Poor water quality can be a factor in degrading pump reliability and MTBR.
Hydro
03/04/2019
A major steel plant on the East Coast had been experiencing catastrophic failures with their five- stage descaling pumps for more than four years. The plant operated using three multistage axially split (BB3) pumps with two spares. All five of the pumps had a mean time between repair (MTBR) of two years. The plant water quality was considered to be less than ideal, and the entrained abrasives were a factor contributing to the repeated failures.
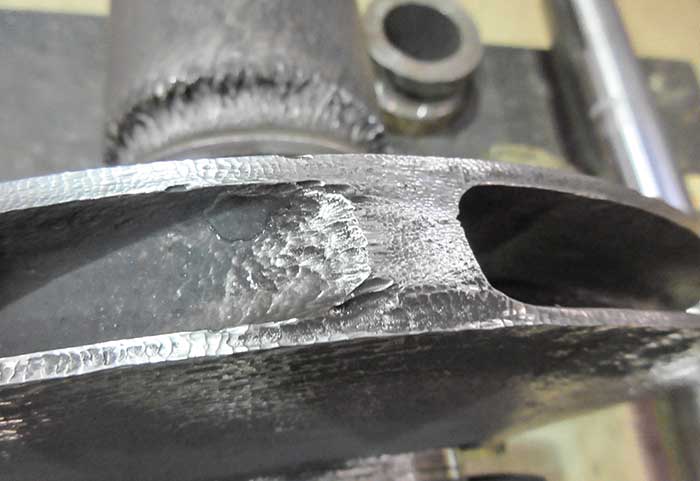
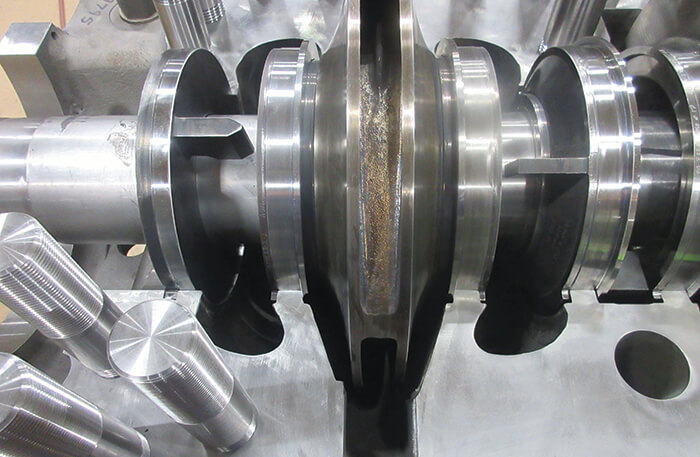
The Challenges & Issues
Poor water quality can lead to a number of pump reliability issues. When pumping fluids with abrasive material, pumps experience erosion and corrosion, and the effects can rapidly degrade both the casings and critical inner elements. While erosion and corrosion alone are not always a difficult problem to solve, it is important to have a firm understanding of the relationship between various types of erosion and corrosion and the metallurgy used in designing the pumps. An analysis provided results that showcased excessive clearances and inconsistencies with component fits that also contributed to pump performance degradation outside the abrasion.Analysis & Action
The pump casings and rotating components were completely cleaned, inspected and digitally mapped using current laser scanning technology. The hydraulic design engineers then analyzed the impeller and volute geometry. The team recommended manufacturing new impellers, which would increase pump performance while providing higher efficiency and greater hydraulic stability.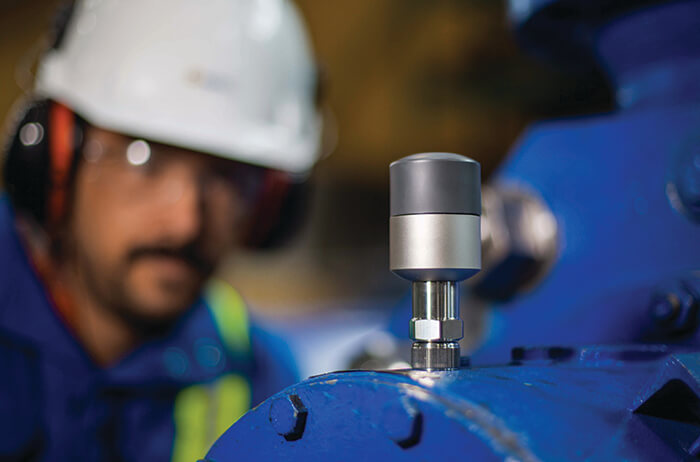
Impact & Results
In order to increase the MTBR of the pumps at the plant, the aftermarket pump service provider also recommended several engineered upgrades including new impellers, which were manufactured using advanced mold technology. This produces components that specifically address surface finish and dimensional consistency. The splitter on the bushings was also upgraded to provide a better interstage water flow, reducing internal hydraulic turbulence and the vibration levels of the pump. With the aftermarket engineers on the project, the client was provided with a field service team to install and remove all of the pumps. A wireless condition monitoring system to support the plant’s pumps was also established. Two pumps were actively in service, monitored by 10 magnetic wireless sensors measuring vibrations up to 20,000 hertz (Hz) with automated alerts and predictive reporting protocols.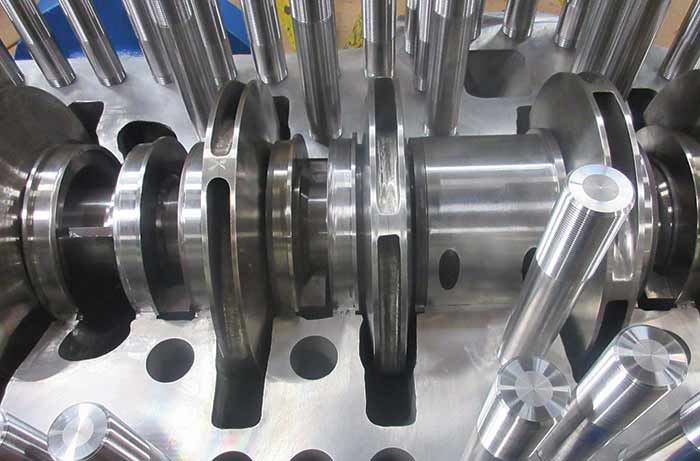
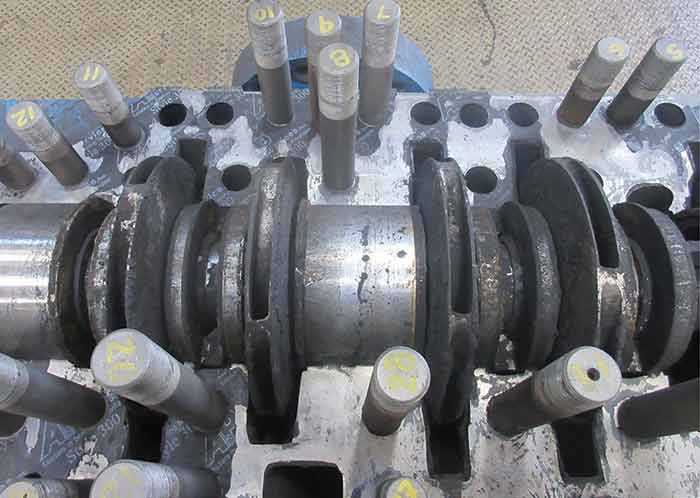