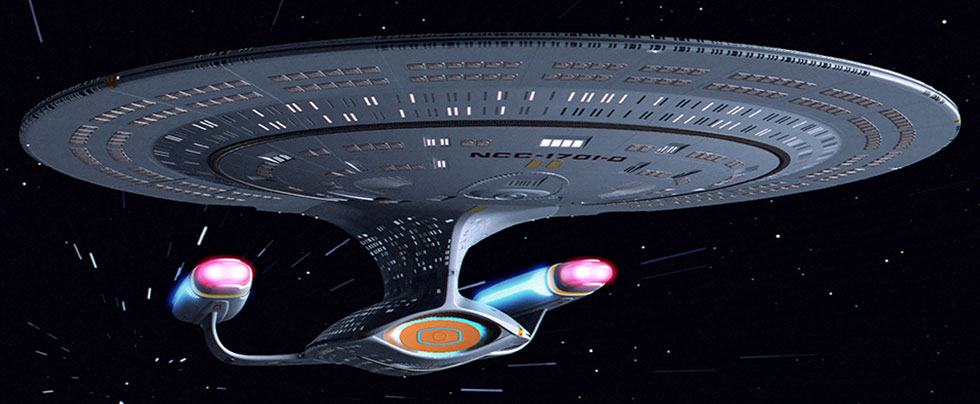
The first time I heard the term “critical speed” was in a college mechanics class. I initially assumed it had something to do with the Starship Enterprise or the safe speed range that exists above the posted speed limit but is lower than state trooper ticket speed. I was wrong on both counts.
If you operate high-energy equipment in a power plant or refinery, you are aware of critical speed because of the many multistage pumps and other high-energy equipment such as turbines and compressors.
For the everyday pump operator or technician, you don’t need to worry about critical speed because someone else has already figured it out. However, I recommend that you at least be aware of the term and have a fundamental understanding of the concept. The purpose of this column is to initiate discussion of the critical speed concept on a general level and explain why it is important for safe and reliable equipment operation. If you don’t know the critical speed of your pump, ask the manufacturer.
Critical Speed
Any structure made from an elastic material has a natural resonance frequency. In our example, the structure is a pump rotor. The fact that metal is elastic may be hard to understand at first, and while it takes some noticeable amount of force, metal will deflect, bend and vibrate. If you still have issues thinking of metal as an elastic material, refresh your materials science background with a fast review of Young’s modulus of elasticity and remember that most metal choices for pump shafts share a small range of elastic modulus around 29x106 pounds per square inch (psi).
Critical speed is the speed where the natural vibration (resonance) occurs. Resonance is when the unit has high vibration from a disproportionate (small) stimulus. From a different perspective, an example you may remember is old TV commercials or other visceral instances using voice or instrumental resonance to shatter a wine glass.
Rotor Dynamics
All rotating equipment has a critical speed (fans, blowers, generators, motors, turbines, expanders and compressors). For this column, we will focus only on centrifugal pumps. For the average single-stage pump, the critical speed will be much higher than the operating speed, and so it is of little to no concern. For example, with few exceptions, American National Standards Institute (ANSI) (OH-1) pumps in the S, M and L frame sizes have a first critical speed over 10,000 rotations per minute (rpm), which is well above any allowable operating speed. In lieu of critical speed on OH-1 pumps, it would be more important to pay attention to a related parameter, the pump shaft rigidity factor also known as “L-over-D ratio,” or more accurately the L3/D4 ratio. L-over-D ratio is derived from the beam deflection formula utilized in statics and is a parameter that will aid in the prediction of magnitude for shaft deflection for a given and applied hydraulic radial force.
Of course, shaft deflection in a pump is not a desired reaction because it leads to failure of the mechanical seal, bearings and shafts. When considering the L-over-D ratio, it is important to understand that a lower ratio is better. L-over-D ratios are of little to no concern when dealing with multistage pumps.
