Pump System Improvement
06/06/2016
My longtime readers know that a piping system is made of three parts: the pump elements, process elements and control elements. The pump elements add all the energy needed to move the fluid through the system; the process elements make the product or provide the service; and the control elements improve the product or service quality. Understanding how these various elements work together provides a clear picture of how the system works.
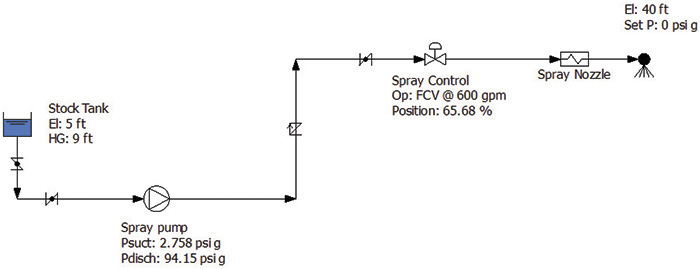
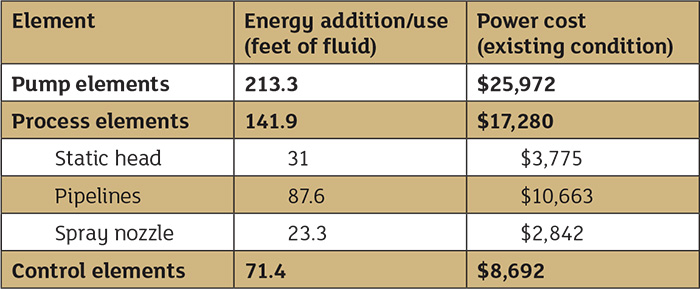
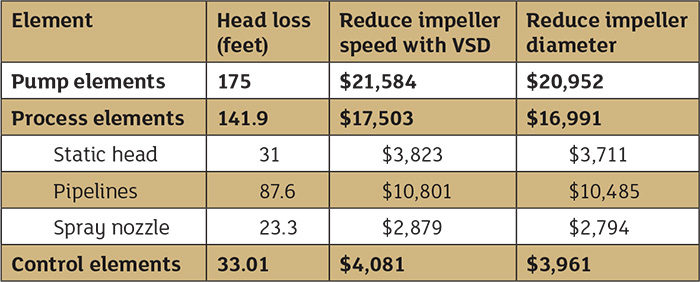
See more Pump System Improvement articles by Ray Hardee here.