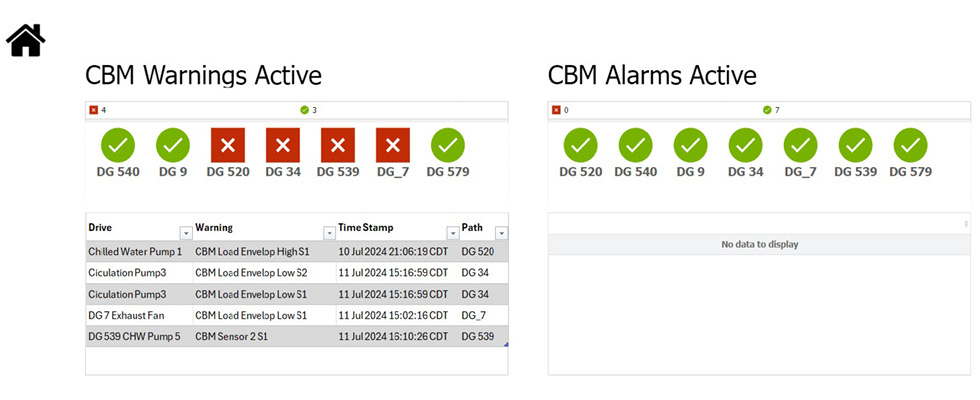
These days, the use of variable frequency drives (VFDs) in motors and applications is common. The drive technology has improved to the point of being able to withstand even the most challenging conditions while providing trouble-free operation for multiple types of motors, including induction, synchronous and servo motor applications anywhere in the world. The combination of solid design, powerful microcontrollers and sophisticated software-based solutions, such as condition-based monitoring (CBM), in VFD technology not only ensures substantial energy savings and precise control but also enhances product quality and operational reliability across a wide range of applications in the water and wastewater industry. Internet of Things (IoT) solutions that offer the capability of remote monitoring add another layer to the benefits of VFDs.
Condition-Based Monitoring
In the water and wastewater industry, maintenance is a key component of system operation. With microcontroller technology, VFDs use voltage and current feedback to provide a monitoring approach for maintenance of the plant. The drives are effectively used as a sensor, where their CBM capability allows for early detection of changes in motor winding resistance, load envelope, system vibration, bearing failures or pump cavitation. By monitoring the condition of the motor loads or equipment in real time, maintenance can be scheduled proactively when needed, minimizing unplanned downtime. This can reduce maintenance costs by optimizing the maintenance resources as well.
In VFDs, CBM technology monitors a wide array of parameters and generates numerous values. Keeping a vigilant eye on each parameter and value is crucial for ensuring optimal performance and preempting potential issues. By closely monitoring these metrics, operators can proactively address any deviations or abnormalities, thereby enhancing the reliability, efficiency and life span of the VFD pump systems. To monitor this data, plants can employ various platforms equipped with different tools and communication protocols, whether online or offline. Remote monitoring has become the latest trend in the industry, enabling real-time information about events to ensure the drive and connected equipment are functioning properly.
Remote Monitoring
Remote monitoring is based on an IoT solution that consists of gateway hardware installed at the user site and cloud software that stores and analyzes data. The hardware is connected to the drives, and it gathers data at intervals and uploads it to the cloud for analysis. The operators or maintenance team can access the data on the cloud and view the visualization of key performance indicators (KPIs) through a web portal. The remote monitoring infrastructure enables the connection of drives and pump systems from remote locations to be monitored centrally (Image 1).
By using remote monitoring, operators and maintenance teams can obtain a wealth of information crucial for managing drives and pumping systems effectively. This data includes drive model numbers, horsepower ratings, software versions and more. The drive dashboard provides views of critical parameters such as motor current, speed, torque, energy consumption, system pressure and others, in real time. It includes CBM data on motor windings, load envelopes, vibration sensors and cavitation, similar to the example in Image 2. A VFD’s historical data in the cloud can display a timeline of events that includes fault states and abnormalities and also features a datalogger and parameter browser. These tools enable proactive maintenance strategies by providing comprehensive insights into system performance and operational trends over time.
Additional advantages include:
Email and text messages: The system is configured with email and text message alerts, ensuring notifications can reach recipients wherever they are needed. These alerts are not limited to a single individual but can be accessed by a group of people, enabling swift and widespread communication of critical information.
Accurate and real-time information for analysis: Having 24/7 access to detailed, real-time and accurate information enables corrective actions, leading to faster response times and minimizing downtime. This proactive approach enhances the efficiency and reliability of VFDs and pump systems (Image 3).
Fault history and data logging: The cloud server maintains the fault history and the connected data files, which show the selected signals and parameters in a microsecond. The data logger files can be shared with experts for detailed analysis of the fault and for implementing corrective actions.
Data analyzer: The analytic view from the dashboard gives the capability to analyze the collected data and create histograms. This feature helps to detect anomalies or decreases in performance and enables optimization for more efficient systems.
The ability to set custom warning and alarm thresholds: Plant operators can establish a baseline for normal operation of system warnings and trip thresholds.
Data at the user’s fingertips: Key drive data and parameters that can be used for a wide range of service actions are backed up safely in a centralized location. They can be accessed via a web portal, ensuring simple recovery in case of drive failure or if a drive needs to be exchanged.
Data security: Next-generation VFDs come with cybersecurity features that provide data security with signed and encrypted firmware and applications software.
Remote monitoring with CBM capability not only enhances operational efficiency but also allows for proactive maintenance and troubleshooting, ultimately reducing downtime and improving overall productivity. Furthermore, remote monitoring enables businesses to make informed decisions quickly, optimize resource allocation and ensure compliance with regulatory standards.