Critical speed is the natural vibration level of the rotating element due to its structure and imperfections. At some speeds (rpm), the rotor will start to exhibit a pronounced vibration due to the natural resonance. For example, imagine a system startup where you are bringing a large pump up to speed on a variable speed drive (VSD) or a turbine. In our example, the pump would run smoothly as we proceeded from 0 to 2,000 rpm, but it would then vibrate profusely somewhere near 2,050 rpm (critical speed). When we continue to increase the speed above 2,050 rpm, the vibration would dissipate. Please note the speeds mentioned here are only for example purposes.
Again, realize that it is that angular velocity (think speed) that excites the natural frequency of the rotor. Critical speed can also be considered as that rotational speed where the dynamic forces cause the rotor to vibrate at its natural frequency. The natural frequency of a pump is a function of the rotor stiffness (k) and its mass (m). One method to express this natural frequency is seen in Equation 1. Critical speed (expressed in radians per second) is equal to the square root of the stiffness divided by the mass.
Bump/Impact Testing
All rotors have a natural frequency that you can determine by conducting a test that is known as the “bump method” (aka “impact test” or “bump testing”). It is not my intent to delve into the details of these methods. You can find plenty of information from various companies that specialize in vibration monitoring/analysis and/or the Vibration Institute (vi-institute.org).
The short explanation is if you bump (strike) a structure or rotor with an instrument, it will resonate at its natural frequency. You will need proper instruments to detect and measure the vibration levels and corresponding frequency. The measurement is typically conducted in a minimum of two planes/directions. The test is normally conducted on idle units, but some instrument systems will allow you to conduct the test while the unit is operating, which is a major benefit. The design of some pump units and systems will also allow for the test to be conducted during coast down.
Striking the unit could potentially cause damage, so be careful where you hit the unit. Use soft face hammers or blocks of wood. Most of the time, you don’t need to bump the unit very hard. Many detection systems include a calibrated strike hammer.
Critical Speed Will Vary
No pump rotor is perfectly manufactured—there is always some imbalance or minute imperfection, especially if castings are involved and those flaws become magnified over multiple stages. It is important to note that the “rotor imperfection” can also be due to hydraulic radial force deflection from operating the pump away from the preferred operating range. The deflection due to rotor eccentricity can exceed the elastic restoration limits of the rotor at certain speeds, which will cause the rotor to vibrate as if it was unbalanced.
Critical speed will vary with fluid properties, pump wear (ring fits), shaft length, shaft diameter, bearing types/placement and coupling type.
Critical Speed—There Is More Than One
Critical speed episodes occur more than once for a given rotor. Normally we are only concerned about the first critical speed and its relation and margin to the operating speed. Second and third critical speeds are almost always far above operating speeds.
Speed, RPM & Angular Velocity
Critical speed is a phenomenon that all rotating equipment shares. It is a speed normally expressed in rpm at which the unit will exhibit the highest level of vibration due to the inherent natural frequency of the rotating element. Another way to express rpm would be angular velocity, which is simply the speed of the unit but because it is traveling in a circle (hopefully) rather than a straight line.
To be technically correct, rotational speed is normally expressed in units of rpm while angular velocity is expressed in radians per second (or other units of time). We could also express that velocity as degrees per second (or other units of time).
Lomakin Effect
Critical speed for a pump is difficult to calculate because of the many factors involved. One main reason is that pump shafts have many different diameters over their length. Another major factor is impellers with close ring fits where the liquid is “caught” in the clearance and acts like a dampening bearing (aka Lomakin effect), and so the dampening effect works to mitigate the critical speed vibration by stiffening the rotor. The Lomakin effect has a strong influence on critical speed and the higher the effect, the higher the critical speed will be.
The Lomakin dampening effect can also be created by packing, bushings and other close clearance components. Note that as the pump operates over time, and the clearance opens up due to wear, the dampening effect diminishes and critical speed will decrease.
This decrease in critical speed due to wear is an excellent reason not to ignore maintenance on high-energy multistage pumps. While not likely, it is possible to lower the critical speed into the operating range of the unit and cause severe damage. Large blowers, turbines and compressors do not benefit from this Lomakin dampening effect because the air/gases in the close clearances are compressible.
