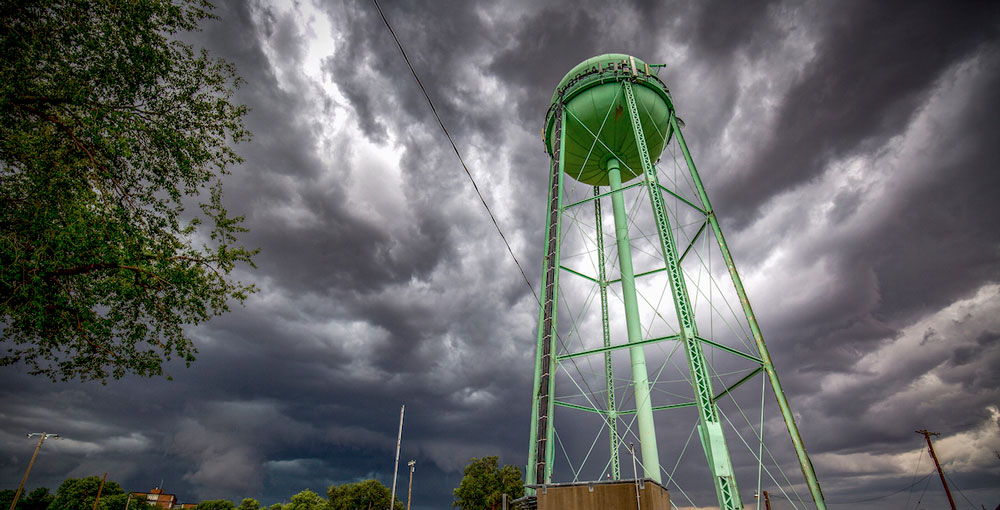
As natural and human resources get stretched, the need for equipment that runs efficiently has become more critical than ever, whatever the job. This is especially true in pumping systems, where water management plays an essential role in various industrial, commercial, municipal or agricultural operations. Efficient solutions deliver positive financial benefits, yet system reliability—including steady operation and consistent performance—is still nonnegotiable.
A growing solution for delivering higher efficiency with proven reliability is a system built around a permanent magnet (PM) motor. PM rotors are magnetized at all times due to the raw material selection and require no electrical power, making them more efficient, especially at reduced speeds and partial loads. PM motors operate more efficiently using rare earth magnets that perform with no slip. This translates into lower input power for the same output power, saving on operational costs every time the motor runs. Also, lower current means that specific components of the system—including variable frequency drives (VFDs), motor cables and filters—might result in smaller size requirements and, consequently, become less costly.
The advancement and use of variable speed technology within the pumping industry coupled with the benefits provided by PM motors means engineers can trust that this system solution provides cost-effectiveness and efficiency.
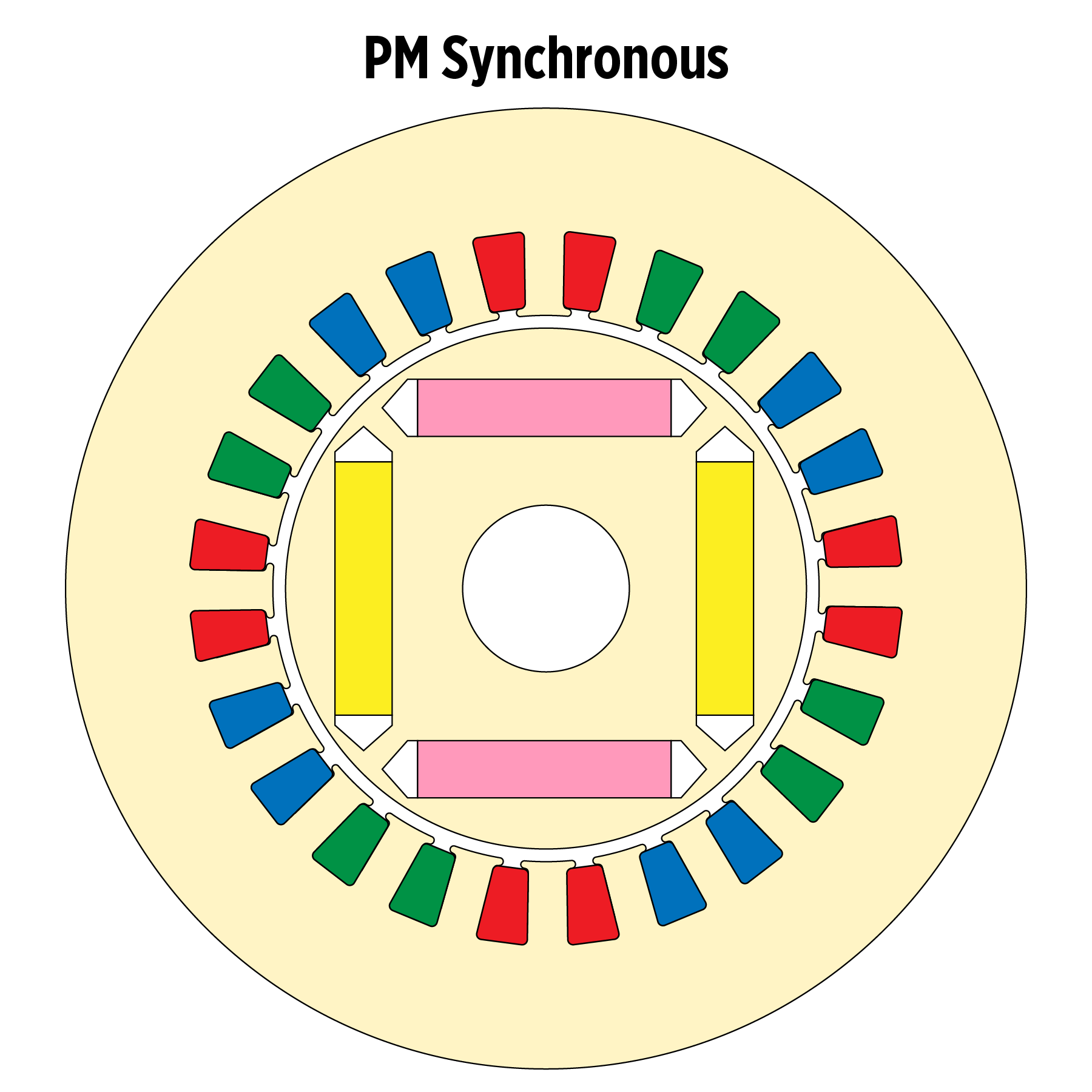
How Do PM Motors Perform in Submersible Applications?
