Teaching Moments
Pumps & Systems
01/17/2018
Companies all over the pump industry—from OEMS to end users—are facing challenges finding skilled employees to replace the talented experts approaching retirement.
“As these older generations retire out of the workforce, we face a huge skills gap, with an estimated 2.7 million jobs likely to be needed as a result of retirements in the existing workforce,” said Doug Keith, Large Drives Business Unit lead, Siemens Process Industries & Drives Division, U.S. And having workers who are up to the challenge of filling these jobs is not always a guarantee. Formal apprenticeships and on-the-job training are largely a thing of the past. Even though those programs may be how most pump experts today learned their craft, new workers rarely go through the same process. “We have a big chunk [of engineers] with many, many years of experience. Then there’s a low number of those with five to 10 years of experience. Then we have a lot of new engineers,” said Adrian Conrad, manager of engineeringU at John Crane. Manufacturers are using a few tactics to address this skills gap. For example, John Crane created engineeringU, a development program for new engineering graduates at the company. Participants spend 12 months learning about the company’s business and gaining hands-on experience with more seasoned engineers in varying departments. At the end of the program, they move into a permanent role with the company.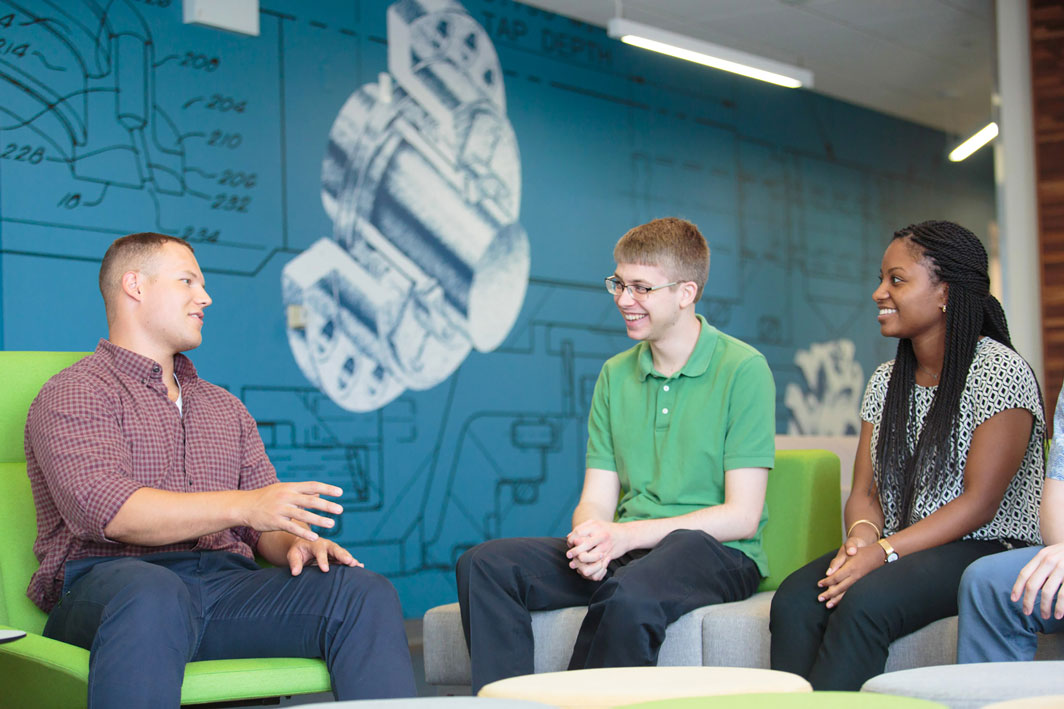