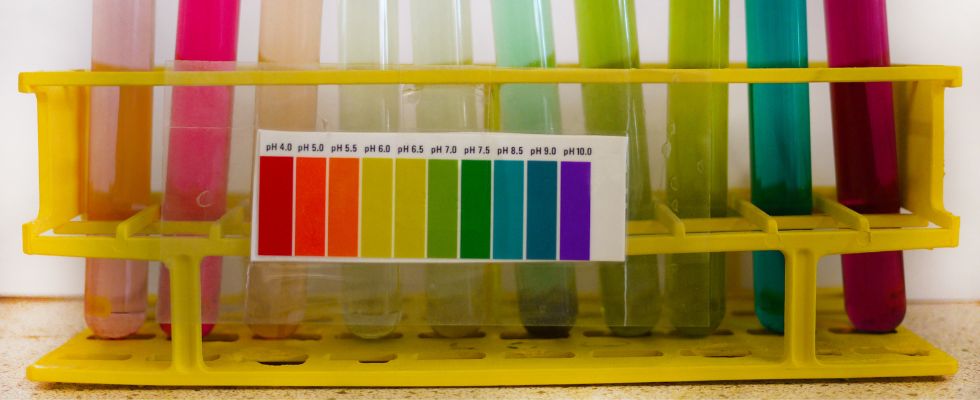
Since the dawn of humanity, humans have tried to understand the world through observation and experimentation, and alchemists were no exception. Centuries before the foundation of Alexandria, Egyptian craftsmen made objects of precious metals, such as gold and silver, and were also capable of giving items the appearance of having a golden surface. Examples of their great skills are the objects found in the tomb of Tutankhamun.
The exact date alchemy was born is unknown, but it seems likely it was before the contact between the Greeks and Egyptians centuries ago. Though there is no suggestion that the Egyptian metallurgists claimed they converted metals into gold, the basis for alchemists had been set, and their aim would be to transmute metals like copper or lead into gold.
Many fields of science have seen important advances since those days, yet for the sealing industry, knowledge of material properties and operating conditions is just as crucial for an effective and reliable seal. Because of this, the pH of a substance is of great importance, since it indicates whether or not a sealing material could be suitable to be in contact with a fluid.
pH, or the potential of hydrogen ions, serves as a fundamental metric in chemistry, influencing various industrial processes, including sealing applications. Understanding pH and its implications is crucial for ensuring the effectiveness and longevity of sealing systems in diverse industrial environments. pH is defined as the negative of the logarithm of hydrogen ions. Its scale ranges from 0 to 14 and quantifies the acidity or alkalinity of a solution. A pH of 7 represents neutrality, as seen in distilled water. Values below 7 indicate acidity, with lower numbers indicating higher acidity, while values above 7 denote alkalinity, with higher numbers indicating greater alkalinity. This scale provides a simple yet powerful tool for assessing the chemical properties of fluids encountered in industrial settings. Table 1 depicts common products and their pH values.
In industrialized societies, a wide array of substances with varying pH levels exists, ranging from highly acidic to highly alkaline. The pH of a fluid can profoundly impact the performance and durability of sealing materials. For example, in applications where seals are exposed to acidic fluids, such as those containing corrosive chemicals like acetic acid, battery acid and phosphoric acid, low pH levels can accelerate the degradation of sealing materials, leading to leaks and premature failure. Conversely, in environments with alkaline fluids such as magnesium hydroxide, potassium hydroxide and lithium hydroxide, the risk of degradation arises due to the potential for alkaline hydrolysis, which can weaken or break down seal materials over time.
Nitrile butadiene rubber (NBR) seals, commonly used in O-rings and other sealing components, exemplify the sensitivity of sealing materials to pH. NBR contains carbon and nitrogen bonds that are susceptible to chemical attack in acidic or alkaline environments. In highly acidic media, the abundance of hydrogen ions can trigger acidic reactions, causing degradation of NBR seals.
