These technologies allow membrane-based distillation components to be used to produce high-purity drinking water from heavily compromised water sources.
10/13/2015
Part 1 of this series (Pumps & Systems, September 2015) discussed recent developments in the field of nanotechnology that have significantly impacted the water and energy industries (read the article here). One such material that can be used in the water treatment process is formed through the chemical modification of styrene block copolymers that are widely used in glues and gaskets. This material can be used to produce membranes that provide molecular pathways for the transport of water between surfaces without traditional porosity. These membranes have a unique ability to selectively move water at a higher rate than gases, ions and other materials.
Treatment of Contaminated Water
A water treatment process capitalizing on the versatile nature of these nanomaterials is in the early stages of commercialization. The nanomaterial allows membrane-based distillation components to be used to produce high-purity drinking water from heavily compromised water sources that are difficult to treat with conventional methods. According to a new study from Bluefield Research, these products are beginning to open up the possibility of recovering nearly all forms of water for reuse, which is a solution likely to receive significant funding in the years ahead.1Features
Nanomaterial features that are important for water treatment include the following. Produces high-quality water. The selectivity of this class of nanomaterials produces water that is significantly higher quality than traditional reverse osmosis (RO). The typical total dissolved solids (TDS) content of the product water is 1 to 12 parts per million (ppm)2, which is one to two orders of magnitude lower than the water typically produced by RO. Works well at high concentrations. Distillation processes transfer water molecules without the need to overcome osmotic pressure gradients, which rise rapidly as the wastewater TDS increases and reduce the energy efficiency of RO. Third parties have successfully tested the presented class of nanomaterials using wastewater with a chemical oxygen demand (COD) as high as 43,000 mg/L. Has a high capture rate. Functionality with highly concentrated wastewater allows as much as 98 percent of the incoming water to be recaptured as clean product water. Large RO installations typically operate in the 40 to 60 percent recovery range, and small portable/residential products typically recover 10 to 20 percent of the incoming water. Encounters less fouling. As a wastewater stream flows past in a cross-flow configuration, the nanomaterial presents a smooth, solid polymer surface with no discernible pores, giving the material superior resistance to fouling. Suspended particles formed from saturated wastewater have a difficult time displacing the layer of water molecules held near the hydrophilic surface of the nanomaterial by intermolecular forces to form durable bonds with the polymer. American Society for Testing and Materials (ASTM) G21 and G22 tests show it does not support bacterial or fungal growth. Produces reduced effluent volume. The material's ability to operate at high concentrations with less fouling allows the operator to release a smaller volume of effluent with higher concentrations than traditional processes. This makes zero-liquid-discharge (ZLD) processes more practical. Require less pretreatment and chemical usage. Most assessments of the operating cost of RO place the cost of treatment chemicals at 5 to 15 percent of the annual operating cost budget, and water systems made using the referenced nanomaterial effectively eliminate this expense. Have a long lifespan. Pilot systems using these nanomaterials have run for more than two years with the materials showing no need for replacement because of performance degradation. Made of simple, robust materials. The maximum pressure in most nanomaterial water cleaning systems does not exceed 15 pounds per square inch (psig) (0.1 MPa), as opposed to reverse osmosis units at up to 1,180 psig (81.4 MPa). This allows the use of inexpensive, corrosion-resistant plastic materials instead of pressure-rated vessels made from specialty stainless steel alloys.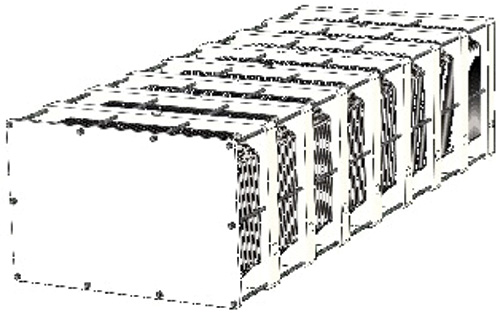
Treatment Systems
Water treatment systems based on nanostructured membranes use temperature and vacuum pressure to evaporate high-purity water vapor from the feedwater. The key component in these systems is the membrane evaporator, a module that uses the nanomaterial to separate heated feed water from a vacuum. Water molecules permeate through the membrane and evaporate from the opposite surface as high-purity water vapor to be collected and condensed into clean, potable water.Membrane Vacuum Distillation
Where thermal energy to maintain a high feedwater temperature is readily available, membrane vacuum distillation uses a cool surface to condense water vapor coming through the membrane into liquid water and draw additional water vapor into the partial vacuum created by that phase change. While some designs incorporate customized condensing surfaces into the evaporator module, the simpler implementation is often to use a separate condenser component. Either variation of the design employs a roughing vacuum pump that is tolerant of water vapor to evacuate the system and periodically remove non-condensable gases. The largest electrical input typically drives the feedwater circulation pump, which is typically a centrifugal style to produce high flow rates through the evaporator at modest pressures. The water does not need to be at high pressure to drive the evaporation process, but the circulation flow rate may be two orders of magnitude larger than the rate at which clean water is produced—a ratio that reduces the temperature drop caused by the vapor carrying the heat of evaporation away from the membrane to the condenser.Membrane Mechanical Vapor Compression
One key to expanding the available market for nanomaterial membrane technology is systems that reduce or eliminate the need for an external heat source. This is possible with a membrane mechanical vapor compression (MMVC) system that uses the nanomaterial as the evaporation surface while retaining the thermal energy within the feedwater.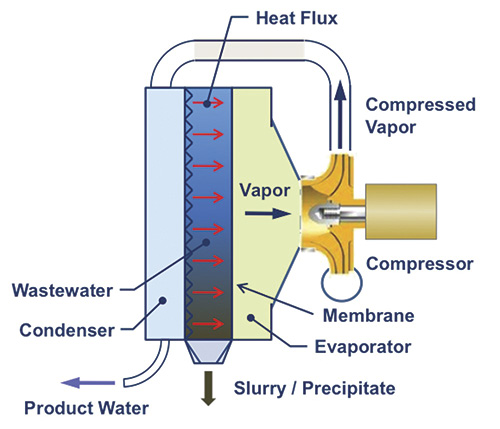
Addressing the Water-Energy Nexus
It has long been known that providing electricity requires a lot of water, and providing water requires a lot of electricity. Simply put, "water needs electricity needs water." Nanomaterials can offer one significant opportunity to break the nexus by cleaning post-production contaminated water to high levels of purity for safe and immediate reuse. Read the first part of this series, here. References- https://www.pumpsandsystems.com/news/2015-05-20/drought-driving-greater-reliance-wastewater-reuse-california#sthash.q6UwEnrh.dpuf
- Throughout this document, the terms ppm, parts per million, and mg/L are used interchangeably.