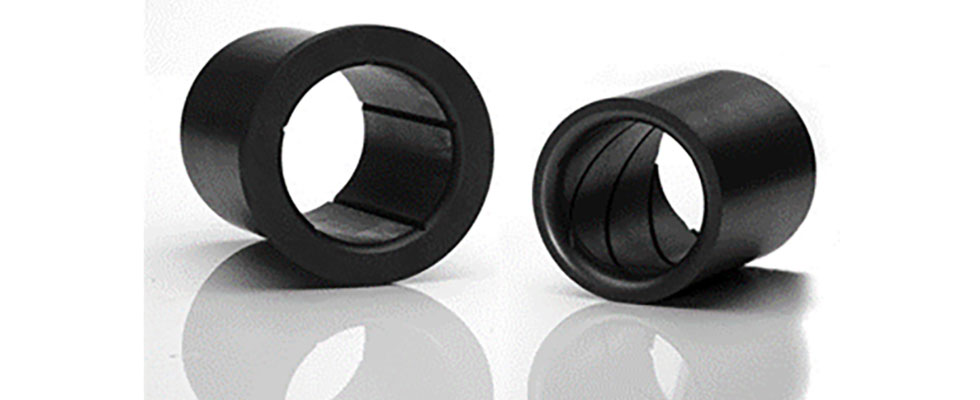
Petroleum products propel vehicles, heat buildings and produce electricity. In 2021, United States petroleum consumption averaged about 19.78 million barrels per day, which included about a million barrels of biofuels. Oil and gas products are integral parts of societies’ infrastructure. Carbon graphite has a combination of properties, allowing it to be used in rotating equipment and its components such as mechanical/dry gas seals, pump bearings, valve seats, generators and compressors to produce, distribute and move oil and gas.
The first property of using carbon graphite is its temperature resistance. Whether that be high temperatures such as 350 F to 1,100 F in oxidizing environments and up to 6,000 F in nonoxidizing environments, or cryogenic temperatures ranging from -30 F to -450 F, these materials have a low coefficient of thermal expansion, meaning the size and shape of the material do not drastically change with a temperature change.
A distinguishing property of carbon is its corrosion resistance to hundreds of chemicals. These include, but are not limited to, benzene, sulfur dioxide, petroleum, formaldehyde, hydrocarbons and mercury. Carbon graphite is an allotropic form of carbon. Carbon atoms are bonded together in a hexagonal pattern by covalent bonds and form graphene layers. These bonds are strong, making attacks by other chemicals difficult. Graphite is considered more inert than other elements and forms of carbon.
Carbon graphite also has self-lubricating characteristics. The graphene layers are bonded together by Van der Waals forces. These are weak attractive forces between atoms. Unlike ionic or covalent bonds, these attractions do not result from a chemical electronic bond; they are comparatively weak and therefore more susceptible to disturbances.
Allowing the graphene layers of carbon graphite to rub off against the mating material filling the surface roughness and creating a hydrodynamic film essentially allows the graphite to run against itself. This self-lubricating ability gives the material the ability to not seize or gall in dry operating conditions. Since it is self-lubricating and has thermal and electrical properties, carbon graphite material is also non-sparking. The spark is referred to here as a mechanical or frictional spark.
A final property of carbon graphite is the available porosity in the material from the baking process. After mixing and molding raw carbon constituents consisting of carbon powders and binders, the green material is sent through a controlled, oxygen-free baking process to carbonize the pitch binder, thus hardening and turning it into amorphous carbon.
During the baking process, outgassing occurs, meaning hydrocarbons in the pitch are driven off due to extreme heat, leaving an amorphous carbon structure. During outgassing, these gases push their way out of the material, leaving behind a network of interconnected porosity. This porosity gives carbon manufacturers the ability to impregnate the material with various types of metals, resins and salts, which can either enhance or add additional mechanical/chemical properties to the carbon graphite. The next portion of this article will detail impregnated carbon graphite’s used for products and applications in rotating equipment.
High Temperature Valve Seats
A ball valve is a shutoff valve that controls the flow of a liquid or gas. It does this by using a ball with a cylindrical hole in the middle. When the ball valve is open, the hole in the ball valve is aligned with the pipe to allow the media to flow through.
In the closed position, the valve is rotated 90 degrees. One component that can be made of carbon graphite is the valve seats. They sit cupping the ball. Sealing occurs when the upstream pressure increases, pushing the ball and the upstream seat in the direction of flow toward the downstream seat.
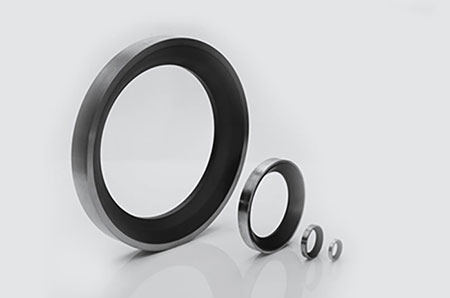
The impregnation commonly used for carbon graphite in this application is coke. Coke is the solid residue remaining after bituminous coals are heated to a high temperature. The residue is chiefly carbon, has few impurities and has a developed graphitic structure.
Coke gives the base material better oxidation and chemical resistance. As a result, the material’s physical properties remain the same in extreme application conditions. This material helps fire safety valves meet the American Petroleum Institute (API) 607 standards.
Pump Bearings
There are a variety of pumps, ranging from centrifugal slurry pumps to vertical submersible pumps. With each having different running parameters, carbon graphite is an optimal solution for pump bearings. The function of the bearing is to support a moving shaft. An example of a centrifugal pump is a vertical turbine pump. These pumps move fluid, oil as an example, from a deep underground reservoir to ground level.
The type of impregnation needed in carbon graphite depends on the type of pump and the physical conditions that the bearings will be exposed to. Many types of impregnations exist. Two, in particular, have proven to perform well in a wide range of pump applications. These are babbitt and nickel. Babbitt is a soft metal with robust lubricating properties. It is the best for low-temperature water applications where the bearing is running submerged. Nickel-impregnated carbon graphite is strong and has the best corrosion resistance. It is common in pumps experiencing high loads and temperatures.
Dry Gas Seals
Dry gas seals are types of mechanical seals that are noncontacting and dry running. They contain seal faces that consist of a mating ring and a primary ring. The mating ring is rotating, while the primary ring stays stationary. They use different chemicals than other mechanical seals so they do not cause contamination. These seals are in harsh working environments such as oil exploration, extraction, refining and gas transmission.
The primary ring component is usually made from carbon graphite impregnated with antimony. Antimony adds stiffness and impermeability to provide an air cushion. It also is stable at a wide temperature range allowing it to encounter chemicals such as hot oil and hydrocarbons in temperatures up to 700 F, or with liquid oxygen/hydrogen in temperatures as low as -450 F.