The rating means they were tested under 3 feet of water for 30 minutes and continued to run properly.
Walchem, an Iwaki America Company
01/20/2017
Choosing the correct metering pump involves many considerations. Among them are accuracy, repeatability, chemical output, material compatibility, line pressure, control input, off-gassing of the chemical and the environment where the pump will be placed. Even for pumps that meet the requirements for a particular application, the environment in which the pump operates can pose a significant challenge. Metering pumps often are used in wet conditions and require daily washdowns of the equipment.
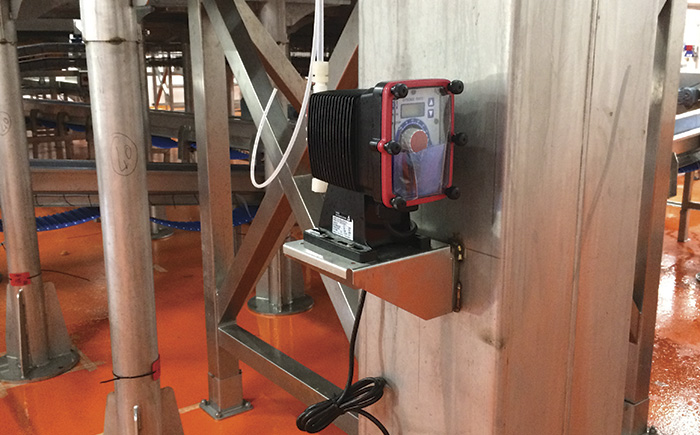
Water Intrusion
Manufacturing a food or beverage—as well as maintaining a hygienic work area during the process—requires copious amounts of water. Washing down the equipment requires either raw water or water containing chemicals such as oxidants. The inundation of water during the washdown process frequently causes pump failure because of water intrusion into the electrical drive or control. Repairing these pumps is time-consuming and requires a replacement pump to keep the line producing. If the pump is replaced, the new equipment also faces the risk of failure because it operates in the same environmental conditions. In some cases, end users replace these pumps with a waterproof version that can handle the washdown procedures. There are pumps available with a rating of Ingress Protection (IP) 67 (NEMA 6 equivalent), which means they were tested under 3 feet of water for 30 minutes and continued to run properly. For example, one manufacturer’s line of these types of metering pumps have been used extensively in the produce disinfection market where washdowns, condensation from low temperatures and perpetually wet surfaces exist. In this specific example, these pumps also can be used in many environments and processes where water intrusion, flooding or washdowns occur.IP 67 Pump Benefits
Chemical metering pumps are the workhorse in produce applications because all produce must be disinfected to remove or kill disease-causing pathogens. The process typically requires an oxidizing disinfectant such as chlorine, chlorine dioxide or peracetic acid to be pumped into the water that comes into contact with the produce. The residual oxidant must be maintained during the process for the required contact time to ensure that the microorganisms are killed and cannot reproduce. This usually requires an accurate, reliable and waterproof chemical metering pump in conjunction with a controller and an appropriate chemical sensor. The produce disinfection process places pressure on chemical pumps because of the constantly wet environment. Several tools and accessories can protect these pumps, but they often pose their own challenges. Pump covers, for example, can make the pump difficult to access for adjustment or servicing. Pump boxes also make pump adjustments difficult, and they can contain heat, which may cause a heat overload or failure.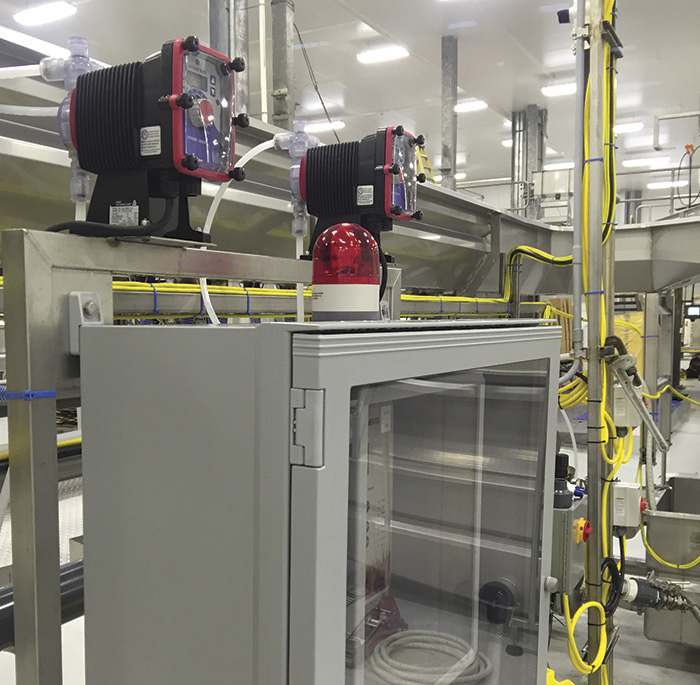