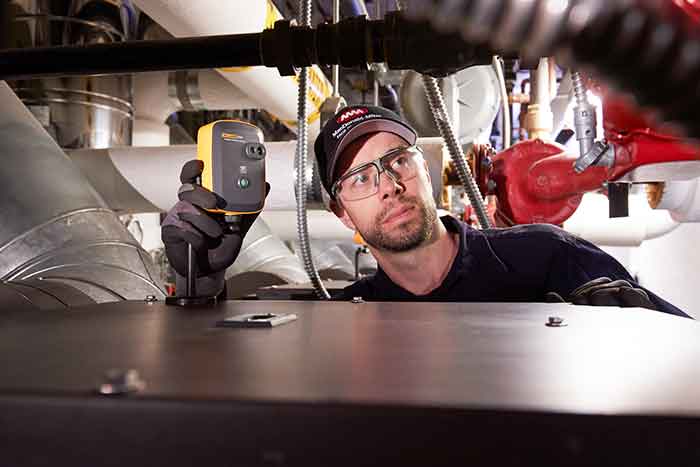
Cloud-Based EAM or CMMS
If end users are not using the IIoT for work management and asset hierarchy setup (or at least considering it), they will be required to move to this method in the future. Maintenance and reliability teams cannot wait for adoption and today, implementation is easier than ever.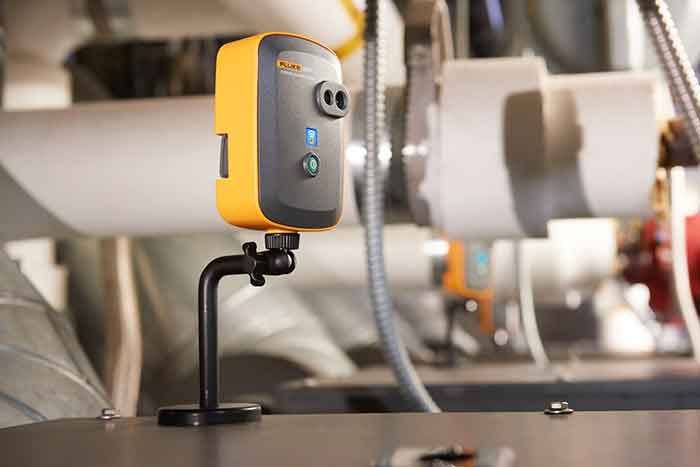
- help maintenance personnel
- gather more accurate and complete failure data
- provide for automated work execution processes
- track maintenance costs to allow for smarter budgeting decisions
- easily plan and schedule work
- designate critical and/or capital spare parts, track warranty information, provide processes
- for equipment refurbishment and restoration
- track and measure important key performance indicators (KPIs) such as machine downtime (or rather uptime), labor performance, wrench time, failure and Pareto data
- ability to place data literally within reach of the technician
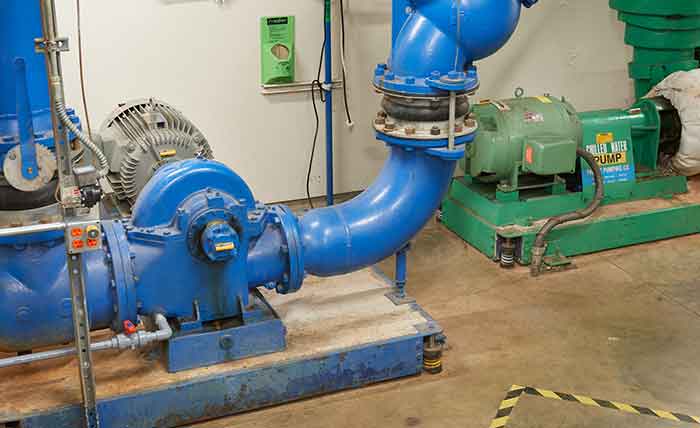
Connected Tools & Sensors
Maintenance systems are not an all or nothing implementation. Pieces and parts of a system may be added to the technology lineup at different times. Some measurements may be gathered on preventive routes with handheld devices. Other measurements can be taken by wireless sensors and still others by tools already installed on the asset. The ability to aggregate lots of data from different measurement devices is instrumental to the often small steps that many maintenance teams must take as they begin their own reliability journey. The addition of wireless sensors can be a first step from preventive maintenance to predictive or condition-based strategies by taking measurements that are sent to the cloud. Two types that can provide early warning of imminent problems are thermal imaging and vibration sensors.Thermal Imaging Sensors
Infrared imaging allows personnel to view high-level temperature data on an asset. No matter the industry or facility, faster response time to sudden mishaps avoids catastrophic failure and curtails damage costs. With thermal monitoring sensors, maintenance personnel can check for hot and cold spots more regularly, averting downtime and other problems that could be created by delay. Temperature thresholds can also be determined and parameters set up in the cloud-based software to send an alert to any connected device if thresholds are exceeded. Some common problems that can be helped with the use of thermal monitoring are:- Automated data collection: Many maintenance managers in mid-sized facilities with smaller teams find performing regular equipment check-ups with a thermal imager difficult, so they often outsource this function to consultants. This tool is so simple to use that team members can begin taking routine thermal images without third-party intervention. Managers can replace some thermal inspection route-based maintenance with automated sequential images.
- Reactive mindset: Because many facilities house seemingly countless assets from rotating equipment to small transformers, chasing problems as they surface strains even the most capable maintenance teams.
- Poor response time: If personnel is spread thin and professionals are constantly hustling to handle the latest equipment failure, response time can suffer.
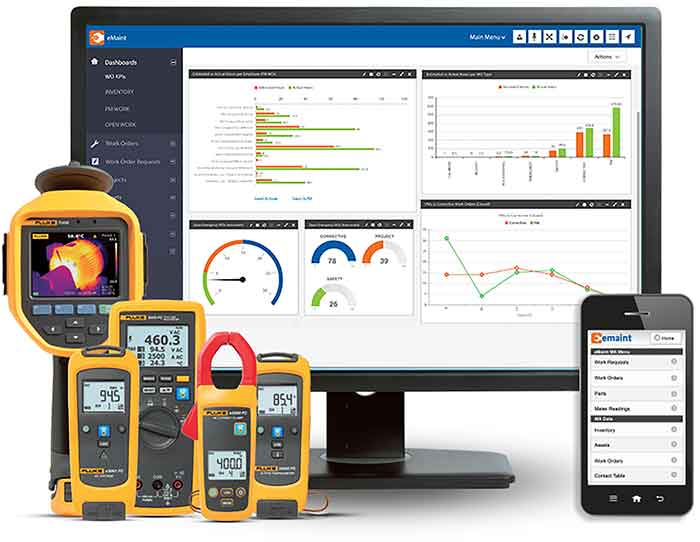
Vibration Screening
Vibration screening can provide early warning of many problems with rotating equipment including pumps, compressors, turbines, motors, fans and blowers. These faults may include misalignment, imbalance, looseness and bearing failure. Some abilities of vibration sensors are:- Reduce downtime. Avoid unexpected downtime and associated expense of repairs or replacement.
- Predict equipment failure. Notice vibration abnormalities sooner, and fix problems at an earlier stage.
- Make data-driven decisions. Collect historical equipment data and capture recurring wear patterns to anticipate trends.
- Minimize costs. A cost-effective solution for capturing all measurement-related data in a single system.
- Avoid hiring vibration specialists. The vibration sensor is easy to install on virtually any machine and runs on battery power with a three-year life span.
- Access hard-to-reach monitoring points. Screen vibrations from hard-to-access measuring points of critical equipment.