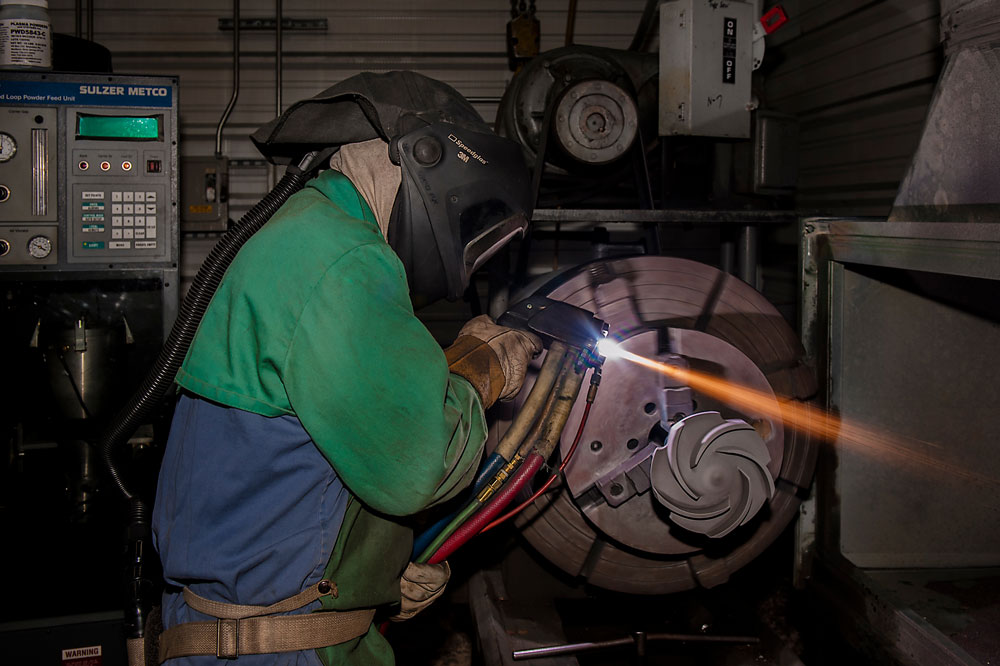
Advancements in industrial coatings over the last several years have made an impact on both operational life and efficiencies in new and repaired pumps. It is now possible to apply a coating of a dissimilar metal over an existing metal base (think 316 stainless steel over a standard pump shaft) with a bond strength that can exceed 9,000 pounds per square inch (psi).
This is being accomplished using the twin arc thermal spray process. This process allows any metal to be sprayed on any existing metal, and the variety of metals that can be applied using this method can often create a surface hardness that far exceeds the original metal surface and/or increase the component’s corrosion resistance properties, thereby extending the product’s functional life.
This process is not the same as the old “metalizing” process. Wear rings that have been worn due to use can now be “sprayed” with new bronze material that is the same composition and hardness as the original bronze or upgraded to a harder material and then machined back to tolerance. The process is faster and, in most cases, less expensive than having to machine new wear rings out of stock material.
Cast-iron cases are highly vulnerable to wear in water and wastewater applications when exposed to chemicals used in the process. However, they can now be sprayed with a high-performance metal that will not react to the chemical, extending the functional life of the product.
Specific areas of a shaft that constantly wear due to a lip seal cutting into the shaft can be repaired using this method, and the area that is coated will be harder than the lip seal, preventing damage in the future. Worn metal surfaces can be restored to their original dimensions with a surface hardness that is usually double the original base metal hardness.
The twin arc thermal spray process was developed by the United States military and has been in use for many years. In fact, parts that need to be repaired on commercial airliners are repaired using this method, as it extends the part’s life due to exceptional abrasive and corrosive resistant properties without adding weight to the part. It is not commonly used in the pump repair industry.
Case Study
The twin arc thermal spray method can be enhanced with the addition of industrial epoxy coatings that help to reduce wear and increase and maintain the pump’s efficiency. This concept was proven at a large, 60 million gallon per day (mgd) metropolitan water treatment facility in the northeastern U.S. in 2005. It coated multiple pumps using a specific industrial epoxy coating after sandblasting the interiors—but left other pumps sandblasted clean but “raw”—and noted that the pumps that were coated stayed in service longer and their efficiencies after repair lasted years longer than the untreated pumps.
The water municipality was surprised to learn that the pumps that were sandblasted and left uncoated began to decline in efficiency within several months after being returned to service, whereas the pumps that were sandblasted and coated lost less than 1% efficiency after several years of service. The pumps that were included in the study were field tested and studied for any loss of performance at 30, 60 and 90 days and once again at six months and then every six months for the following five years.
After nine years had passed, the water municipality decided to follow up on how well the coatings were holding up in the pumps. They found that after nine years of near-continuous use, the industrial ceramic coatings were still intact and functional.
The water municipality that conducted the study calculated an energy savings of $17,000 in one year on one pump: a 300-horsepower (hp), 6,000 gallons per minute (gpm) pump with 150 feet of head that was first installed in 2000 and rebuilt during the 2005 study using the industrial ceramic coating. The pump’s original efficiency had slipped from the original manufacturer’s design of 88% in 2000 to 77.8% in five years.
When the pump was refurbished in 2005, the efficiency was brought back up to 88%. The pump in the study ran over 90% of the time since being repaired. These savings were realized in 2005 at the utility’s kilowatt-hour (kWh) rates at that time.
Most often, when a water/wastewater pump is repaired, the internal parts are cleaned by sandblasting the various components down to bare metal and returned to service in that condition or, at minimum, given a spray can paint job, which is typically gone in less than a week after the pump is put back in use. Many professionals in the water/wastewater industry would not think of installing unlined ductile iron piping for use in a municipal water distribution system. Yet only a few professionals have considered that these same pipes are often feeding pumps in their facilities that are manufactured out of raw ductile iron. Left uncoated, the pumps are susceptible to the same corrosion and tuberculation the pipes would normally be subjected to, causing a drop in performance and efficiency as was proven in the study discussed above.
Users should consider that a pump’s interior and components should be coated for the same reason the industry coats ductile iron pipe for use in water and wastewater applications. Water intake screens can be coated to prevent the buildup of zebra mussels.
Many companies are looking for ways to keep existing pumping equipment in operation without having to purchase new pumps that may not be made as well as the “old iron” they currently have installed in their plants, while others are looking for ways to make their pumps last longer. Both options can now be realized using the twin arc thermal spray method and applying industrial epoxy coatings.
These methods can be used with new and repaired pumps to meet the end goal of making pumps last longer and run more efficiently. One key factor is to find a repair facility that is certified by the coating’s manufacturer to ensure proper application of the manufacturer’s coating product. If the coating is not applied in the proper manner, it can malfunction and will not produce the expected performance.