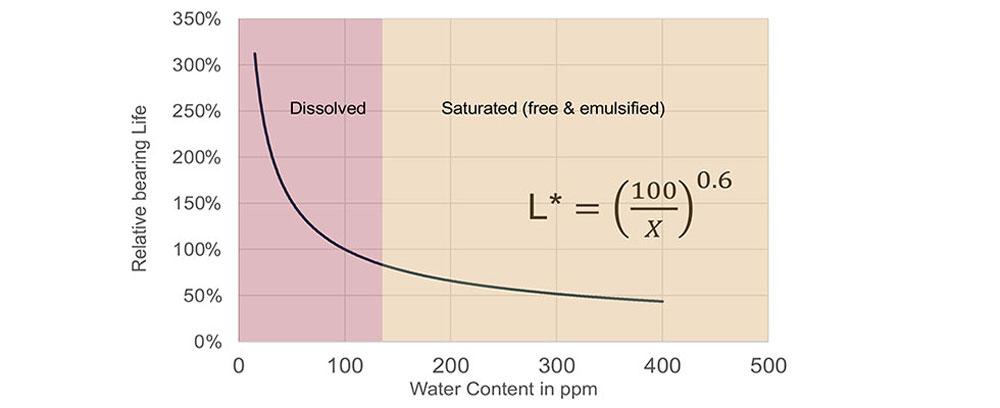
In industries that rely on process pumps, water in the form of free water, steam or airborne humidity is a pervasive contaminant. Water not only leads to rust and corrosion but can also lead to a reduction in oil film strength, resulting in overall poor lubrication conditions that can reduce the life expectancy of bearings by as much as 50%. As such, maintaining a low level of moisture and humidity in bearing housings is critical to overall pump life.
Why Is Water So Impactful?
Most pumps use rolling element bearings. In an element bearing, the separation of the bearing raceway from the rotating elements occurs due to elastohydrodynamic lubrication (EHL). Under EHL conditions, the oil trapped between the moving elements and raceway is subjected to extremely high, localized pressures, often in the range of hundreds of thousands of pounds per square inch (psi). Under these pressures, the oil will exhibit a rapid increase in viscosity due to the oil’s pressure-viscosity coefficient. This viscosity increase causes the mating bearing surfaces to elastically deform. As a result, this distributes the load across a wider surface area. If any water is present in the load zone, it will impact the elastohydrodynamic oil film and, under some circumstances, can cause flash vaporization of the water.
Water & Oil Do Mix
While conventional wisdom says that polar fluids like water do not mix with nonpolar fluids such as oil, in pump oils and other lubricants, oil and water can mix under certain conditions. When water and oil mix, the water can exist in three distinct phases: dissolved, emulsified and free. Dissolved water refers to water that is dispersed at the molecular levels throughout the oil. All oils will hold a certain amount of water in the dissolved phase. Even though there is water in the oil, an oil with dissolved moisture will appear clear and bright. The amount of dissolved water depends on the type of oil, the temperature and the condition of the fluid.
Most pump oils at operating temperatures will hold between 100 to 150 parts per million (ppm) (0.01% to 0.015% volume per volume [v/v]). Once this concentration is exceeded, the oil is said to be saturated with moisture and additional water will be present as either free water, sitting on the bottom of the bearing housing or emulsified, causing the oil to appear milky or hazy. While all forms of moisture are harmful to bearings, free and emulsified water are the most damaging.
Image 1 shows the results of an empirical study of bearing life as a function of water-in-oil concentration1 for a standard mineral-based International Standards Organization Viscosity Grade (ISO VG) 68 rust and oxidation (R&O) inhibited pump fluid. Based on this curve, which arbitrarily set a water-in-oil concentration of 100 ppm as a baseline for 100% bearing life, one can see that once water concentrations exceed the saturation point of the oil, bearing life can be significantly reduced. In fact, at only 300 ppm, equivalent to just 3 milliliters (ml) in a 10-liter (L) oil sump, bearing life expectancy is cut in half.
The effects on water and other contaminants on pump life are well known and primary reasons why bearing isolators have become standard on many American National Standards Institute (ANSI) and American Petroleum Institute (API) pumps. Modern bearing isolators that are designed to provide both dynamic and static sealing have proven effective at increasing pump life. However, studies have shown that using bearing isolators does not completely negate the impact of water on pump life.
The reason for this is due to the way that water and humid air interact—an effect that can be explained by Henry’s Law. Henry’s Law states that at a constant temperature, the amount of a given gas (water vapor) that dissolves in each type and volume of liquid (oil) is directly proportional to the partial pressure of that gas in equilibrium with that liquid. Put another way, if the air above an oil has a relative humidity of 60%, the oil will also be 60% saturated, meaning a water concentration of 60 to 100 ppm. Image 2 shows how the humidity of air affects the water concentration in the same ISO VG 68 R&O fluid. The inference in Image 2 is clear: Exposing pump oil to higher levels of ambient humidity will result in higher water-in-oil concentrations, effectively lowering bearing life expectancy.
