Last year, a Pumps & Systems reader asked about matching variable frequency drives (VFDs) and motors. “I have a spare pump in my warehouse that requires 15 horsepower (HP) at best efficiency point (BEP) flow when running at 1,760 rpm. I also have a new application with a duty point that can be matched perfectly by this pump at about 1,466 rpm. This speed is about 83 percent of full speed and equates to 50 hertz (Hz) when operated by a VFD. The affinity laws indicate that the power required at 50 Hz is reduced to just 8.7 HP. I have a limited budget and would like to keep my total cost for the motor and VFD as low as possible. Is it OK to use a 10-HP motor as long as I make sure the VFD will never exceed 50 Hz?” I was on the road conducting training sessions, so I sent my short answer—“No, it is not OK to run this motor on a VFD, so you may want to consider running it via a belt drive instead.” He never questioned my reason, but he thought the belt drive alternative made good financial sense. I received an email later letting me know that his new belt drive system was up and running. Why was a 10-HP motor not OK? Many ways are available to ensure that a VFD will not exceed a maximum preset speed. The reader’s plan was flawed from the beginning, and the problem was not with limiting the maximum speed. Centrifugal pumps follow the affinity laws. When the speed of an electric motor changes due to a change in frequency, other rules dictate the motor’s performance. The HP produced by an induction motor is directly proportional to its torque and rotational speed (HP = (torque x rpm) / 5,250). If the number of stator poles remains constant, the rotational speed of that motor is directly proportional to the frequency of the input power. When the frequency changes so does the speed, but the torque remains constant. For torque to remain constant, HP must change. Therefore, if the incoming power frequency is reduced from 60 Hz to 50 Hz (5/6), the HP will be reduced to 5/6 of its original value. If this is applied to the 10-HP motor in the example above, its output at 50 Hz would be just 8.3 HP. Even though the power required by the pump was reduced to about 57 percent (8.7 HP) of its original 60 Hz value, it is still more than the 10-HP motor can supply at 50 Hz. U.S.-made motors for 60-Hz operation must be de-rated for use overseas on 50-Hz power. The standard de-rating factor for 230-, 460- and 575-volt models is 5/6 (0.83) of the 60-Hz power. Most manufacturers use 0.85 for open drip proof (ODP) motors and 0.80 for totally enclosed fan-cooled (TEFC) motors, assuming a service factor of 1 and line voltages of 190, 380 and 475 volts. If line voltages are higher, the de-rating factor is reduced proportionally. Application of the proper line voltage at reduced frequencies is important. A motor designed for 460-volt, 60-Hz operation has a volts/hertz (V/Hz) ratio of 7.66. If the same voltage is used at 50 Hz, the ratio increases to 9.2. To accommodate this increase, the motor magnet’s circuit size must increase. Because this is impossible, the existing circuit will saturate, causing an increase in current draw and a corresponding increase in winding temperature. Winding temperature plays a major role in insulation life. For 50-Hz operation, line voltage is reduced to 380 volts and keeps the V/Hz ratio at 7.66. A constant V/Hz ratio is always maintained when a motor is under VFD control. When frequency is changed, the line voltage is automatically compensated via pulse width modulation (PWM). If voltage is 460 volts at 60 Hz, it is reduced to 230 volts at 30 Hz.
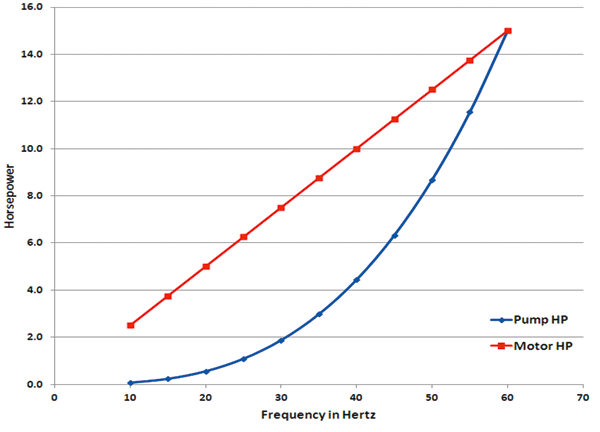
