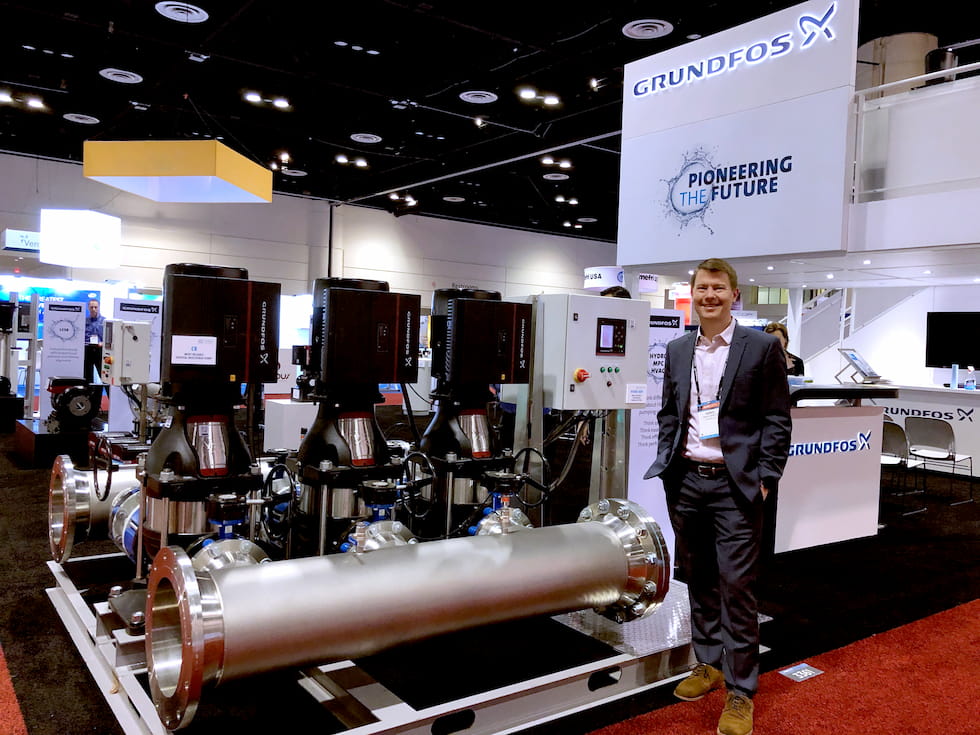
ORLANDO, Florida – Some talk among attendees at the recent AHR Expo at the Orange County Convention Center centered around packaged pumping systems.
For example, Grundfos exhibited its Hydro MPC packaged pumping system family, showcasing both the flagship CR variation and the new CME option. The Hydro MPC platform is not new to Grundfos, but it was traditionally used in plumbing applications, said Greg Bretz, Grundfos’ vice president of sales for commercial building services and a Pumps & Systems Top 10 professional to watch in 2019. The Grundfos Hydro MPC package has been used in heating, ventilation and air conditioning (HVAC) and building services markets.
“I think one of the things we’re seeing is a trend towards packaging,” Bretz said. “You see here in our booth [with the Hydro MPC CR and CME packages), we really see a trend toward modular construction. It’s in all levels of the industry.”
One factor for more packaged pumping systems, said David McMillan, Grundfos executive vice president for building services, is the decline in the skills gap.
“We see more pumps, integrated motors, drives and controls from one supplier for various reasons,” McMillan said. “One is you get a fit and function that’s the same time repeatable, but the most important thing is that if you look at the construction industry, we have a major problem with the shortage of labor. If you look at some of the generations that are leaving our industry, I don’t know what the stat is, but for every two or three tradesmen that leaves the trade, only one comes back into the market.
“Long term, that could have a real problem in terms of economic growth because there’s not enough people to build our buildings.”
McMillan, pointing at the Hydro MPC CME, then indicated companies are making products that combine all the parts into one system.
“We’re not trying to displace a competitor,” McMillan said. “We’re trying to displace ourselves and the idea is this would have traditionally been two pumps that you sent to a site, you put in an inertia base, you add suction diffusers, triple duty valves, you add it together, add a VFD [variable frequency drive], someone added a control panel and they needed to figure out how this was going to work.
“We’ve done all of that for them. The whole idea is that this can be shipped to site, can be dropped into place and very quickly you bring power to it, fill the system with water, have a very quick commissioning and you have a ready-made pumping solution that would have been 25 pieces, 35 to 50 pieces. We’ve done all of that inside a controlled environment.”
McMillan also said that smaller pumps inside one system is one way to go.
“Take a regular system in Chicago or Texas,” McMillan said. “For example, they don’t run 100 percent load all the time, so selecting one pump to be really great at 100 percent load is great when the chiller’s working at 100 percent load, but what about when the chiller is working at 30 percent load? All the sudden, wouldn’t it be great that, instead of slowing down a really efficient pump, but to divide the flows by smaller pumps that are really efficient as well and we could also utilize things like ECM [electronically commutated motor] permanent magnet technology.
“I would say the number of pumps you see [is increasing], the packaging and also integrated controls— the chiller manufacturers did it before, but you can’t buy a chiller without controls anymore. We think the best people to control pumps in the world are the pump manufacturers, and I speak for all of us.”
At future AHR Expo events, users may be introduced to an expanded range of ECM technology.
“One of the big things I think we’re going to see is, again, in addition to the packaging, is also the ECM motor technology,” Bretz said. “We brought a 15-horsepower (hp) today, but we are expanding that line, that could go up to 50, 75, 100 hp very soon.”