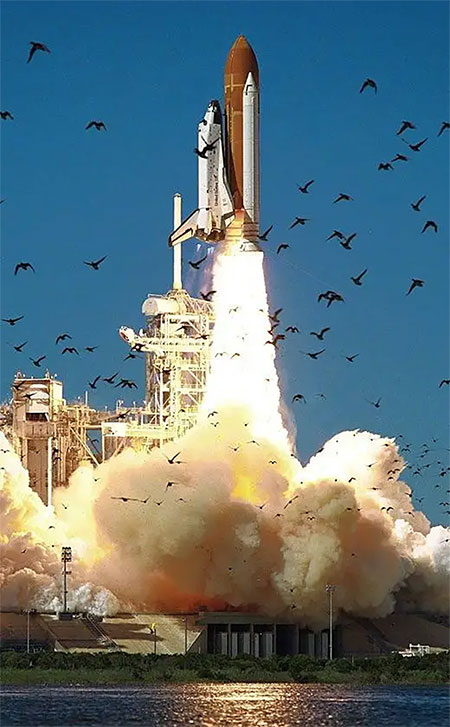
Part 1 of this article ran in the February 2024 issue of Pumps & Systems.
The Importance of Valve Packing Loading Precision
Excessive gland load on valve packing bolts gives rise to three primary issues:
Bending of glands
Stress on the bolts can cause the gland to bend and distort, compromising its perpendicular alignment to the stuffing box. This distortion impedes the gland follower’s free movement into the stuffing box, resulting in load loss and failure.
Bent stems
Excess gland forces increase packing friction, rendering the handwheel ineffective in operating the valve. The use of cheater bars to enhance force may exert loads so strong they exceed the yield strength of the stem, causing it to bend. A bent stem introduces serious valve operability issues and leakage.
Seat leakage
Applying a cheater bar on the handwheel can often exert more force on the seat to close the valve than initially calculated by design engineers. This added force can exceed the limits of the seat material, resulting in cracks and internal leakage.
In the 1980s, the Electric Power Research Institute (EPRI) undertook the formidable task of reducing unscheduled maintenance in nuclear power plants. A significant issue flagged was a high percentage of lost power generation due to leaking valves. EPRI, through meticulous research, underscored the critical role of correct packing loading in ensuring longer packing service life. They discovered that relying solely on the “skill of the craft” method resulted in a substantial scatter in loading accuracy.
A pivotal change following the landmark EPRI report was the adoption of a torque wrench as the correct way to apply gland load. Torqued valves became the norm and were integrated into packing procedures, training manuals and textbooks. While torque brought about an industry shift, it also brought its own set of challenges. Studies revealed the accuracy of applying load using a torque wrench hovered around a modest 30%. These studies often utilized bolts in good condition and adhered to ideal bolting practices, conditions not always mirrored in real-world situations. The absence of these practices led to false positives in torque wrench readings, resulting in inaccurate load application. Bolt condition emerged as another critical factor, necessitating the replacement of studs during field repacking to ensure proper loading. Simple issues like a bent thread on a new or old bolt could create an illusion of tightness without any load being applied to the gland.
Valve packing, functioning as a wearing part in a valve, undergoes volume reduction over time through the repeated actuation of opening and closing. This reduction in shape prompts the gland to move into the stuffing box to compensate for the loss. Stretched by a small distance, the bolts loosen, lowering the gland force on the packing.
This phenomenon occurs with every valve actuation, and the loss of load remains concealed. An innovation sparked by the EPRI report was the adoption of Belville springs sets, which were introduced to the bolting on a valve to enable live loading. This technology, involving more travel in the joint, sought to reduce the loss of load over time compared to valves without springs, extending their service life.
However, live loading technologies, including Belville springs, grapple with the challenge of not addressing precise gland loads. The inherent inaccuracy of torque still contributes to premature packing failure, even with the implementation of live loading. Another seldom discussed yet well-known issue in bolting circles pertains to reapplying a torque value in the field, introducing drastic errors. Dried anti-seize lacks the same K factor as when applied in a wet state, resulting in a wide and unpredictable scatter in torque readings. Despite the illusion of reenergizing a valve, reapplying the same torque value while in service often results in a 50% reduction in load.
A modern technology that has revolutionized the landscape of correct packing loading is a cartridge live loading. This innovative approach utilizes Belville springs but in an outer cup design, cut to a precise height based on calculated
gland load. This design ensures accurate packing load application when the flat washer on top of the springs aligns with
the cup.
This simple yet effective design marks the next generation of accurate valve loading, moving away from reliance on torque wrenches and embracing spring compression. In addition to providing spring travel and extending the duration of bolt load loss, this technology offers a visual aid of actual valve loading while in service.
A plant manager walking through their plant with their team once pondered, “When is this valve going to fail and cause me a headache?” With cartridge live loading technology, valves can be routinely checked for correct assembly loading before any signs of leakage emerge. A simple box wrench can be employed to reload the valve to the correct load, bypassing the need for torque measurements.
While spring assemblies, like all live loading technologies, must be sized according to valve dimensions (stem diameter, stuffing box OD, stud diameter and clearances), they also factor in the valve’s operating conditions, including system pressure and temperature.
In embracing cartridge live loading, plant maintenance teams now possess a consistent and reliable method to ensure accurate packing loads, resulting in fewer failures and extended reliability. This technological advancement symbolizes our commitment to learning from past challenges, adapting and evolving to create a safer, more reliable future in the intricate realm of industrial operations.
We invite your suggestions for article topics as well as questions on sealing issues so we can better respond to the needs of the industry. Please direct your suggestions and questions to sealingsensequestions@fluidsealing.com.