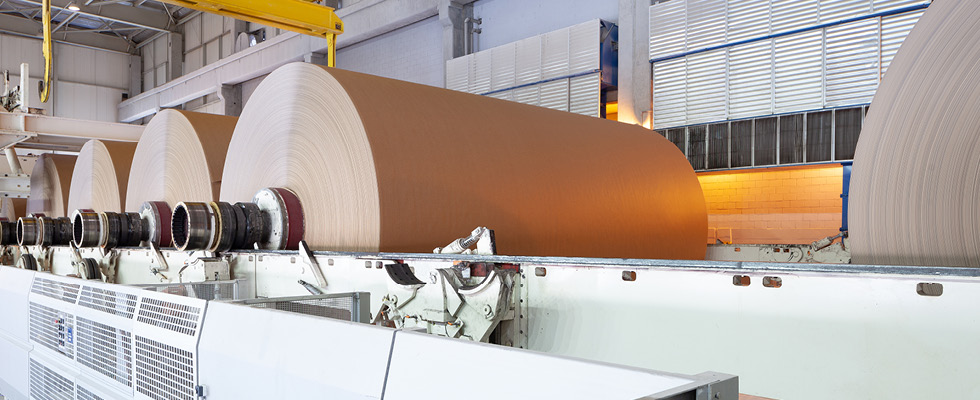
Over the last decade, the paper industry has made measurable sustainability strides. According to International Energy Agency (IEA) estimates, the industry’s emissions intensity has declined by nearly 3% per year1 on average. Meanwhile, global industry leaders such as International Paper are tracking progress against ambitious goals not just for emissions reduction but also reduced water consumption. Yet, as net zero deadlines draw near and global water scarcity intensifies2, the industry’s rate of progress must accelerate.
To realize its Net Zero by 2050 Scenario3, the IEA estimates that paper industry emissions intensity must decrease by about 5% year-over-year through 2030—nearly double its current pace. Water evaporation contributes significantly to a paper operation’s energy consumption, making it a key focus for many emerging emissions reduction technologies.
Among these initiatives, the IEA highlights the significant potential of enabling water removal without evaporation, utilizing waste heat sources from production processes and, even more ambitious, achieving a fully closed water loop in paper production. As these innovations bring decarbonization closer to reality, pulp and paper organizations are also addressing the water consumption challenge. Key levers for progress include the adoption of innovative water-saving technologies, as well as strategies that optimize existing asset reliability to reduce water wastage.
Robust, continued technology investments will be critical to accelerating the pulp and paper industry’s sustainability progress. However, numerous market-ready innovations are already helping operations curb water consumption and emissions today—including advanced mechanical sealing technologies that perform reliably in some of the world’s most complex pulp and paper operations.
In the coming years, the paper industry is expected to experience a modest 1% year-over-year growth4 due to rising demand for packaging and sanitary paper products. But the industry is also under pressure to do more with less, creating a dynamic in which organizations must meet increased demand while reducing costs, accelerating decarbonization and reducing water consumption. Mechanical sealing technologies can help paper organizations achieve all four objectives.
The Role of Mechanical Seals in Driving Sustainability Progress
In 2022, the pulp and paper industry was responsible for slightly less than 2%5 of all emissions from industry, with decarbonization gaining steam but still lagging behind IEA benchmarks. An equally mission-critical challenge for pulp and paper operations is water conservation.
Water is used in nearly every paper production process, including moving slurries and paper stock, generating steam for heat transfer in cooking, dehydrating pulp byproducts and creating products from waste. By some estimates, processing 360 truckloads of logs requires 35 Olympic-sized swimming pools worth of water, and enough water to fill 30 pools typically ends up at a wastewater treatment facility. These water-driven processes increase energy consumption and, depending on the fuel type, can contribute to carbon emissions.
Often, the regions in which pulp and paper mills operate are underincreased pressure to reduce water use and wastewater disposal. Combined with tightening environmental legislation and corporate sustainability mandates, this makes the industry’s water conservation efforts more critical than ever.
More than a century old, packing technology has long been used in heavy-duty centrifugal process pumps that move liquids to support manufacturing. Mills built 30 to 40 years ago typically feature equipment designed for packing. However, after decades of being the preferred choice for OEMs and operators, packing is now increasingly being replaced with mechanical sealing technologies, especially in the most demanding pulp and paper applications.
By switching to mechanical seals, paper mills can significantly curb water consumption, avoid the power loss and friction heat associated with compression packing, increase reliability and eliminate the need for weekly maintenance trips to tighten packing.
Leveraging Seal Face Technologies for Enhanced Reliability & Sustainability
Every day, pulp and paper mills use mechanical sealing technologies to enhance efficiency, maximize reliability and do
more with less. Within this class of solutions, seal face technologies have gained the spotlight for improving liquid sealing reliability and sustainability.
Mechanical seals feature two flat faces that run against one another. Between the two faces, there is a narrow gap. Pulp and paper process media—whether it be sand, viscous fluids or solid particles from solidified black liquor—can create deposits within the gap that damage the seal. Meanwhile, poor lubrication can cause friction within the gap, leading to overheating and seal failure. Borrowing from gas seal designs, seal face technologies pump a minimum amount of barrier liquid along the gap until it reaches the product side. This clean, optimized barrier between the two faces can deliver numerous operational and environmental benefits, such as:
- Optimized pump reliability and seal life
- Extended mean time between repair (MTBR) and equipment life spans, which reduces maintenance costs
- Fewer equipment failures, resulting in less production loss and enhanced operational efficiency
- Reduced power consumption and friction for improved energy efficiency
- Zero emissions, with no process fluid leaking into the atmosphere
- A significant reduction in water consumption by virtually eliminating cooling and flush water requirements in
many applications
Seal face technologies are proven to perform reliably in even the most challenging pulp and paper operating conditions, including those caused by low lubricity, high heat, caustics and/or liquors, viscous fluids and dry running.
Mechanical sealing technologies can help operators achieve environmental and operational goals, particularly when compared with solutions of the past.
References
- iea.org/energy-system/industry/paper
- unicef.org/wash/water-scarcity
- iea.org/reports/global-energy-and-climate-model/net-zero-emissions-by-2050-scenario-nze
- fortunebusinessinsights.com/pulp-and-paper-market-103447
- iea.org/reports/tracking-clean-energy-progress-2023