PM motors provide benefits in submersible applications. A PM motor in a submersible pump may lead to lower total cost of ownership (TCO), more efficient operation, better performance and less downtime. Consider that PM motors run with an efficiency rate of about 90% to 94%; PM motors deliver strong performance across a range of speeds for longer motor life and they operate with no slip. Their speed is constant regardless of load, delivering consistent water distribution. When paired with a pump in submersible installations, PM motors offer high- efficiency operation and speed.
PM Motors Deliver Peak Efficiency
According to the Environmental Protection Agency (EPA), about 30% to 40% of a municipal government’s energy consumption goes toward powering water and wastewater plants. Higher efficiency in pumping operations can lead to long-term benefits and major cost savings for not only municipalities but pump operators in any industry. PM motors run with an efficiency rate of about 90%.
They run this efficiently since the rotor does not need to be magnetized, concentrating all the power into motor shaft rotation. No energy is lost due to magnetization of the rotor, concentrating more power into motor shaft rotation. Because of this power concentration, PM motor systems can run at a synchronous speed, providing improved hydraulic performance. With no slip, the motor speed is consistent and will not vary regardless of load.
According to field trial data for PM motors, typical high-duty rate systems can have a payback of one to two years. Paired with a VFD, a system can optimize performance and maximize system life while relying on real-time monitoring, protection and customizable application-specific programming software as needed to cover all user requirements. These efficiency savings also position owners and operators for the future. Energy efficiency across a broad range of operations and infrastructure-related equipment is continuing to be prioritized. PM motors ensure energy-saving benefits to meet compliance considerations now and as regulations evolve.
