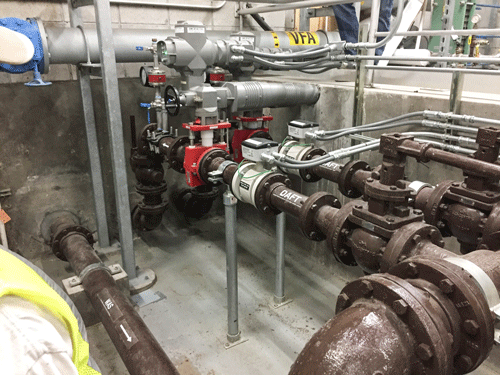
Pinch valves are gaining popularity in water and wastewater due to their ease of operation, infrequent need for maintenance and ease of repair. When they are in the open position, there are no pockets or cavities for material to accumulate in and cause operational problems. Pinch valves are 100% full port and provide 100% bubble tight shut-off. They are often used for influent control, grit removal, sludge, raw sewage, sodium hypochlorite, scum, lime addition, digestor gas, alum, ferric chloride and other applications.
Selecting historical equipment may not always be in a user’s best interest. For many years, plug valves have been used in water and wastewater. They are a known commodity to many plants. Plug valves are reliable, but if a plant does not have the manpower to periodically operate the valves, it may lead to inoperable valves, repairs or replacement. A plug valve that has been closed for six months may possibly become a problem. Plug valves have a cavity around the plug that slowly packs full of material through normal operation and can become more difficult to operate. Finally, even full port plug valves are not 100% full port and have reduced flow coefficients to other types of valves.
The Chester Water Authority in Pennsylvania selected pinch valves for lime isolation at its water plant. Lime is a widely used substance in the municipal water and wastewater industry. Lime is difficult to manage in process piping systems due to its scaling nature, so valves and related equipment in lime slurry service need to be selected carefully to prevent frequent failure of these valves and equipment. Lime can be used in the dry form or made into a slurry for use. Engineering and maintenance people often face a long and potentially expensive trial and error process to find the best equipment to handle lime.
Limestone is mined from a quarry as calcium carbonate (CaCO3). It is then crushed and fed into a kiln at about 2,000 F. The carbon dioxide is burned off (called calcination) to make calcium oxide (CaO). It is used in many industrial processes such as flue gas cleaning, pH control, calcium extraction in pharmaceutical manufacturing and more but its most common use is for pH control.
Lime is difficult for many types of equipment because it does not dissolve but is rather suspended in solution. Lime particles are also jagged. Any cracks, crevices or void areas become natural collection or settling points for the lime particles. These particles settle into this area and then solidify to create a heavy scale. If these areas happen to be moving parts of a valve or a pump, then they may no longer be free to move. Constant equipment jams are typically found with lime as well as lime scales on the interior of piping, which shrink smaller and smaller as the scale increases. Valve seats and pump bearing areas likely will be affected by this buildup of scale.
Recommendations for Lime Slurry Service
Process equipment selected for use in lime slurry should be as free as possible of void areas or collection points. The products should also have the capability to self-clean when lime buildup occurs. A typical lime slurry control loop and pumping station can be a significant draw on maintenance dollars if the wrong products are selected. Full port is a great idea in lime slurry. Even a small crack or crevice can cause countless hours of maintenance and downtime. For all the above reasons, pinch valves have been operating trouble-free at Chester Water Authority for more than 10 years. The pinch valves used were also made of polyamide bodies. So, a 2-inch pinch valve in polyamide only weighs 17 pounds (lbs) and is easy to work with and install.
A pinch valve’s ability to shut off 100% with no hassle or maintenance is an advantage compared to many other valves. Deer Island Wastewater Treatment Plant in Massachusetts has been using pinch valves with Hypalon rubber sleeves in sodium hypochlorite service for more than 20 years without downtime or need for repair. Similar results in the same facility have occurred on grit removal without any repairs.
A high-quality pinch valve can provide decades of no maintenance and trouble-free operation. The manual pinch valves in Image 3 have a fully contained screw mechanism for closing. This enclosed area is packed full of grease before it leaves the factory. Notice the grease nipple on the top of the hand wheel where grease can be added if needed. This valve can sit in the open or closed position for five years or more and it will be as easy to open and close as the day it arrived at the plant.
Pinch valves generally start at an inch. One Florida project that was awarded and will be shipped in 2022 will use a 54-inch pinch valve with an electric motor operator for influent control.
Pumps for Water &Wastewater Treatment
There are many types and styles of pumps used in water and wastewater. One type that has gained popularity is peristaltic pumps. The top application for peristaltic pumps is delivery of sodium hypochlorite for disinfection, but they are also used for pumping lime, ferric chloride, alum and other chemicals. They are popular because they, like pinch valves, have one main replacement part that is a piece of rubber or polymeric tube. They are relatively fast and easy to repair. When dealing with aggressive chemicals, they are often chosen because the rubber hose or polymeric tubes are the only components that contact the medium. Peristaltic pumps also have other features that are desirable in some cases. Peristaltic pumps can run dry without damaging the pump, can perform suction lift duties, are fully reversible and are low shear. The first determining factor on how long tubes or hoses last is how many times the rubber hose or tube is compressed. For this reason, the best potential candidate will be a style that uses a single roller that compresses the rubber hose once per 360-degree revolution. Peristaltic pumps that compress the rubber hose two or more times will have a shorter lifetime and higher maintenance costs. The second determining factor that affects hose life is how much heat is generated in the compression process. If the pump uses metal shoes that rub against the hose, then they generate a lot of heat and require a lot of glycerin to dissipate it. A single roller design will outperform these two-shoe designed pumps in almost every application.
One alternative to peristaltic pumps is progressive cavity pumps. The wastewater industry is a large user of progressive cavity pumps for pumping scum as well as primary and secondary sludges. Deer Island used a number of these pumps for sludge. The facility was faced with regular repairs and replacements of the rotor and stator. About every eight weeks, engineers had to replace both on multiple pumps at a considerable cost.
The facility hired an engineering, procurement and construction contractor (EPC) to help improve the situation. The EPC selected a pump that had a specially compounded nitrile stator and hard coated rotor. The result was that stator life increased from eight weeks to six months. The rotor lifetime increased from eight weeks to one-and-a-half years. The result was millions of dollars of savings over five years on six progressive cavity pumps. The new pumps consistently ran at lower rotations per minute (rpm) while producing higher flow rates than what was in place before.
Engineering firms that bring new technologies and are open to new products are a real find. New technologies bring lower cost solutions that outperform traditional products that are used today. If users want to have a cutting-edge facility with superior performance and lower cost of operation, they need to be involved and push for equipment they want to see installed in the plant.