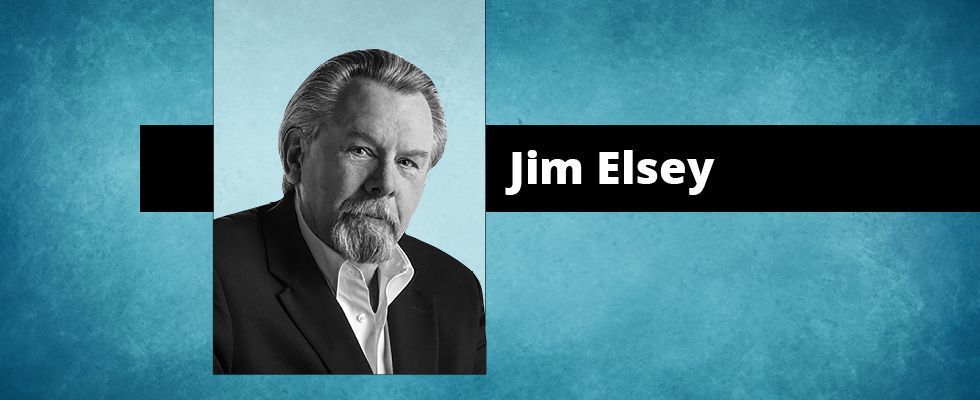
Parts 1 and 2 of this column ran in the February and March issues of Pumps & Systems, respectively.
Special Suction Side Issues
Normally the pump suction piping is going to be at least one size larger than the pump suction nozzle. Parallel pumps will present requirements for even bigger pipe sizes. This is mostly to accommodate both the velocity and net positive suction head available (NPSHa) friction loss requirements. An exception may be a self-primer suction line where users are more concerned with the amount of time required to prime the pump. The larger the suction line, the more air to be evacuated—which translates into additional time that the pump operates without liquid flow. Excessive priming time is not a desired condition as the recirculation overheats the priming chamber fluid, and the mechanical seal may not be properly lubricated or possibly overheat depending on the individual pump design.
There are other issues, besides the wrong size suction pipe, that translate into excess friction and unbalanced swirling flow profiles. The best practice is to reduce or eliminate the turbulence and uneven flow velocity profiles. Note that double suction pumps are even more susceptible to these issues than other designs. The most common issues include the following:
- the use of pipe tees where a Y fitting would be better
- the use of a short radius 90-degree elbow in lieu of a long radius
- using a 90-degree elbow where the use of two 45-degree-spaced elbows is better
- using two or more elbows in proximity to each other and the pumps that are in different planes (at right angles to each other). This creates a swirl or corkscrew in the velocity profile.
- using suction pipe that is smaller than the pump suction nozzle size
- using flow disturbing fittings and components that are the same pipe size or smaller than the suction pipe itself
- the drastic transition from one pipe size to another without the use of a properly designed transition piece
- sharp-edged pipe profiles in lieu of generous radius or bell shapes
- misaligned pipe flanges that create internal flow eddies and vortices
- the use of a horizontal elbow, valve or strainer directly on the suction of the pump
- improperly sized suction side supply vessels, which translates to inadequate retention time, low pressures and high friction. At an absolute minimum, the retention time of any suction tank should be more than two minutes, and I highly suggest four or more minutes as a best practice.
A comment regarding piping integrity and the associated (flange) connections: Please appreciate that they must be air tight, especially on lift applications. Recognize that the pressure inside the pipe will be below ambient (think vacuum). Just because liquid is not leaking out does not mean that air cannot leak into the pipe.
Eccentric & Concentric Reducers
This section is specifically in reference to the suction side of the pump as we will save discharge side pipe size increaser practices to another column. I have witnessed numerous, heated and long discussions/arguments on this subject. I will address the subject briefly.
There are two main points, and then I will pose a third idea as a paradigm shift. The first is whether or not it is proper to use a concentric reducer on the suction side of the pump, and the second is when using an eccentric reducer, which way should the flat side be positioned?