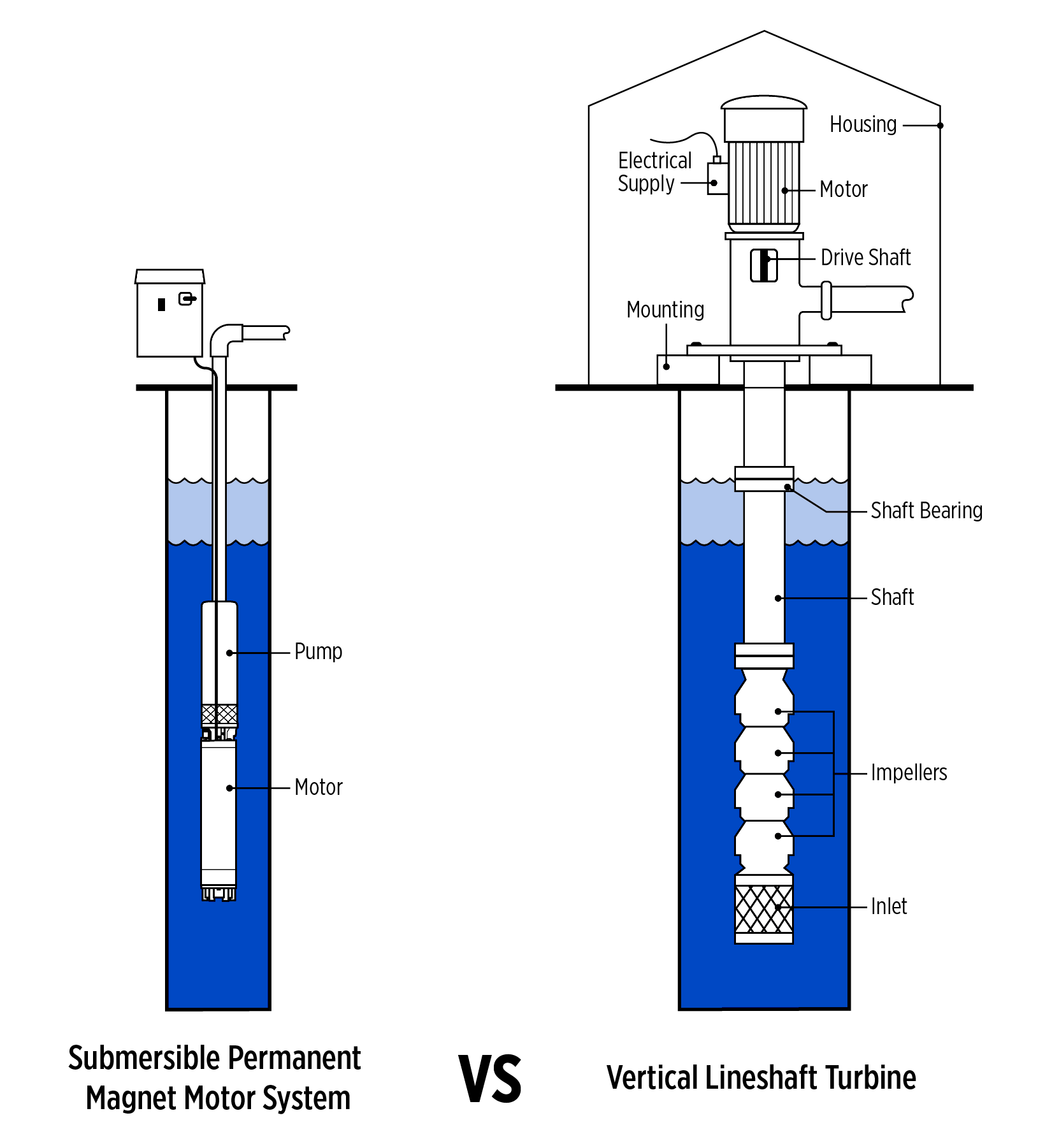
Efficiency Over a Spectrum of Speeds
VFDs are a popular electronic device used to vary the speed of a pump. A PM motor paired with a VFD delivers energy savings and advanced speed control. An induction motor will run at the slip speed at its rated voltage. If a user tries to increase the speed of an induction motor above 60 hertz (Hz), it will run in a weakened field, thereby lowering efficiency. In contrast, PM motors have no slip and are designed to run with a synchronous speed at their rated voltage. This means users are not compromising speed for efficiency. When running a PM motor with a VFD, users can enhance and expand the pump envelope by gaining optimized efficiency. Last but not least, when a pumping system runs with PM motors, users can experience a flatter efficiency curve over a larger range of horsepower (hp), allowing users to cover various ranges without needing to stock dozens of different motors. This can reduce inventory, overhead and costs.
Noise Reduction & More
PM motor systems also offer maintenance advantages and noise-reduction benefits, along with cost savings in installation. When it comes to submersible pumping systems, the overall installation features fewer moving parts than those required for jobs with vertical lineshaft turbine systems (VLSTs). Having fewer parts can lead to a smaller overall size. This may save owners on installation time, shipping expenses and other costs.
PM motors used in submersible applications offer more silent operation and reduce noise pollution. Environmental or natural damage is also less of a concern with submersible motors since they are protected underground and away from heavy equipment, lightning and other potential hazards.
One final, often overlooked, benefit is the ability of PM motors to work in complex applications where submersible pumps are preferred. For example, if a user is installing a pump in a misaligned well, a submersible pump is typically the better solution, thought it will experience wear, tear and reduced longevity. Does a user need high flow from a reduced diameter borehole? Submersibles are typically operated at higher speeds since the pump and motor are close-coupled, enabling them to move more water with a slimmer diameter pump. This changes the pump size and, therefore, can offer the opportunity to drill a smaller borehole for the installation of the smaller diameter pump and motor.