First in a Series on how mechanical seals work
Mechanical seals touch nearly every aspect of industrialized society. Wherever a rotating shaft moves fluid, mechanical seals play a key role in sealing process fluids in, keeping contaminants out, or both.
A few basic components and principles in mechanical seal design contribute to a working seal at the interface of the rotating shaft and stationary pump/mixer/seal-chamber housing. Mechanical seals are usually end-face seals or rotating-face seals, but in some designs they can be circumferential or even a hybrid of lip-type seals. In either case, the following components are common to all mechanical seals:
- Rotating primary sealing element: fixed to/driven by the shaft and seals against the stationary primary sealing element
- Stationary primary sealing element: fixed to the stationary housing of the pump, mixer or other equipment through which the rotating shaft passes and seals against the rotating primary sealing element
- Closing force: biases the primary sealing elements in contact to initiate sealing
- Static and/or dynamic secondary seals: seal between the mechanical seal components and the equipment shaft and housing
Rotating & Stationary Primary Sealing Elements
The more common end- or rotating-face mechanical seal designs feature mating faces as the primary sealing elements. Rings of ceramic, carbide, carbon or composites of these materials are lapped flat in the range of less than 1 micron on an axial end face. These lapped faces run against each other, one rotating with the shaft and the other stationary with the equipment housing.
The sealed fluid migrates between the flat faces and forms a stable fluid film at this interface. During shaft rotation, the face materials heat up, wear and degrade quickly without a lubricating fluid film between them. The sealed fluid creates this thin lubricating film.
In a lip-seal-type mechanical seal, a thin film of sealed fluid also lubricates the sealing interface. Rather than two flat rings, the sealing interface is a polymer material deflected against a hard material. This material could be a hardened, coated or plated metal, ceramic, or carbide face or sleeve. One of these elements rotates with the shaft while the other is stationary with the equipment housing.
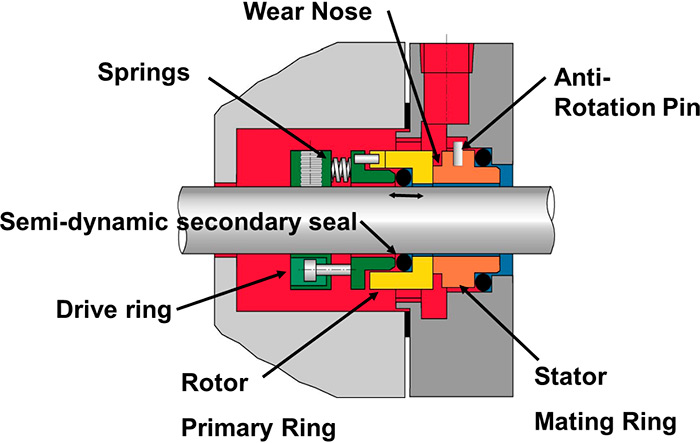
Closing Forces
Leakage is a function of the mathematical cube of the film thickness, so to minimize leakage, the gap at the sealing interface must be kept at a functional minimum. Closing forces are used to optimize this design parameter throughout the operating range of the mechanical seal.
The initial closing force ensures that the seal will function properly from startup. In end- or rotating-face mechanical seal designs, the initial closing force is provided by a spring component, which can be a single coil spring, multiple coil springs, a deflected bellows unit (elastomer or metal), or formed or flat springs. Initial biasing forces also can be created by magnets, compressed elastomers or any other means of applying a closing force between sealing elements. In a lip-type mechanical seal, the initial closing force is typically from the deflected polymer of the lip-type seal or a garter spring for less resilient materials.
Static/Dynamic Secondary Seals
The sealing elements must be secured to the rotating shaft and stationary housing of the equipment being sealed. O-rings, gaskets and other elastomer seals stop leakage at these interfaces.
A static secondary seal stops leakage between components that do not move relative to each other. One example is the interface between a sleeve and a shaft, where both rotate but do not move relative to each other. A dynamic secondary seal, on the other hand, stops leakage between components that move relative to each other. An example is a spring-mounted seal face, where the face is free to move as the spring deflection allows, and the secondary seal will stop leakage between the seal face and the component to which it is resiliently mounted.
A lip-type mechanical seal may only require static secondary seals because the deflection of the lip-type seal accommodates equipment operating motion. All effective end- or rotary-face mechanical seals require at least one dynamic secondary seal. This is because the mating faces of the sealing interface are rigid materials that cannot comply with any equipment shaft/housing misalignments, thermal growth and shaft end-play. The dynamic secondary seal will accommodate the relative motion between at least one of the seal faces and the component to which it is mounted.
Factors that increase seal life include seal design and material selection, process and environmental controls, and equipment optimization.