Concentric reducers have not been used to a large extent on horizontal pump suction piping, ostensibly due to concerns with air entrainment and the consequential flow blockage. Realize that air pockets act as blockages and restrict flow just as if a partially closed valve or orifice was placed in the line. I believe that concentric reducers are perfectly acceptable in vertical piping as the concern for air entrapment is typically negated by the orientation and geometry in addition to being swept by the fluid velocity. A more controversial topic is the incorporation of concentric reducers in the horizontal plane on the suction line of pumps. I will point out that I have observed numerous and successful applications of concentric reducers on the pump suction approach. The users are not experiencing issues with air entrapment, though in most cases there is either a manual vent or automatic air release valve (ARV) installed in case air or gas does need to be vented.
This paradigm shifting philosophy with horizontal concentric reducers is that the liquid velocity in the pipe facilitates the transportability of any air and noncondensable gases. The added advantage of the concentric reducer choice is that the liquid velocity profile downstream of the reducer is symmetrical unlike that of an eccentric reducer. I concur that hypothetically the overall velocity of the liquid can transport (sweep) any air and noncondensable gases along the stream in lieu of being trapped at the transition. Before making this decision, conduct a computational fluid dynamics (CFD) analysis. Additionally, I suggest avoiding the use of concentric reducers in situations where the pump is at a higher elevation than the suction supply source and/or the liquid properties are known to include the entrainment of air, vapors and noncondensable gases.
Eccentric reducers are commonly used for the transition of a larger-size suction pipe to the smaller pump suction nozzle. Everyone asks me which way should the flat side be positioned? I offer my two cents as follows and also add the caveat that “it depends.” If the supply source is from (immediately) above the pump, the flat side should be on the bottom to allow air and gas to escape back toward the suction source. If the source is from either below or from a horizontal long run (more than 4 to 5 diameters) prior to the pump, then the flat side should be on the top.
A more important and often overlooked detail is the angle of the eccentric reducer transition piece—or think of it as the rate or ratio of reduction. I recently witnessed several installations (with pump issues) where the eccentric reducer angle was high and in excess of 25 to 30 degrees (15 degrees should be the maximum angle). I have frequently seen these types of issues when the diameter reduction is over several pipe sizes: for instance, from 10 inches to 4 inches. The misguided thinking is that a reducer is a reducer and the designer is not concerned with how it happens and the rate of reduction.
These instances would be far better off with either a two- or three-stage reduction with some straight pipe in between them or a larger (longer) more gentle transition of less than 15 degrees on the reducer. The “thumb rule” might be to transition down one size at a time—for example from 10 to 8 inches, then to 6, and then to 4 inches, which would be three transitions.
Another tip in addition to keeping the angle less than 15 degrees is to consider the ratio of the reduction. Think of this ratio as (D1 - D2) ÷ L (where D is the pipe diameter and L is the length of the reducer).
Finally, I strongly propose that we (the industry) cease the practice of placing eccentric reducers immediately adjacent to the pump suction flange. Eccentric reducers create uneven flow velocity profiles at the outlets. Suppose the flat side is on top for my eccentric reducer example, and so the liquid flow entering the reducer near the top will have a straight run to the outlet, which is no problem. However, the flow entering the reducer at the bottom has a longer route to run, and so it must speed up and, therefore, exits the reducer at a higher velocity (refer to Bernoulli’s equation for the science and conservation of energy explanation). My proposal for a better installation is to place the eccentric reducer outlet at least 4 to 6 diameters away from the pump suction nozzle and to use a straight and unobstructed section of pipe between the reducer and the pump to allow the velocity profile to correct and realign itself to symmetry.
As for the pipe, it is not just about the safety and efficiency of containing the fluid as it moves from one point to another. More importantly, it is also about what is happening inside the pipe. The symmetry of the velocity profile and friction factors are what you should be additionally concerned about. To ignore or dismiss these factors will add significant costs to operate and maintain the pump in the long run.
References
1. Rotodynamic Pumps for Pump Piping ANSI/HI 9.6.6 2016
2. Centrifugal Pump Users Guidebook (Problems and Solutions) by Sam Yedidiah
3. Pump Handbook 4th edition by Paul Cooper, Igor Karassik, et al
4. Institute for Pumps and Mechanical Seals by William (Bill) J. McNally (SS)
5. Review pump suction reducer selection…, Vol 56 No. 3 October 2014 of Journal of South African Institution of Civil Engineering, by Ross Mahaffey (PE) and S.J. Van Vuuren (PE)