As consumer demand for convenient, disposable wipes continues to grow to over $2 billion annually, nearly double the rate of retail purchasing since the early 2000s, pump manufacturers are forced to develop new designs to take on the growing challenge of handling more difficult to pump materials at increasing volumes. The increased maintenance costs directly related to higher volumes of larger, non-biological solids has shifted the focus from system energy efficiency costs, to system operating and maintenance costs related to equipment failure due to ragging. Currently, many pumps require weekly, even daily, maintenance to unplug blockages, which increases labor and parts costs well beyond those in the past and also creates greater health and safety risks to operators and residents in areas where pumps stations fail. While original pump designs performed well pumping soft biological solids with more consistent, manageable solids sizes, current pump designs must contend with the presence of much larger, stringy materials. These stringy masses carry increasing amounts of grease and grit; the fibers in the wipes pick up the fats, oil and grease in the waste stream and offer a congealing medium. The rags get heavier with these coagulants; necessitating that fluid velocity in the piping system to properly carry these heavier solids has increased from recommendation of 2 to 4 feet per second in a pre-wipe period, to a range of 5 to 7 feet per second now, in order to avoid settling issues. This increased velocity is critical in piping design and pump operating speed considerations—the increased velocity contributes to greater pipe abrasion. The potential increase in abrasive materials attached to rags will play a part in the selection of proper materials in the pump wet end to maximize its operating life. In 2011, one manufacturer developed a cutter pump design to address the increase in rag material in not only wastewater applications, but other solids-handling applications in the agricultural and industrial markets. The original design incorporated a hardened rotating cutter ring affixed to the impeller, serving as both a cutter ring with teeth and as the pump wear ring and a stationary cutting element fixed in the suction inlet. As solids pass into the pump the stationary cutter ring works with the rotating cutter shearing the materials and reducing them to a manageable size to pass through the impeller vanes.
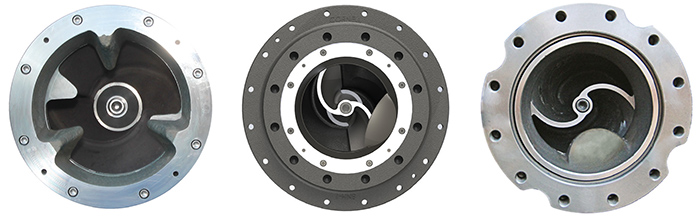
Recommendations & Observations
- When designing pumping systems to handle the presence of rag material, select a pump design that can handle the volume of material anticipated.
- Fluid velocity in the inlet piping system must be able to carry the solids into the pump inlet for proper performance. Pipe size and pump operating speed are critical to proper velocity.
- Pump operating speed is important to cutting efficiency. Consult with your pump supplier for the minimum recommended operating speed.
- Select the proper construction materials for the pump to reduce wear from abrasion. Harder materials or coatings can increase the operating life of the pump system.
- Whether upgrading an existing system or designing new, be sure to compare the system operating and maintenance cost to energy efficiency costs. Most of the time, running the system to best handle the pumped material with minimal downtime will be a less expensive station to operate and create a safer environment for the maintenance staff.