
Selecting a pump can be challenging. There are a broad range of options per application. Each type of pump offers key advantages and disadvantages that must be closely considered. This article serves as a general overview of some of the more common pumping technologies and the pros and cons of selecting each type of pump per application.
There are many factors that contribute to defining which pump works best per application. It is important to first outline your goals and design intent for your project. The cost of downtime plays a major role in decision making. Often one hour of downtime can be the cost of a new pump. In these cases, sticker price is less important than pump reliability. In other less critical applications, the pump price, operation costs and reliability are more influential in determining which pump provides the best value.
Two other key factors that influence pump selection are fluid properties and process conditions. Viscosity, pressure, flow rate, density, chemical compatibility, temperature range, vapor pressure, suspended solids, dissolved solids and consistency are all variables that should be considered during pump selection. There are also more abstract considerations unique to each application such as:
- the product being shear sensitive or prone to foaming
- the product having a risk of igniting
- or exploding
- the process fluid requiring high purity materials and finishes
- the application requiring
- clean-in-place pumps
- any environmental or safety risks
Positive Displacement vs. Centrifugal Pumps
Once all project details are understood, the next step is to decide which type of pump is the best fit for the application. For a novice, the sheer number of pump technologies can be overwhelming. It is important to first understand the difference between positive displacement (PD) and centrifugal pumps and when to use each technology.
The conventional definition states that a PD pump captures and transfers a fixed amount of fluid per cycle. A centrifugal pump imparts velocity onto fluid through rotational force. This is not incorrect but also not useful to the average application engineer. A more practical difference is that centrifugal pumps have a high level of volumetric slip, causing them to limit pressure output. As centrifugal pumps experience more pressure downstream, they produce less flow. While this also can be true of PD pumps, they tend to experience significantly less volumetric slip, allowing them to push past line resistances at little to no change in volumetric displacement. Pressure will continue to increase until a secondary limiting component relieves pressure, or the pump motor overloads.
As a result, centrifugal pumps generally favor higher flow rate applications with low–medium pressures. Also, centrifugal pumps require thinner fluids, generally below 500 centipoise (cP). It is recommended to consult the pump manufacturer if the process fluid exceeds 200 cP. While some PD pumps can physically achieve the same flow rates as centrifugal pumps, it can become cost prohibitive at higher flow rates. These pressure generation characteristics also require a higher degree of safety considerations to prevent catastrophic over pressurization.
PD pumps excel at pumping viscous fluids. It is not uncommon for a rotary PD pump to provide 100% volumetric displacement at viscosities above 500 cP. PD pumps are also frequently used in low viscosity ranges, generally at low flow rates and higher pressures. Additionally, PD pumps are the primary selection for applications that require precision
metering or dosing.
PD Pump Selection
If the decision has been made that a PD pump is the best selection for a particular application, the next step is to narrow down which type of PD pump to choose. PD pumps are further broken down into two categories: reciprocating and rotary pumps. Reciprocating pumps displace fluid by a diaphragm, piston or plunger moving in a linear motion. Check valves are required to set the direction of flow. Conversely, a rotary pump uses a motor driven rotor or multiple rotors to displace fluid.
Most piston and plunger pumps are used for high pressure, lower viscosity applications. Diaphragm pumps tend to cover a broader range of products at lower pressure thresholds. Given the linear nature of the pumping mechanisms, it is more common to use compressed air to drive reciprocating pumps. However, motor driven reciprocating pumps adapted with cam shafts are used as well. Plunger and piston pumps perform well in applications that require high pressure flow through a nozzle (paint sprayers, pressure washer, inline cleaners, glue application).
Rotary PD pumps have a broader range of pump types. Image 1 displays common types of rotary PD pumps. These pumps are generally differentiated by rotor and stator/housing designs. These pumps have little to no clearance between rotor and housing or stator. Vane, eccentric disc, progressive cavity (PC) and peristaltic pumps are all designed to have contacting rotors/vanes. This attribute allows these pumps to better displace a liquid with lower viscosities. PC pumps are particularly versatile, as they can displace high to low viscosity products, with considerable suspended solids, devoid of pulsation. Some peristaltic pumps offer all the same advantages except they provide a moderate degree of pulsation and require routine hose replacement. An added advantage of a peristaltic pump is that some designs can run dry. It should be noted that a limitation of contacting components is wear and heat generation from friction. For this reason, it is important that PC and eccentric disc pumps that process fluid have some lubricity.