Stiff Rotor vs. Flexible Rotor & Static vs. Dynamic
A rotor with its first critical speed above the operating speed is referred to as a “stiff rotor.” Stiff rotor does not mean little to no radial deflection (during operation) and/or rotor sag when the pump is static/idle.
Caution: I have witnessed operators make costly mistakes because they believed that a stiff rotor meant the rotor did not sag and, consequently, the impeller rings would not be touching the casing rings when the pump was at idle and in a static condition. Because of the sag on multistage rotors at rest, you should never rotate them without liquid in the pump (do not rotate even by hand). Without liquid in the pump, the rings will gall.
For details about this subject of pump shafts—rigid and flexible—I recommend a technical paper from the 10th Pump Users Symposium by Ulrich Bolleter and Arno Frei.
Notes & Comments
Operating at critical speed is something to avoid by a wide margin due to the potential for damage caused by the amplification of excessive vibration. The pump is more sensitive to any residual imbalance at critical speed.
Critical speed phenomena occur at the natural frequency of the rotor, also referred to as the intrinsic frequency and sometimes the excitation speed.
The critical speed of a rotor is the same whether it is vertical or horizontal.
Critical speed calculation is fairly straightforward for gas/air turbines, compressors, fans and blower units, but is much more difficult for units that involve liquids.
Critical speed calculations for air and gas units are normally correct within a few percent.
Large multistage pumps incorporate long shafts simply to accommodate the required number of impellers. The pump designer could design the shaft with a larger diameter to preclude the rotor from sagging when the pump is at rest. However, with larger diameter shafts, the eye area of the impeller is reduced. Reduction of the impeller eye area increases the net positive suction head required (NPSHr) for the pump and it also reduces the pump efficiency.
If your pump still utilizes oil rings for lubrication (older designs), know that the oil rings normally rotate at a speed close to 50% of the rotor speed. On multistage pumps, it is common for the first critical speed to be below the operating speed. It is then possible for the ring and/or the oil velocity in the fluid film bearing to be at the critical speed of the rotor. This condition is, of course, undesirable and will cause the rotor to vibrate excessively. Also note that the rotor critical speed and the lubricating oil velocity can occur in bearings without oil rings. This phenomenon is known as whirling or oil whirl instability.
Critical speed can be calculated and subsequently expressed as either wet or dry. Dry speed is also referred to as air speed. Normally if there is no added description for a pump’s critical speed you can assume it is the wet critical speed. For pump applications, I suggest that you disregard critical speed calculations based on dry values as you can be assured the presence of liquid will change the value and you will not be operating the pump in a dry condition. Some engineers will calculate the dry value as a point of interest and curiosity. Dry speed calculations may be appropriate for some disaster scenario calculations conducted for nuclear and military applications.
If the pump speed is variable either by electric VSD engine or turbine, be aware and cautious of the units’ first critical speed and take steps to avoid this speed zone.
The calculated critical speed of a pump can change simply by placement into the piping system. The system will change both the mass and the stiffness values of the unit. Another reason to evaluate piping and foundation designs with the pump as a total system.
The first critical speed for the Starship Enterprise NCC 1701-D is well above warp 9.9, which is approximately 4 billion miles per hour or 21.5 times the speed of light. The sweet spot for avoiding speeding tickets remains elusive.
References
ASME paper 82-GT-277 by S. Gopalakrishnan et. al. 1982
Velocity vs. Speed
Some people erroneously interchange the terms of velocity and speed. We are all guilty of this in some casual conversations. Velocity is the rate of change in position over some period in some direction (vector). Linear velocity is simply in a straight line, while angular velocity relates to the speed of rotation. The difference between speed and velocity is that velocity has a defined direction. Speed is a scalar while velocity is a vector. For example, you can state that your yacht is traveling at 30 knots, which is the speed, but if you state the yacht is traveling at 30 knots on a southerly course at 180 degrees, that is velocity.