During the past few years, end users in the Middle East power generation industry have considered specifying pumps according to American Petroleum Institute (API) standards. The standards, according to the API website, "are designed to assist industry professionals improve the efficiency and cost-effectiveness of their operations, comply with legislative and regulatory requirements, safeguard health, and protect the environment." Typically, the standards require a more robust equipment design. Two such standards commonly apply to pumps: API Standard 676 for rotary positive displacement pumps and API Standard 610 for centrifugal pumps. As safety standards become more stringent, API standards, or their variations, could more frequently be implemented in industries such as power generation. Understanding what these standards mean and how to apply them can be beneficial for end users.
Refinery Safety Compliance
New refineries in the Middle East have spurred the regional specification of API standards for pumps in the power generation market. The national or private oil companies that build the refineries often construct power plants for the facilities. The oil and gas industry requires API compliance for processing equipment to ensure safety throughout the refinery. This compliance must be based on API industry standards as understood by the equipment manufacturer and the end user—in this case, the oil company. These oil companies may naturally extend the same API compliance requirements for their hydrocarbon processing equipment in the adjoining power plant. Beyond the pump, API compliance is now being considered or required for the full range of process and auxiliary equipment. API standards are often required for electric motors, valves, tanks and instrumentation. This applies to both new facilities and retrofit operations, particularly if facility ownership has changed and the new owner is committed to API certification. API compliance may go beyond the power plant. If under the oil company's ownership, other areas of the refinery, including the water treatment facility, may have to meet the standard. As safety standards become more stringent, the application of API standards or their variations could have more international appeal among professionals in the power generation industry.Defining API Standard 676
This standard is a purchase specification used to facilitate the procurement and manufacturing of specific rotary positive displacement pumps. Like all API standards, 676 was developed to establish a minimum standard for process pumps in mission-critical applications. In oil and gas, these applications could be defined as injection, gathering, transfer and pipeline pumps.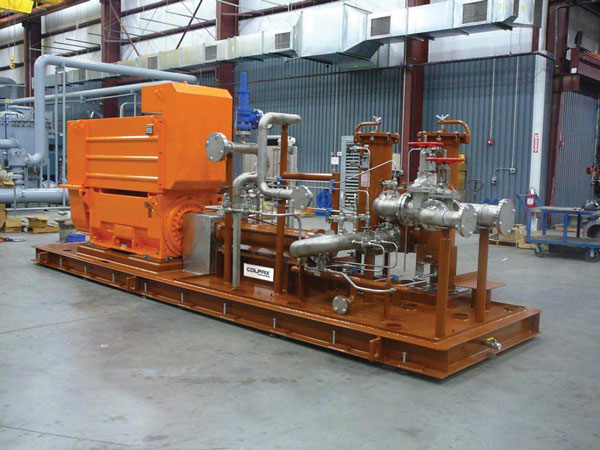