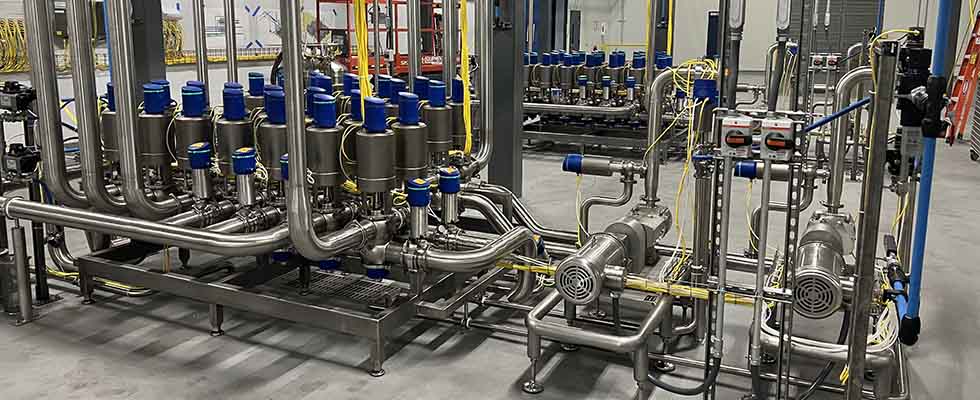
In the dynamic landscape of food, beverage, dairy, pharmaceutical and other high-purity processing, energy efficiency is not just a want, but a requirement. With the global demand for sustainable practices escalating, processing plants are under increasing pressure to minimize their environmental footprint while maximizing operational efficiency. A large portion of this effort revolves around the optimization of motor and drive systems, which are the workhorses of these facilities.
Electric motors account for a substantial portion of global electricity consumption. Estimates suggest that these devices consume between 40% and 50% of the world’s electricity, highlighting their pivotal role in energy efficiency initiatives. In sanitary processing plants, motors drive pumps, mixers, conveyors and many other critical pieces of equipment. Consequently, even minor improvements in motor efficiency can translate into energy savings, cost reductions and maximized productivity.
The Significance of Motor Efficiency
The efficiency of a motor directly correlates with its energy consumption. A more efficient motor converts a greater percentage of electrical energy into mechanical power, minimizing waste in the form of heat. This translates to reduced electricity usage for the same output. In processing plants, where motors operate continuously or for extended periods, the cumulative effect of even small efficiency gains can be substantial.
Furthermore, motor sizing plays a crucial role in energy efficiency. Oversizing a motor, a common practice to ensure adequate performance, often leads to inefficiencies. Motors operating at low loads typically experience reduced efficiency, resulting in unnecessary energy waste. Selecting a motor that closely matches the application’s load requirements is essential for optimal energy performance.
Increased Control With VFDs & VSDs
Variable speed drives (VSDs) or variable frequency drives (VFDs) are powerful tools for optimizing motor performance and reducing energy consumption. While the terms are often used interchangeably, it is important to understand their nuanced relationship. A VFD is a type of VSD that specifically controls motor speed by varying the frequency and voltage of the electrical power supplied to the motor. Therefore, all VFDs are VSDs, but not all VSDs are necessarily VFDs.
Unlike traditional motor control methods that rely on fixed speeds, VSDs and VFDs allow for precise control of motor speed, enabling adjustments based on actual load requirements. This capability is particularly beneficial in applications with fluctuating loads, such as pumping, mixing and conveying, which are prevalent in processing plants in the food, dairy, beverage and other consumable goods industry.
In pumping applications, for instance, VFDs can adjust pump speed to match the required flow rate. By reducing the frequency and voltage supplied to the motor, the pump’s speed is reduced, eliminating the need for throttling valves that waste energy by creating artificial resistance. This precise control ensures that the pump operates only at the speed necessary to meet the current demand, resulting in substantial energy savings.
Similarly, in mixing applications, VFDs can optimize mixing speed based on the product’s viscosity, desired mixing intensity and the specific stage of the process. For example, a slower mixing speed may be sufficient during initial blending, while a higher speed may be required for final homogenization. By precisely matching motor speed to the application’s needs, VFDs are able to:
- Minimize energy waste
- Improve product consistency
- Enhance operational efficiency
The ability to control motor speed with such precision also extends to conveyor systems, where VFDs can adjust the conveyor speed to match the production rate. This avoids unnecessary motor operation at full speed when the production line is running at a lower capacity, further contributing to energy savings.
Essentially, VFDs, as a subset of VSDs, provide a method of controlling motor speed through frequency and voltage modulation. This technology allows for dynamic adjustments to motor performance, ensuring that energy is used only when and where it is needed, resulting in energy savings, reduced wear and tear on equipment and improved process control.
The Impact of Operating Conditions & Technology
Several factors can influence motor efficiency, including operating conditions and motor technology. Motor speed, load variations and ambient temperature can all impact performance. High operating temperatures, for example, can reduce the efficiency of a motor and shorten its lifespan. Regular maintenance and proper ventilation are crucial for maintaining optimal operating conditions.
Technological advancements have also played a role in improving motor efficiency. Newer motor technologies, such as high-efficiency motors, offer superior energy performance compared to older designs. High-efficiency motors incorporate improved materials and designs to minimize losses, resulting in even greater efficiency gains.
The Benefits of Efficient Motors & Drives
The benefits of using efficient motors and drives extend beyond energy savings. They also include:
- Reduced electricity bills are a direct result of lower energy consumption, leading to cost savings over the equipment’s lifespan.
- Reduced energy consumption translates to a smaller carbon footprint, contributing to environmental sustainability.
In addition to cost and environmental benefits, efficient motors and drives can enhance operational efficiency. Precise control with VSDs can optimize equipment performance, improve product quality and increase productivity. In mixing applications, for example, optimized mixing speeds can improve product consistency and reduce processing time.
Mixing Efficiency & Energy Savings
Mixing processes are vital in food, beverage and pharmaceutical manufacturing. Innovative technologies that enhance mixing efficiency contribute to faster, more efficient processing and higher productivity. By improving mixing processes, plants can save energy while ensuring product integrity, such as color, flavor, texture and aroma.
For example, technologies that combine pump and powder dissolving functions into single units can reduce the need for multiple motors, leading to substantial energy savings. Additionally, systems that preblend powder and liquid before the high-shear stage can ensure quick and complete powder dissolution with minimal energy input.
Utilizing efficient agitators that provide gentle handling of sensitive ingredients can reduce energy consumption significantly. Impellers designed for effective and gentle mixing, low-shear performance and uncompromising hygiene can contribute to energy savings while maintaining product quality.
Looking Forward
As sanitary processing plants continue to prioritize energy efficiency, the role of motors and drives will become increasingly critical. By investing in efficient motor technologies, implementing VSDs and optimizing operating conditions, plants can achieve energy savings, reduce their carbon footprint and enhance operational efficiency. The continuous evolution of motor and drive technologies promises even greater opportunities for energy optimization in the future, ensuring a sustainable and efficient processing industry.