Internal gear, external gear, lobe and circumferential piston pumps all contain two or more rotors designed with internal clearances. Gear pumps do not require timing gears, as the rotors are used for both fluid displacement and rotation of the idler gear(s). For this reason, they are generally lower cost and simpler to maintain. Internal and external pumps tend to experience shorter life when used to pump fluids that contain various types of suspended solids, especially abrasive slurries, because of their internally lubricated bearing design. Internal gear pumps excel at pumping extremely viscous materials, while external gear pumps are more effective at higher pressure and lower flow applications, often used as metering pumps.
Lobe pumps are designed to operate better with suspended solids. They have a smooth contour which also makes them a good fit for hygienic applications. Many lobe pumps have high clearances which limit their ability to accurately displace low viscosity products at lower speed ranges. Circumferential piston pumps are an innovation of traditional lobe pumps. The clearances are much tighter, allowing for considerable improvement in pumping low viscosity products. It is important to note circumferential piston pumps are limited in high temperature applications because thermal expansion can cause the low tolerance rotors to contact the housing and seize the pump. Manufacturers have remedied this by offering hot clearance rotor options that increase tolerances on high temperature applications.
Centrifugal Pump Selection
Centrifugal pumps are prevalent and, like PD pumps, they come in a variety of designs. They are well-understood, easy to maintain and adaptable.
Some of the common types of centrifugal pumps are end suction, split case and multistage pumps. End suction pumps are the most widespread of all centrifugal pumps. Many OEMs offer multiple impeller and volute options to suit a broad range of applications. Often, end suction pumps are fitted with open face impellers because of their ability to pump moderated suspended solid concentrations while still providing favorable net positive suction head required (NPSHr) performance. Because of the simplistic design, end suction pumps tend to be lower cost and easier to maintain.
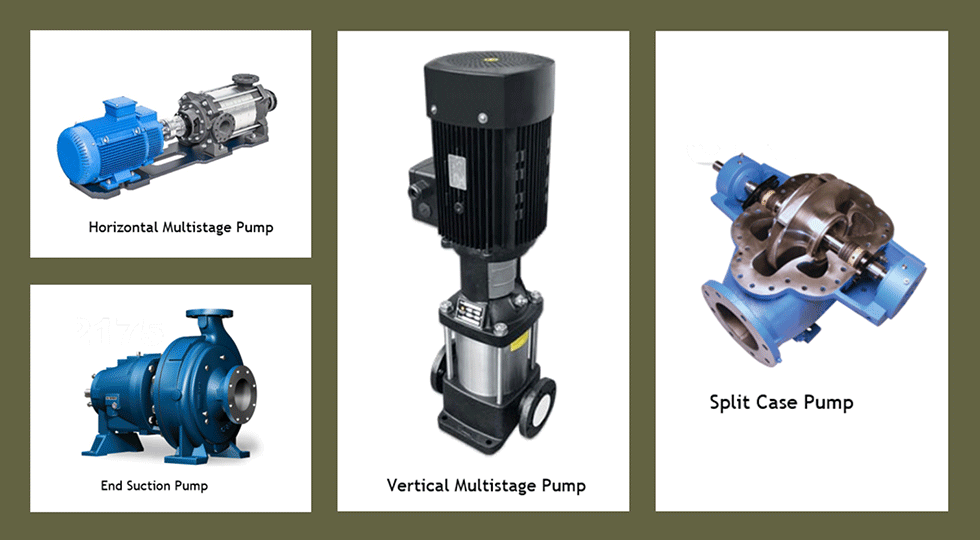
Split case pumps are better suited for higher flow rates. For clean fluids, these pumps tend to offer better efficiency and reliability. Because split case pumps have fully enclosed impellers fitted with wear rings, they are less ideal for fluids containing suspended solids. They can be more challenging to maintain and often come at a higher up-front cost.
Multistage centrifugal pumps contain multiple enclosed impellers configured in series to allow for higher pressure capabilities. Boiler feed, irrigation and water booster systems are a few examples of where these pumps are utilized. As these pumps increase in size, they become expensive and difficult to maintain. Multistage pumps are available in both vertical and horizontal configuration.
Understanding how to properly select pumping technologies can have a major impact on system operation. This article only touches on some general principles and is meant to encourage a deeper dive. into each pump technology.