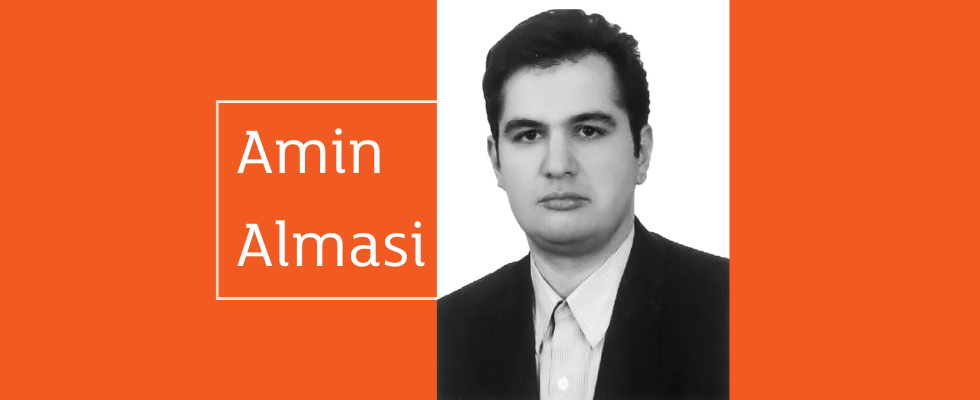
This article discusses the operation and operational assessment/management of pumps and how to deal with the operational problems of pumps. Operational assessments are structured studies that methodically examine each pump and its operation to assess operability, reliability and safety. These also review the operating conditions and operational procedures. Deviations from mandatory codes or established procedures need attention.
Operational Assessments
The first step in the operational management of pumps and the assessment of their operation is to evaluate if the installation and operational procedures meet mandatory/applicable codes, client specifications, operational standards and good working practices.
The weaknesses of a pump or its systems should be identified. Operational and procedural controls are also the focus of any comprehensive operational and reliability assessments. These would include assessing engineered controls, sequences of operations, human interactions, management of alarms and trips and others. This should cover different operational modes such as startup, standby, normal operation, unsteady situations, normal shutdown, emergency shutdown and more.
The operational assessment/management of pumps needs multidisciplinary input, review and help. These are usually cross-functional team efforts and rely on specialists and experts from various disciplines with appropriate skills and experiences who display intuition and good judgment.
A pump system may have several protective layers that ideally work independently of each other (i.e. mechanical relief devices used to protect against overpressure or overspeed protections). A mixture of quantitative, semiquantitative and qualitative methods can be used for the operational risk assessment of pumps. The most appropriate method should be selected based on the application. This will likely be a semiquantitative method.
Pump Operation
There have been many types of operational problems and hazards for pumps. However, many of them should be removed during different safety/risk assessments at detail design stages. For the operational assessment/management of pumps, the focus has typically been on the following:
Problems/hazards rooted in human operator performance and behaviors.
Problems/hazards that are difficult to detect, analyze, isolate, count and predict. These problems/hazards might be missed in design/safety checks during normal design reviews at the detail design and installation stages.
Existing protective devices that prevent or safeguard against the adverse consequences of operational problems and hazards are considered and modifications are planned where the protection is considered inadequate. These actions/improvements could be to remove the cause and to mitigate or eliminate the consequences.
Operational feedback should confirm the assessment and control steps are adequate. Often the assumptions made about the level of residual risks should be re-evaluated before the startup or during the first days/weeks of the operation.
Practical Issues & Realistic Solutions
Most operational problems are due to human error. However, outside of typical slips and lapses in attention, some so-called human errors are the result of inadequate training or instruction. This is an important issue for the operation of complex pumps.
Pumps are inherently better and safer if the problems and hazards have been reduced or removed rather than controlled by added-on protective equipment, devices, controls or procedures which can fail or can be neglected. The best way to prevent operational problems, safety issues and risks is to use safer materials/mechanisms instead of risky or problematic ones. For instance, when dealing with dangerous/risky materials, an option is to use so few hazardous materials that it hardly matters if they leak or are misused.
Layer of Protection
The safety integrity level (SIL) assignment method that is usually selected for pump systems is usually the layer of protection analysis (LOPA) method. The LOPA method is a semiquantitative approach that relies upon risk acceptance criteria and the development of a set of guidelines that are to be applied consistently throughout LOPA. In other words, this method can provide the opportunity to use the codes and academic details, as well as opinions of subject matter experts. This usually leads to a strong mixture of academic data and experiences and knowledge applicable to the pumps.
Optimum Configuration of Alarms
Alarms or even shutdown requests can be added as the result of many different studies and reviews of pump systems. Alarms and their optimization are closely related to operation and operational management. Too often, for many issues, the first and simple recommendation has been to put in an alarm and leave it to operators. This misguided practice has been used for decades. This practice causes further problems for the operation, safety and reliability of pump systems. Optimum configuration of alarms has always been important.
Too many alarms are bad and too many shutdowns is disaster. Human operators do not cope well with alarms, as they can suffer from a condition called “cognitive overload.” In simple terms, an operator should not be presented with more information and alarms than they can process and act upon in the time available. In modern plants, when an upset (or a significant operational problem) does happen, the transition from normal to abnormal can be rapid. The result is many alarms in a short time. As an indication, the sustained rate of about two or three alarms per minute is as much as a normal operator can handle. The higher the alarm rate, the lower the probability of the operator noticing it and responding effectively.
As the first few alarms sound, the human operator moves quickly from vigilance mode to action mode. Once into action mode, people rarely re-evaluate their initial analysis, even if subsequent information clearly indicates that the initial analysis was wrong. In other words, once in action mode, there is a powerful human tendency to “confirm” rather than to “falsify” hypotheses and rethink the situation. This bias, which can be created or escalated by too many alarms, could cause further problems.