To study the influence of ambient humidity on pump headspace humidity levels, two pumps were fitted with desiccant breathers equipped with smart humidity sensors. One breather was sealed and the silica gel desiccating media removed to serve as a reference, while the second breather was installed in the bearing fill port, allowing the silica gel to dehumidify the headspace. Both pump bearing housings were equipped with a leading brand of bearing isolator. The test was conducted in Central Florida in the summer with average ambient humidity of 74% relative humidity and daytime temperatures around 93 F (34 C).
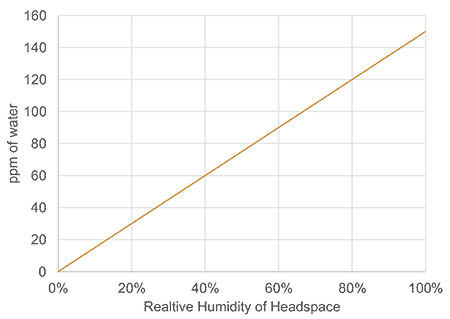
The results of the study are shown in Image 3. As shown, the pump with no headspace protection shows high levels of humidity in the headspace, varying from 50% to 65% relative humidity. Interestingly, humidity levels were shown to fluctuate across a 24-hour period, reflecting the impact of daytime/nighttime temperature fluctuations on pump headspace humidity. By contrast, the pump with silica gel protection showed a low level of humidity, despite identical conditions to the reference pump. Based on this data, the pump oil saturation graph shown in Image 2 and the relative bearing life projections shown in Image 1, it is reasonable to conclude that the pump without headspace humidity protections might be expected to have as much as a 20% to 40% reduction in bearing life.
Which Pumps Are Most Affected?
The impact of headspace humidity on pump life is perhaps most pronounced when pumps operate intermittently. Since relative humidity is temperature dependent, pumps that operate in stop/start mode or are shut down for long periods of time are often found to be completely saturated with moisture, meaning the bearings are sitting idle in oil contaminated with free or emulsified water. This is prevalent in process industries such as petrochemical or refining where it is common to have both duty and standby pumps. Under these circumstances, controlling headspace humidity should be considered a priority to prevent unexpected failures during pump startup.
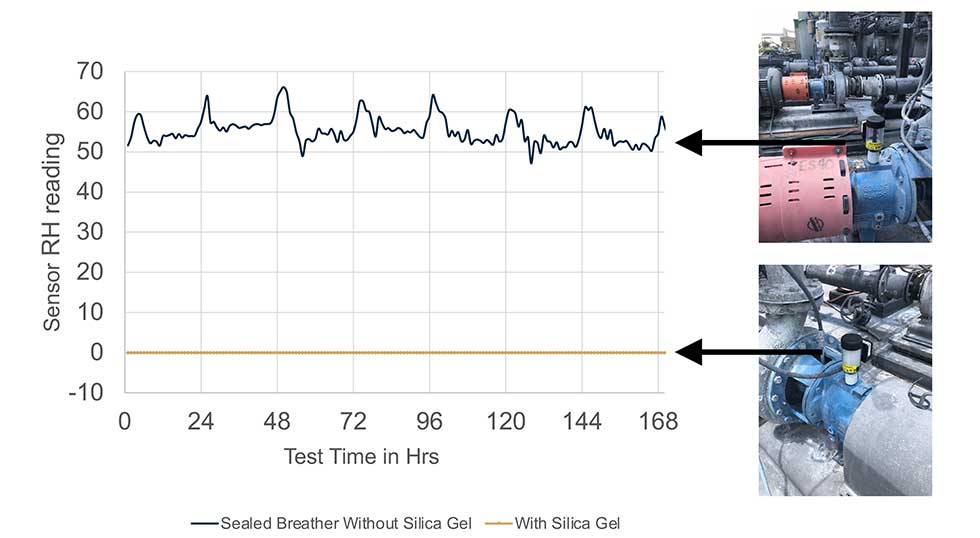
headspace humidity
How Can Headspace Humidity Be Controlled?
Controlling headspace humidity is a three-step process.
- New oil should be prefiltered to remove both particles and moisture and stored in resealable containers when not in use.
- Installing bearing isolators is a strategy to exclude particles and gross moisture during normal operation and shutdown.
- Using a desiccant breather that has silica gel in contact with the pump headspace will help to reduce headspace humidity and, in doing so, increase bearing life.
References
R. E. Cantley ASLE Transactions Vol. 20. 3. 244-248, 1977