Mechanical seals are used with many process fluids. Each fluid has different lubrication qualities, but a thin, lubricating film at the sealing interface is always needed. A film that is too thick will increase leakage and may allow particulate between the faces, which will increase wear from abrasion. A film that is too thin will generate heat and cause materials to degrade. Keeping the sealing interface cool and clean will promote longer seal life.
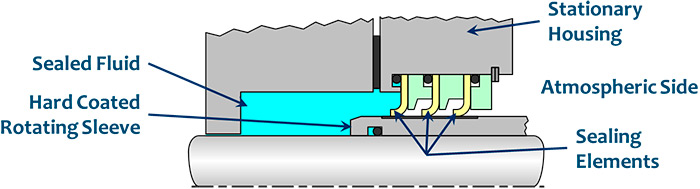
Design & Material Selection
Seal design can influence film thickness by balancing the closing forces on the sealing interface in such a way that the sealing interface does not become overloaded as process pressures increase. A closing force that is too high will lead to a fluid film at the sealing interface that is too thin, generating detrimental heat.
Another way to influence film thickness is to design surface features at the sealing interface that promote hydrodynamic lift between the rotary and stationary sealing elements. This can help create a purposeful separation at the sealing interface that results in a thicker fluid film that provides cooling and decreases face wear.
Primary seal material selection can influence seal life as well. Chemical or process compatibility is just one consideration. Harder materials are more resistant to abrasive processes, but if both sealing elements are hard materials, the wear characteristics may be less desirable in a nonabrasive application.
Using one sealing element made of a softer material and/or one that contains lubricating components such as graphite decreases friction for starting and incidental contact. The use of composite hard faces will also reduce friction by providing microscopic reservoirs of system fluid at the interface.
Thermal conductivity of materials will dissipate heat away from the sealing interface, promoting seal life. Material toughness also can play a dominant role in mechanical seal life. The inherent material surface texture may also play a role in promoting desirable film thickness.
Note that many seal failures result from failed secondary seals that have exceeded chemical compatibility, pressure or temperature limits. Metal parts must be compatible to avoid corrosion, and springs and other hardware must hold up in service.
Process & Environmental Controls
Process and seal environmental controls greatly contribute to a cool, clean lubricating film at the sealing interface. If the process fluid is a slurry mixture, process pressure will drive the particulate-laden fluid into the sealing interface, resulting in abrasion and accelerated wear.
Environmental controls, such as a restriction bushing and clean flush, can isolate the mechanical seal from the harsh process so the seal is mostly sealing the cleaner, cooler flush fluid. In other cases, the pump product may crystallize, abrading the sealing interface and causing premature wear. Product crystallization can be prevented by using temperature controls, quenching the atmospheric side of the sealing interface, or using a double seal with a buffer or barrier fluid.
There are many process considerations other than abrasion that might prevent a cool, clean lubricating film at the sealing interface. If the sealing fluid has a low vapor point, for example, flashing can result. Flashing occurs when the sealed fluid changes from liquid to gas at the sealing interface, expanding quickly and forcing the sealing elements apart until the pressure and temperature are relieved, only to have the sealing elements collapse back into contact. Mechanical damage to the sealing contact surfaces quickly results in seal failure. No lubricating film is established. Operators must incorporate process controls and ensure proper mechanical seal selection to prevent such upsets. There are many other process conditions that require special attention such as fluids that harden, are toxic, must be kept anaerobic, are part of food or water supply, or present another specific constraint.
Seal environmental controls are often overlooked, resulting in surprisingly short seal life. Many seal failures of this type happen in cool water applications. Cool water is an effective sealing fluid for creating a stable lubricating film at the sealing interface, but failure to apply proper seal environmental controls can lead to seal failure.
Many cool water applications fail prematurely because they are vertical, with the seal installed at a high point in the system where air is trapped. Without properly venting the air out of the seal chamber area, the mechanical seal seals air, not cool water. This is a dry-running condition that generates heat and quickly degrades the materials at the sealing interface.
A common environmental control used in vertical applications is a recirculation line from the seal chamber to pump suction, but in some cases the seals run dry for too long before the fluid replaces the air in the seal chamber.
Equipment Optimization
Poor equipment conditions—caused by bad bearings, cavitation, excessive impeller loads and misaligned shafts—result in excessive motion, vibration and mechanical shock to the mechanical seal. These conditions cause greater stresses, more heat and more opportunity for abrasives to enter the sealing interface.
Mechanical seals are designed to handle a range of motions and conditions, but they are just one machinery component in a larger system. Understanding the basics of mechanical seals and how they may be adapted for different application requirements is critical for choosing the best seal for the job and ensuring optimal system reliability.
Next Month: Back to Basics: Compression Packing (Find other articles in this series here.)
We invite your suggestions for article topics as well as questions on sealing issues so we can better respond to the needs of the industry. Please direct your suggestions and questions to sealingsensequestions@fluidsealing.com.
See other Sealing Sense articles here.