Similarly, in alkaline media with high concentrations of hydroxide ions, alkaline reactions may occur, compromising the integrity of the seals. To mitigate the risks associated with pH-induced degradation, several key considerations must be addressed:
1. Material selection
Selecting the appropriate sealing material is paramount, considering not only pressure and temperature but also the pH of the fluid being sealed. Different sealing materials exhibit varying degrees of resistance to acidic or alkaline environments, necessitating careful consideration of chemical compatibility. Materials such as fluorocarbon (FKM) and perfluoroelastomers (FFKM) offer superior resistance to a wide range of aggressive chemicals, making them suitable for challenging sealing applications.
2. Testing
In cases where uncertainty exists regarding the compatibility of sealing materials with specific fluids or operating conditions, conducting rigorous testing is essential. Chemical compatibility tests can assess the performance of seals under simulated operating conditions, providing valuable insights into their suitability for real-world applications. By identifying potential issues early on, manufacturers can make informed decisions and optimize sealing performance.
3. Maintenance
Even with the selection of appropriate sealing materials, improper installation practices or inadequate maintenance can compromise the effectiveness of sealing systems. Regular monitoring for signs of wear, damage or degradation is essential for detecting potential issues before they escalate into costly failures. Implementing preventive maintenance protocols, such as lubrication, cleaning and inspection, can prolong the service life of seals and ensure reliable performance over time.
Another important aspect to consider is industrial safety. pH plays a critical role, serving as a key indicator of potential hazards in chemical processing and manufacturing environments. In industries where hazardous chemicals are handled or processed, maintaining the appropriate pH levels is essential for preventing accidents and ensuring the safety of workers, facilities and the surrounding environment. Deviations from the optimal pH range can pose serious risks, including chemical spills, leaks and equipment failures, and can result in injuries, environmental damage and costly cleanup efforts. By closely monitoring and controlling pH levels in industrial processes, operators can mitigate these risks and create safer working conditions for personnel.
Furthermore, pH influences the corrosion resistance of materials used in sealing applications, making it a crucial factor in preventing corrosion-related failures. Corrosion occurs when metals react with acids, bases or other corrosive substances, leading to the degradation of metal surfaces and the loss of material integrity. Sealing systems exposed to corrosive environments are particularly susceptible to corrosion-induced damage, which can compromise the effectiveness and reliability of seals over time. By selecting sealing materials that are compatible with the pH of the fluids they will encounter, engineers can minimize the risk of corrosion and extend the service life of sealing systems, ultimately reducing maintenance costs and downtime.
In addition to corrosion prevention, maintaining the appropriate pH levels in industrial processes can also enhance product quality and consistency. In industries such as food and beverage manufacturing, pharmaceutical production and water treatment, pH control is critical for ensuring the desired properties and characteristics of final products. For example, in the food industry, pH levels can affect the taste, texture and shelf life of products, making precise pH control essential for maintaining product quality and safety. By monitoring and adjusting pH levels throughout the manufacturing process, producers can achieve consistent results and meet regulatory standards, enhancing user satisfaction and brand reputation.
Moreover, pH monitoring and control are integral components of regulatory compliance in many industries, particularly those subject to strict environmental regulations. Failure to comply with these regulations can result in fines, penalties and legal consequences for noncompliant companies. By implementing robust pH monitoring and control measures, industrial facilities can ensure compliance with regulatory requirements, minimize environmental impact and maintain their social license to operate.
In summary, pH plays a multifaceted role in industrial applications, influencing safety, corrosion prevention, product quality and regulatory compliance. By understanding the importance of pH and its implications for sealing systems and industrial processes, engineers and operators can make informed decisions to mitigate risks, optimize performance and achieve sustainable outcomes. Through ongoing education, training and innovation, the sealing industry continues to adapt and evolve, leveraging pH as a critical parameter in the pursuit of safety, efficiency and environmental stewardship. Industrial organizations and associations also play a crucial role in providing guidance and resources for professionals involved in sealing applications.
We invite your suggestions for article topics as well as questions on sealing issues so we can better respond to the needs of the industry. Please direct your suggestions and questions to sealingsensequestions@fluidsealing.com.